150m/min! Dekuma Sets New Record for Microduct Extrusion Speed
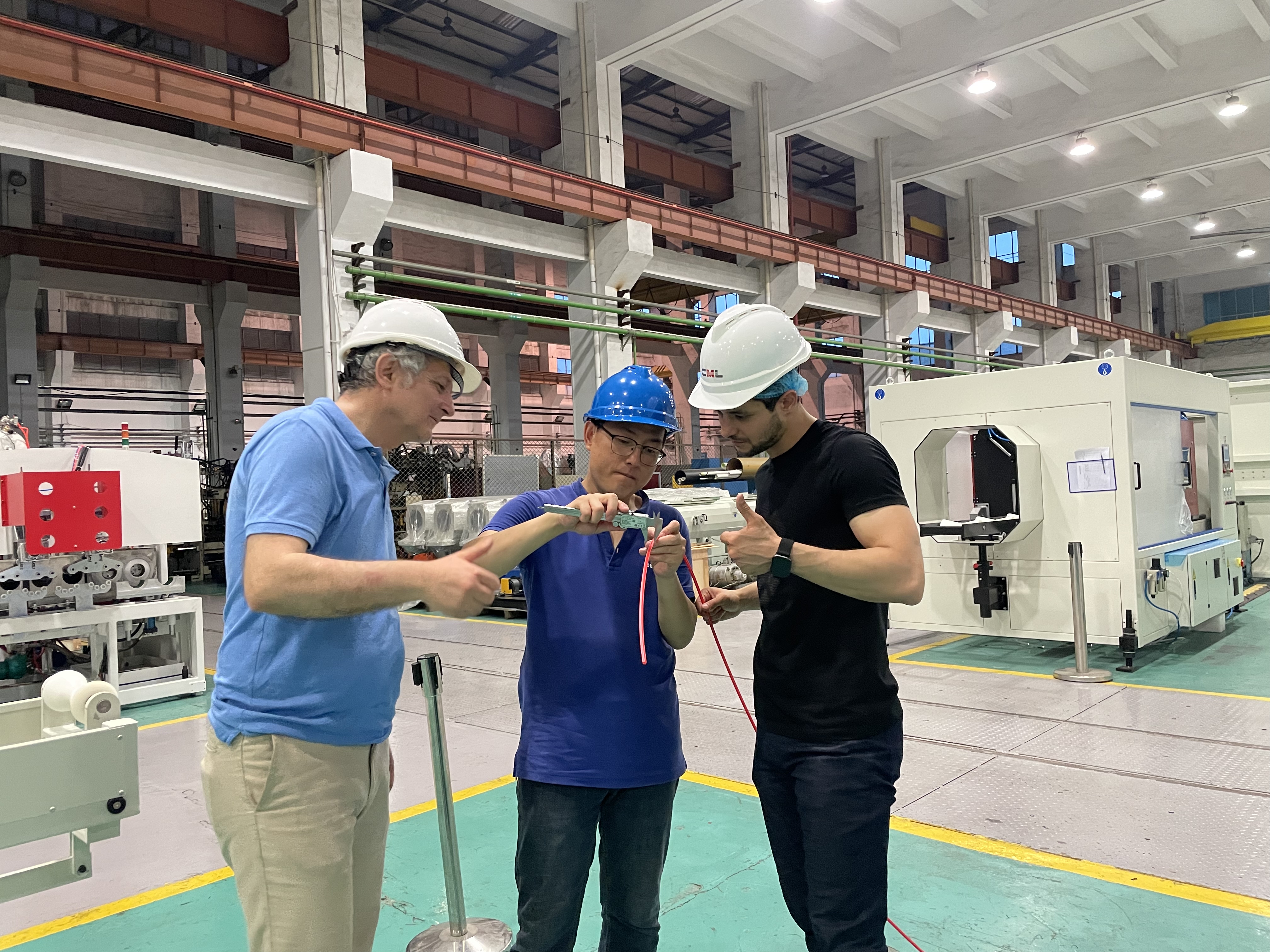
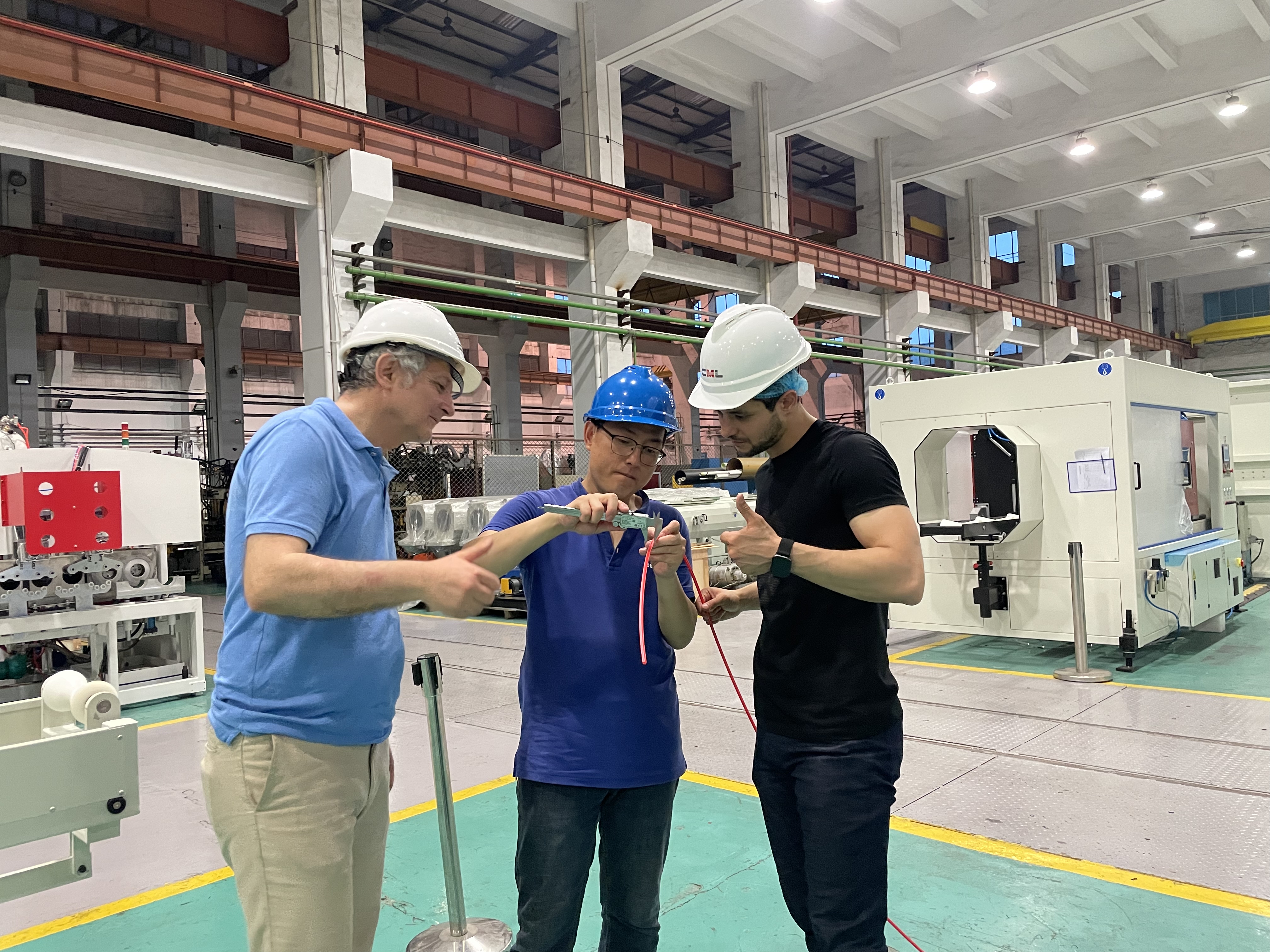
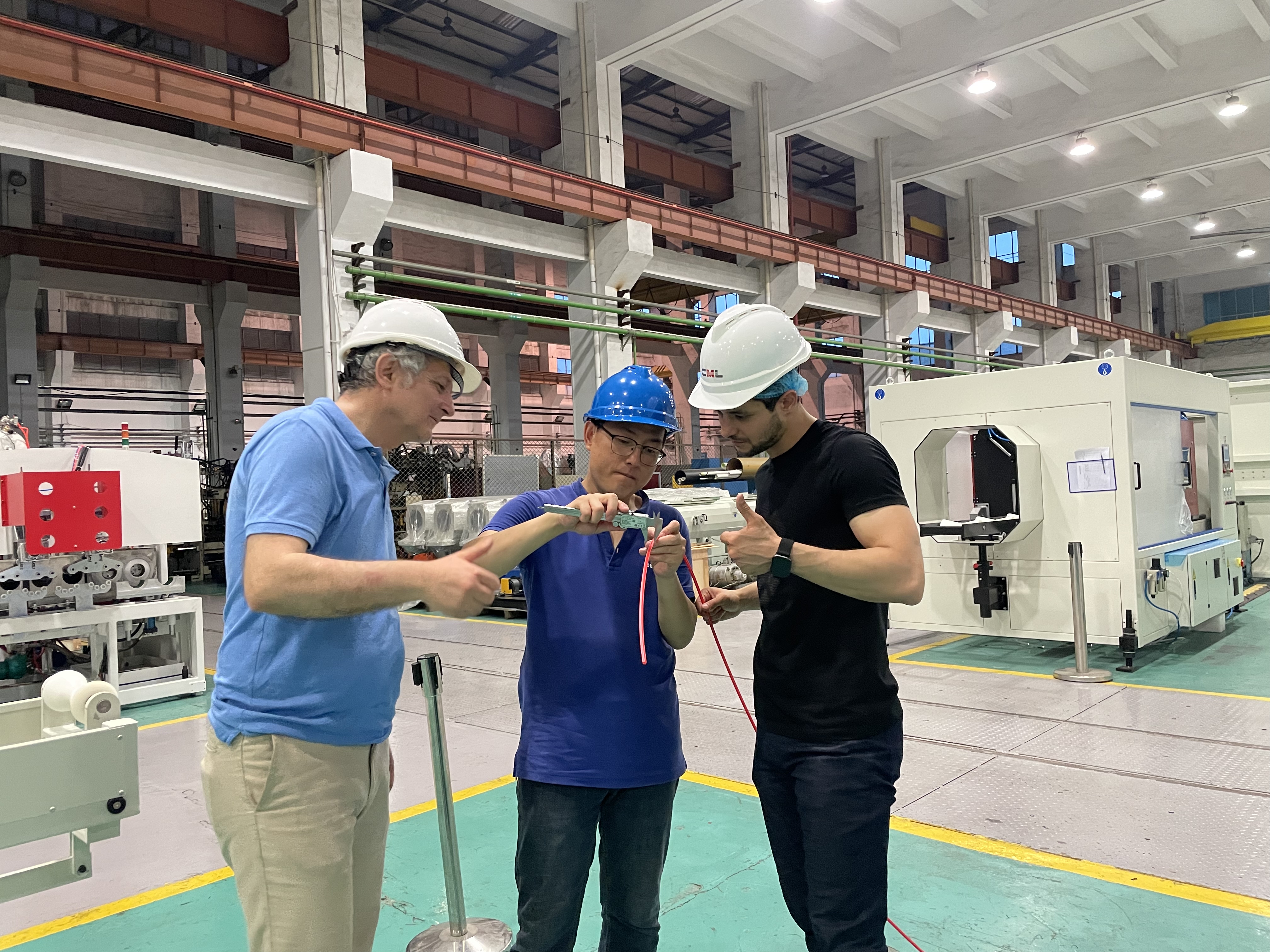
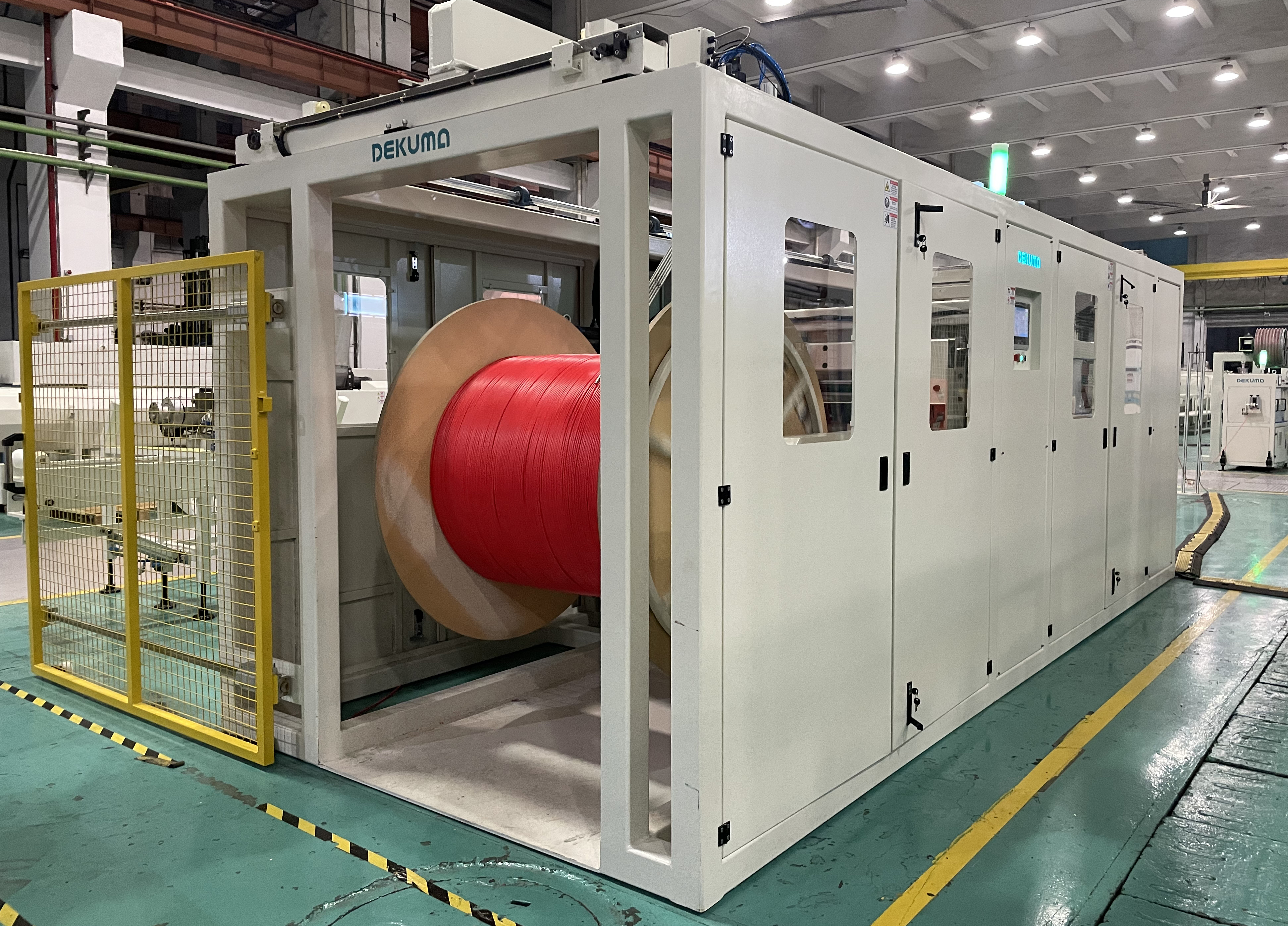
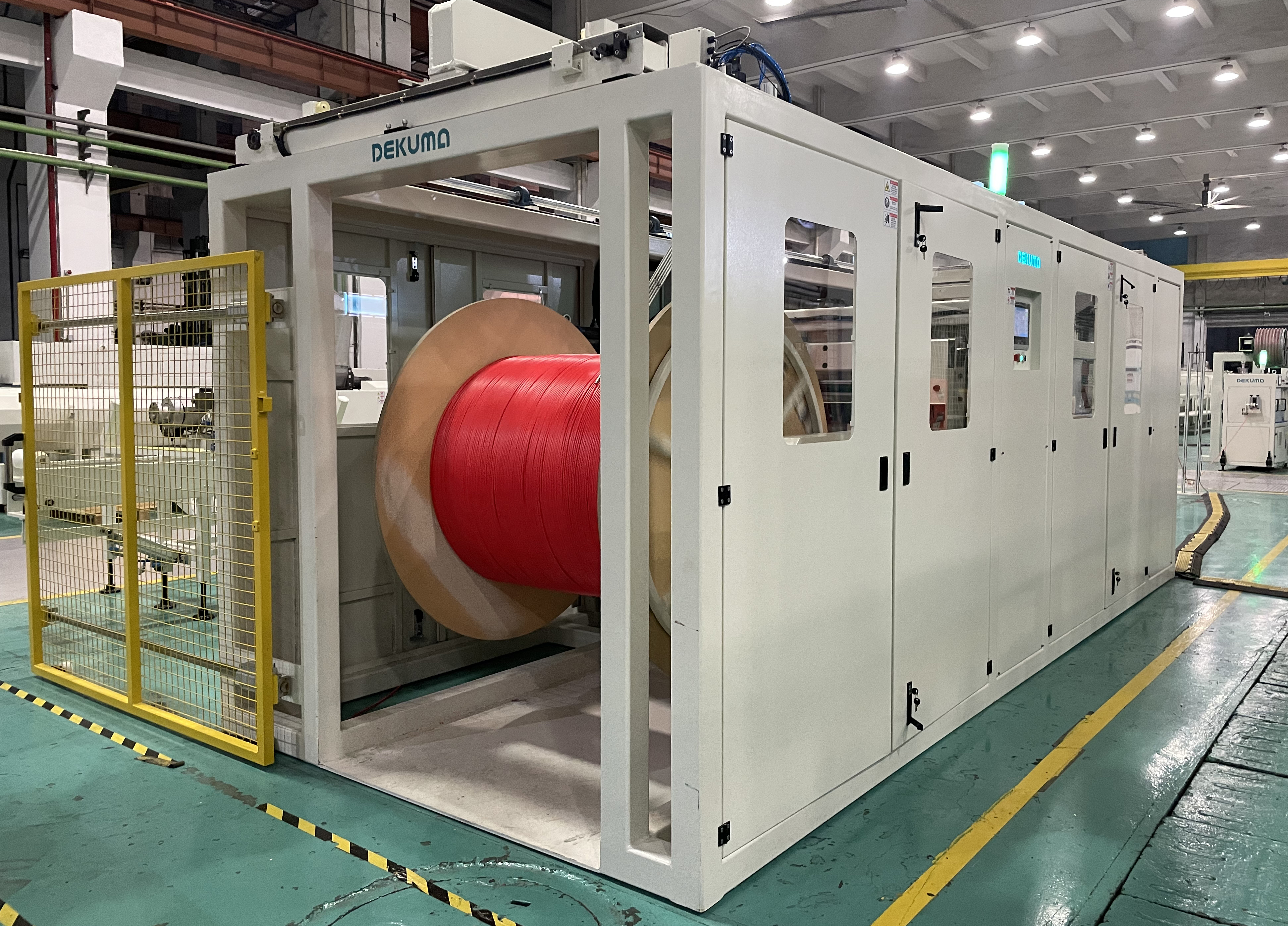
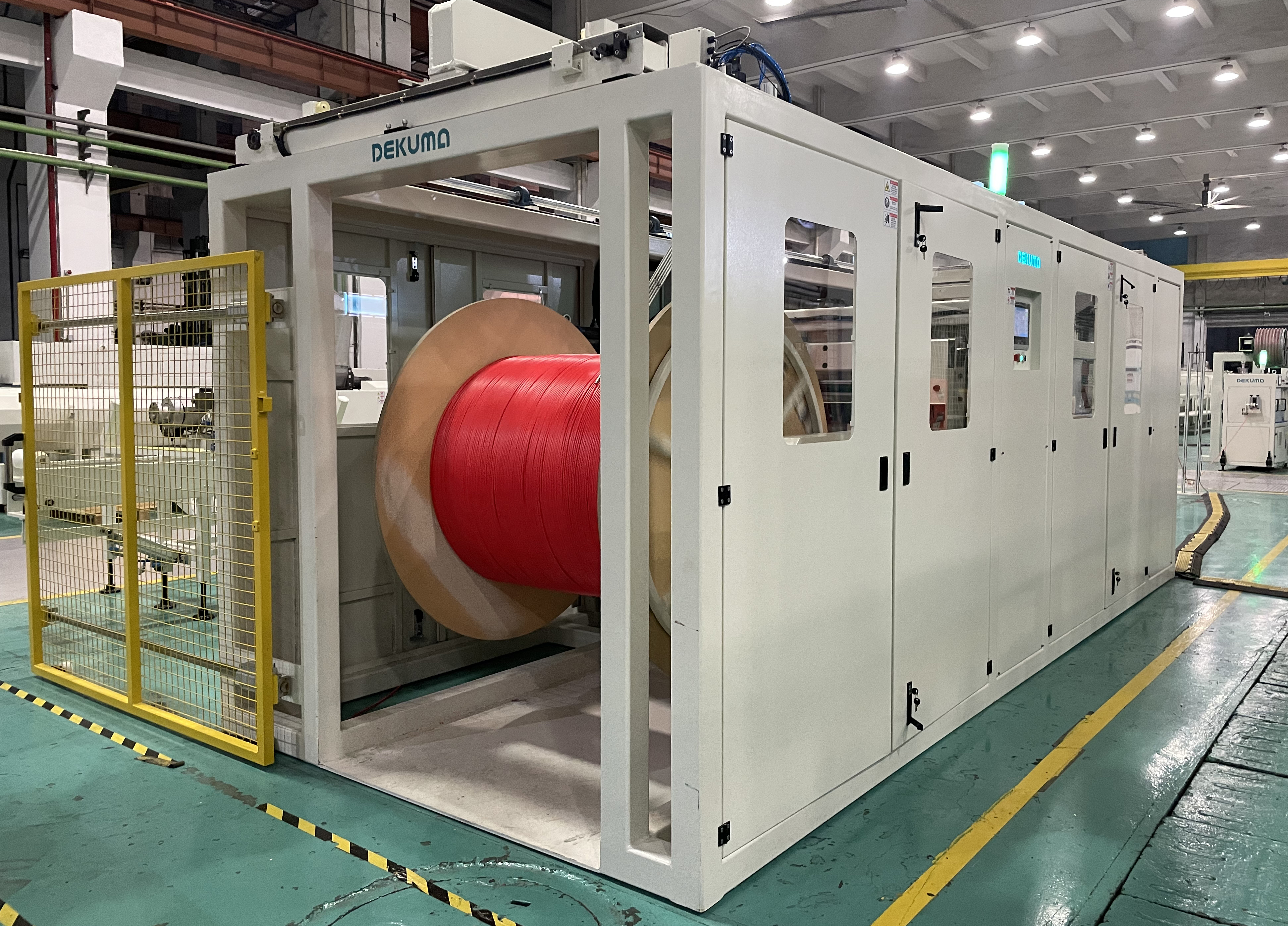
1, Optimize production processes and increase production capacity.
The highest production speed of this line when producing 14mm microtubes can reach 100m/min.
