Abstract: With the continuous improvement of productivity of extrusion production line main unit, the capacity of its downstream equipment shall also be continuously improved to fulfill the requirements. This section introduces the method that Dekuma solves the problems of difficult adjustment of the cutting machine feed mechanism and difficult control of the feed speed with TRIZ innovative theory.
Keywords: TRIZ extrusion line Cutting Machine
01 The main problems of commonly-used feed mechanism in the industry
The feed mechanism of the cutting machine commonly used in the industry meets the processing requirements of the feeding and retracting with a group of hydraulic pump, supply hydraulic oil to hydraulic cylinder to control the swing movement of tool arm.
To cut pipes with different diameters and different wall thicknesses, firstly, it needs to adjust the initial feeding position, and meanwhile, it also needs to effectively control the feed amount of the tool arm; on the other hand, the feeding length is generally controlled by the cylinder stroke, and the initial position of the feed is controlled by adjusting screw of hydraulic cylinder support assembly.
In addition, for different cutting methods, the feeding speed shall also be controlled. The feeding speed is realized by adding the flow control valve in hydraulic circuit. If the speed is too fast, it will easily damage the cutting blade or saw blade.
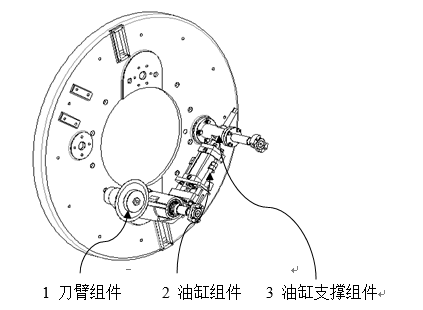
(1)Difficult to adjust the initial position of tool arm
The initial position of tool arm shall be adjusted by adjusting screw of hydraulic cylinder support assembly. It needs to loosen or tighten the lock nut and rotate the adjusting screw. Due to lack of suitable marking scale, it can only perform the action of feeding and retreating after preliminary adjustment, observe whether the cutting thickness can be completed, and finally lock the adjusting screw. However, when adjusting with this method, the working space is limited, and adjustment is very inconvenient.
(2)Difficult to control the tool arm feeding speed
The feed of tool arm is adjusted by the flow control valve, and it is difficult to obtain a suitable feed speed. The speed is easy to become too fast or too slow. The operators shall adjust the appropriate feeding speed for many times, which requires high technical level of the operators.
(3)Slow feeding speed
The feeding speed has only one speed when passing through the flow control valve, especially under working conditions with relatively slow feeding speed, the tool arm takes more time in approaching stroke. Taking the 40mm feeding stroke as an example, 20mm is approaching stroke, which requires 30s; the remaining 20mm working stroke also takes 30s, and it takes total 1min to complete the cylinder stroke.
02 Solve problems with TRIZ theory
The TRIZ theory was first proposed and summarized by the Soviet scientist Genrich S. Altshuler. TRIZ theory contains many systematic, scientific and operational creative thinking methods and analytical methods for finding problems. After years of development, TRIZ theory has become a mature classical theoretical system for solving practical problems in product development.
The general method of TRIZ theory to solve problems is that, first, abstract the special problem to be solved into a standard problem; then obtain a general solution based on the methods and tools provided by TRIZ theory; finally, obtain the final solution based on the user’s experience.
Heavy Duty Chipless Cutting Machine DKM-PO450
(1)Find and analyze problems – abstract into standard problems
Based on the analysis of the actions of feed mechanism, Dekuma’s engineering team conclude that in the approaching stroke, the feeding speed is expected to be faster, to reduce the feeding time and improve efficiency; while in the working stroke, the feeding speed is expected to slow down. On the one hand, it is aiming to reduce the load resistance of hydraulic cylinder; On the other hand, it is to reduce the rigidity requirement of the whole mechanism, and to improve the service life of the blade. From this analysis, the feeding speed shall be combined fast and slow, forming a pair of physical contradictions.