During the entire line test process, the highest production speed of 7mm microtubes reached the expected goal of 150m/min, and the real-time detection of various product indicators met the requirements of the European customers who visited the site.
2, Automated configuration and efficient winding.
The entire line integrates automated control and is equipped with a dual-position automatic rewinder, greatly improving the degree of automation.
3, Provide a complete set of production solutions to save time and effort.
DEKUMA provides users with a complete turnkey solution, with production line plans for all specifications of microducts and various structural bundle tubes.
DEKUMA insists on survival through quality and development through innovation, providing users with better products and services.
The technology of DEKUMA’s microduct production line has reached the leading level in the industry and can meet users’ requirements for high output, high speed, and high efficiency equipment.
At the same time, automated control realizes convenient operation of equipment, reduces dependence on manual labor, and provides a one-stop service for users with a complete set of production solutions, making it the first choice for project investment and equipment upgrades for domestic and foreign customers.
Dekuma’s solution to composite insulator production issues
With the emergence of polymer materials, ceramics and glass are no longer the preferred insulation materials. European and American countries have started to research polymer insulators, studying the physical and electrical properties, long-term reliability, and optimal shapes of electric insulators, leading to continuous improvement in productivity.
Among the polymer materials that can replace ceramics and glass, silicone rubber has more advantages than other polymers. Composite insulators, which are made of silicone rubber, are used as insulators for power lines and are mainly used in substations.
Dekuma not only has many years of experience in independently researching and developing machines, but also has an experienced team that understands the product manufacturing process. This special machine, which was developed by our over 25 years of experience engineering and technical team and adheres to German manufacturing standards for insulator production, is highly recognized by customers in the niche market due to its high efficiency, stability, and wide applicability.
“Composite insulator rubber machine”
production of finished products
What exactly makes the performance of this special machine for composite insulators so powerful?
1、Low-platform designed for easy operation
The low-platform design provides comfortable operating height, facilitates equipment operation and layout, and eliminates the need for foundation pits. The fully automatic injection system eliminates tedious steps such as material weighing and filling, reducing labor intensity. The professional design of the cold runner system saves materials and improves production efficiency.
2、Stability and durability
The bolster is thick, with good anti-deformation performance and durability, resulting in small burrs on the produced items. Equipped with imported electrical and hydraulic components, enhances the stability and reliability.
3、Multi-purpose machine with wide range of applications
Developed specifically for insulators, it can cover all specifications from 10kV to 550kV, and is a multi-purpose machine with a wide range of applications.
Dekuma has always focused on “technological innovation” as its development direction, continuously deepening its presence in niche markets, and improving its brand influence and industry competitiveness.
At the same time, Dechom will continue to strengthen communication and cooperation with users, deeply understand their needs, improve user satisfaction and trust, and provide users with higher quality, intelligent, and environmentally friendly products and services, making greater contributions to the development of the insulator industry.