(2)Conduct resource analysis to find out contradictions
Four separation principles are summarized with TRIZ theory according to space, time, condition and system level, which are space separation, time separation, condition separation, and whole-part separation.
Among them, the principle of time separation is to separate the conflicting parties in different time periods, aiming to solve the problem or reduce the difficulty of problem. Based on analysis, Dekuma’s engineering team solve the problem of different speeds required by feeding speed at different times with this principle.
Comparing the corresponding 12 innovative principles in the principle of time separation, the “fast principle” that completes harmful operations at the fastest speed serves as the most effective one of the 12 innovative principles. For the feed mechanism, slow approaching travel can be considered as a harmful operation, which is very harmful to the improvement of efficiency.
(3)Problem solving
To quickly complete the harmful operation, the “fast principle” is adopted to solve the problem of approaching stroke. Dekuma introduces a deceleration cylinder, which quickly feeds and oil return to complete the action during approaching stroke. When it comes to the working stroke, the oil return of cylinder reduces the speed of working stroke by decelerating to meet the process requirements.
03 Main advantages of the new segment-controlled feed mechanism
To solve the problems encountered by commonly used feed mechanism in the industry, achieve the convenient operation of the extrusion production line, and reduce the cycle time required to replace different pipe specifications, Dekuma’s engineering team has developed a new segment-controlled feed mechanism, with the main advantages and principles as follows:
(1)Fast adjustment of tool arm initial position
The position of tool arm can be adjusted quickly by way of clamp-type tool arm assembly. The operation method goes as follows. Loosen the fixing screws of the clamping block, and swing the tool arm quickly to the marking scale line of the required specification according to the scale displayed on the sign, and then tighten the fixing screws of the clamping block. The initial operation of tool arm position adjustment is thus completed.
(2)Control the oil via deceleration cylinder
Therefore, two stages of fast and slow feed speeds can be achieved. Fast feed is adopted during the approaching stroke, and slow feed is adopted during the working stroke, which can effectively reduce the feeding cycle of tool arm. Taking the 40mm feed stroke as an example, 20mm is the approaching stroke, the time required for fast feed in the approaching stroke is 1s, and the time required for slow feed in the working stroke is 30s, and it takes total 31s to complete the whole stroke, which can save approx. half time of the original mechanism.
(3)Springs configured by deceleration cylinder and feed cylinder
The hydraulic cylinder can be reset actively, allowing the action of tool retracting to be completed faster, which further reduces the time of the whole process and improves the stability of actions.
04 Various processes of tool feed and retracting – description of actions of feeding cylinder and deceleration cylinder
(1)Fast feeding speed
The oil flow to no rod cavity of feeding cylinder, and the rod cavity cylinder returns oil into the deceleration cylinder. Before the piston of the deceleration cylinder reaches the limit position, the piston can move quickly, and the return oil of piston enters the hydraulic tank via valve body.
(2)Slow feeding speed
After the piston of deceleration cylinder moves forward and gets contact with the limit point, the piston will stop, and the oil can only return to the hydraulic tank via throttle valve. Thus the forward speed of the cylinder is reduced significantly, and it enters the slow-speed stage until the feed reaches in position.
(3)Fast retract speed
Both the deceleration cylinder piston and the hydraulic cylinder are set with return springs. The oil passes through the deceleration cylinder piston and quickly pushes the deceleration cylinder piston back to its original position driven by the spring’s reset thrust. Also acted by the spring force, the oil cylinder realizes fast return action.
(4)Retract in place
After the piston of the deceleration cylinder returns in place, the oil passes through the check valve. The piston installs with a check valve, allowing the oil to quickly pass through the piston, enter to rod cavity, and push the tool arm to return to the origin position quickly.
05 Conclusion
By applying the invention principle of TRIZ theory, Dekuma has proposed the idea of solving the problem of feed segmented control, which improves the action performance of feed mechanism cylinder and the time of each process.
The new segmented-control feed mechanism developed by Dekuma doubled the feeding speed, and ensured the stability and reliability of the retracting action. The cutting machine, as part of the extrusion production line, can better match the productivity of the entire production line!