High Precision Make High Quality | Dekuma Rubber Injection Machine for EVs Sealing Corner Jointing
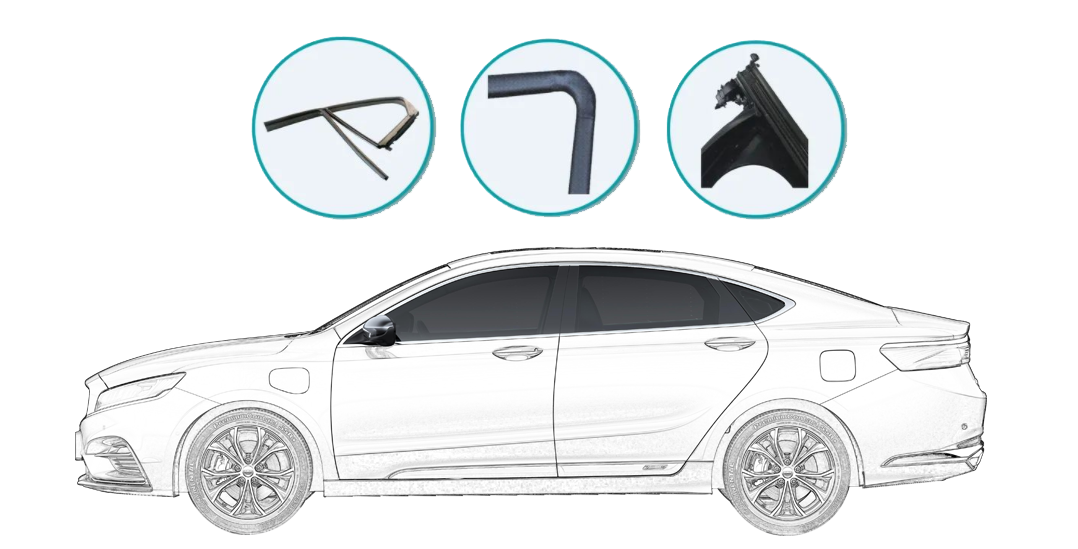
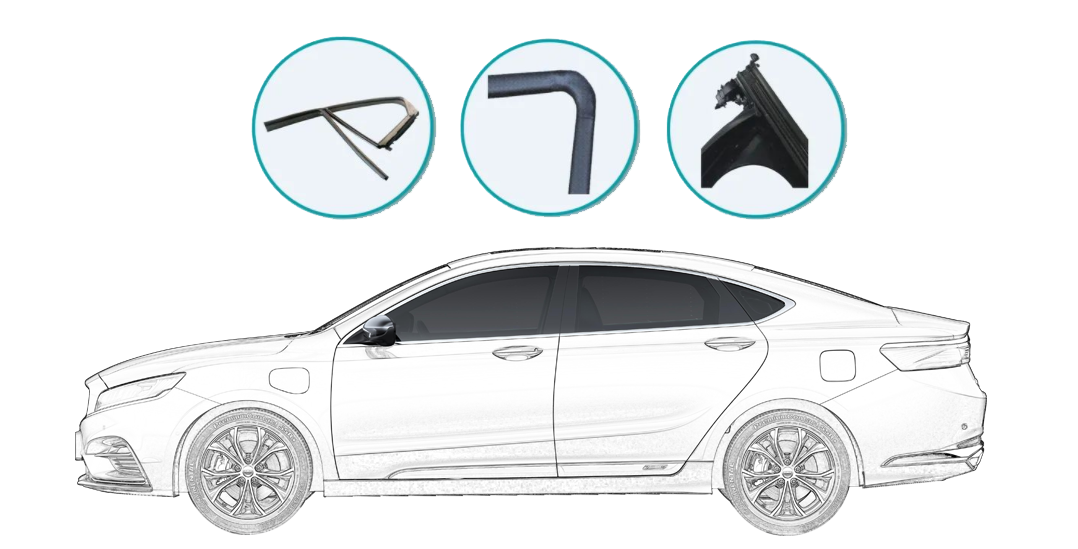
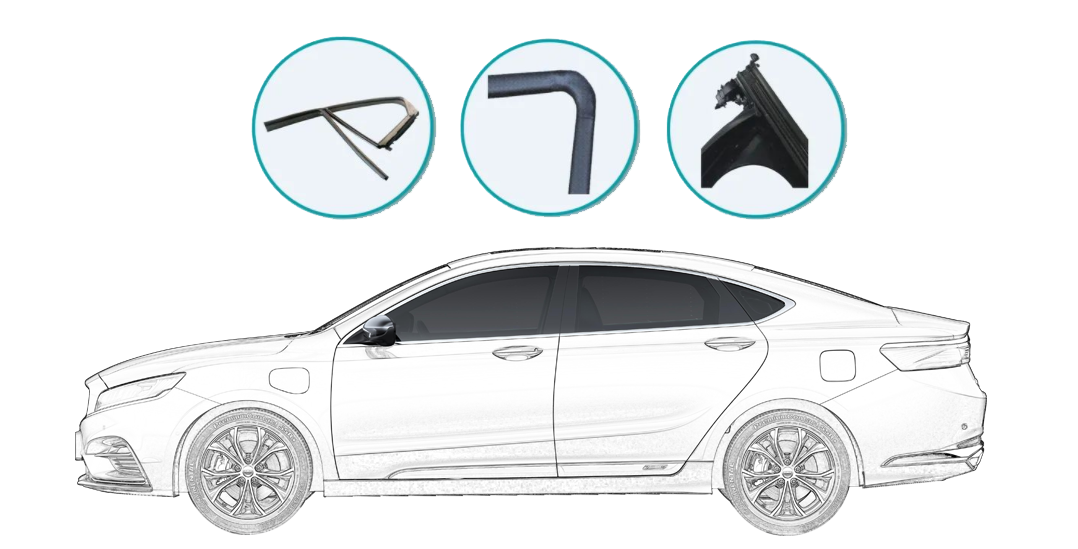
This demand is a great opportunity for DEKUMA, as it can provide customers with higher quality and precision sealing strip processing equipment to meet the increasingly high demands of the new energy vehicle industry.
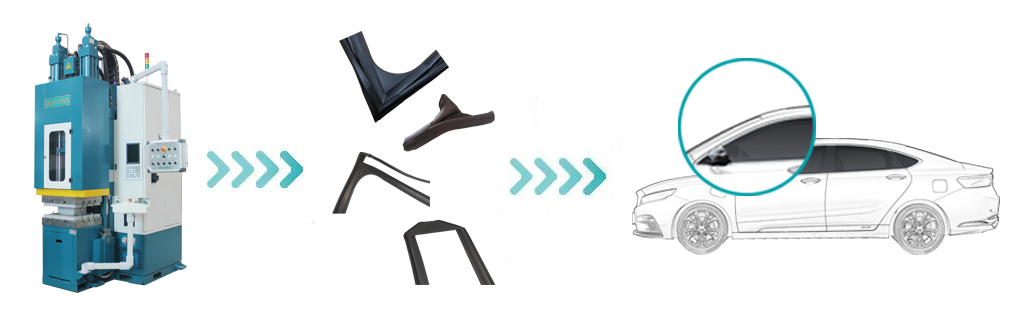
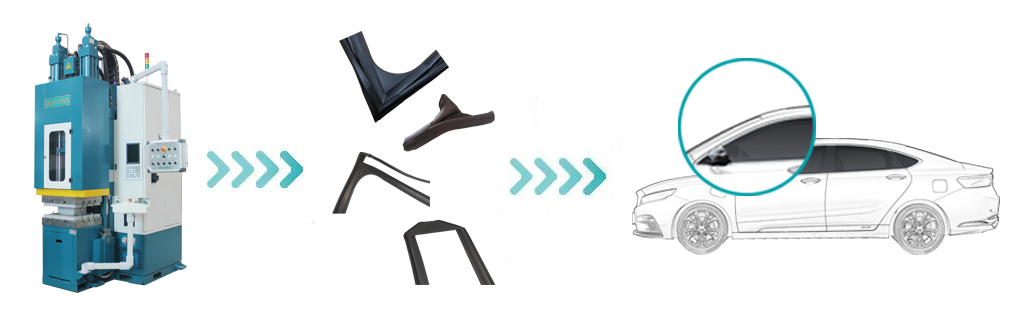
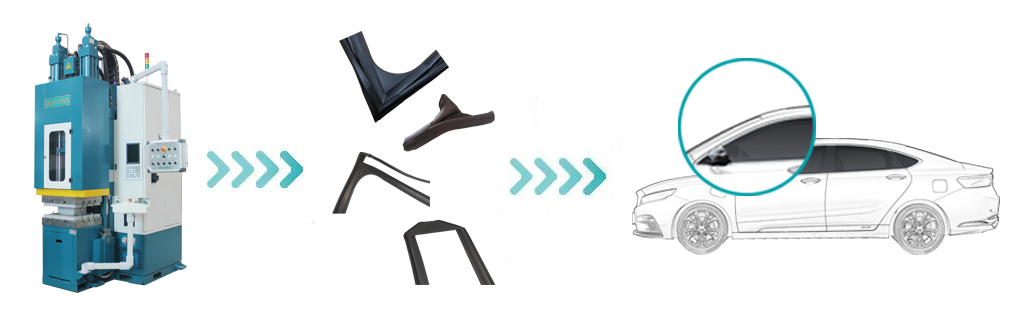
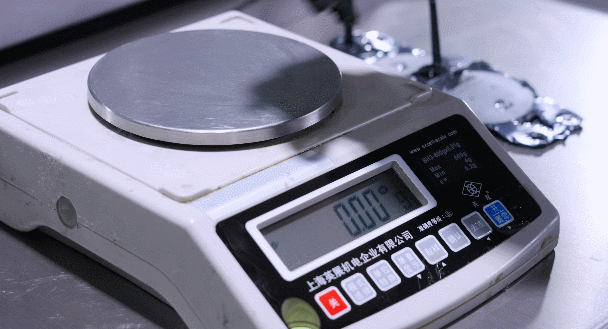
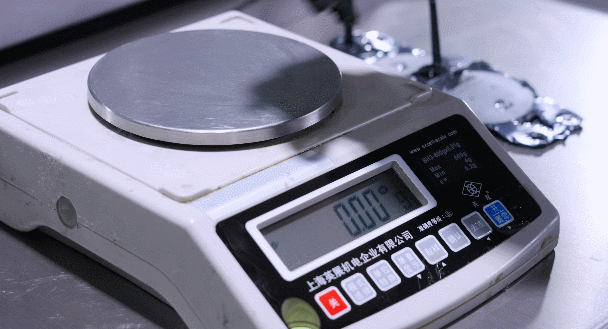
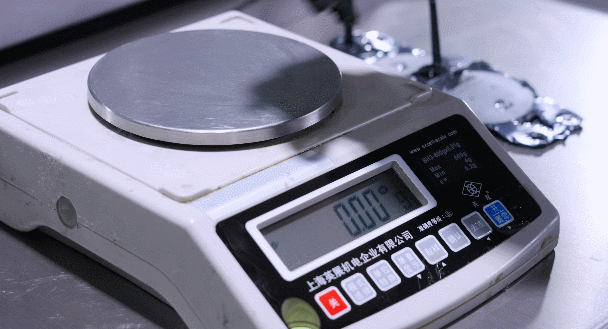
Customers require production line equipment to have the ability to operate stably in the long-term to ensure the continuity and efficiency of the production line, reduce the probability of defective products, and avoid delays caused by such issues.
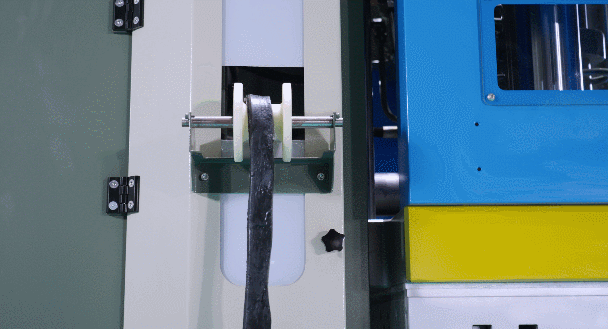
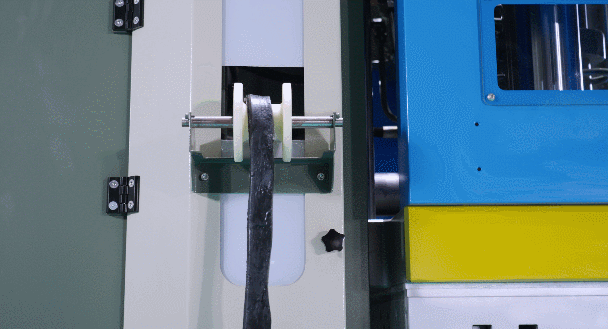
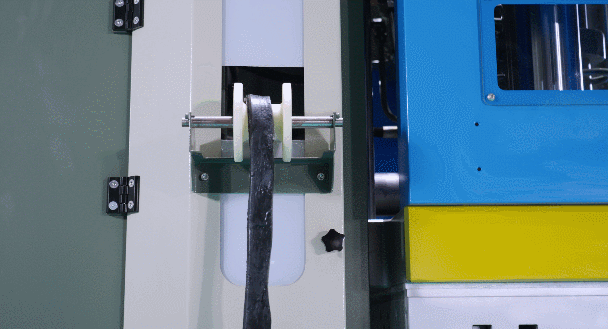
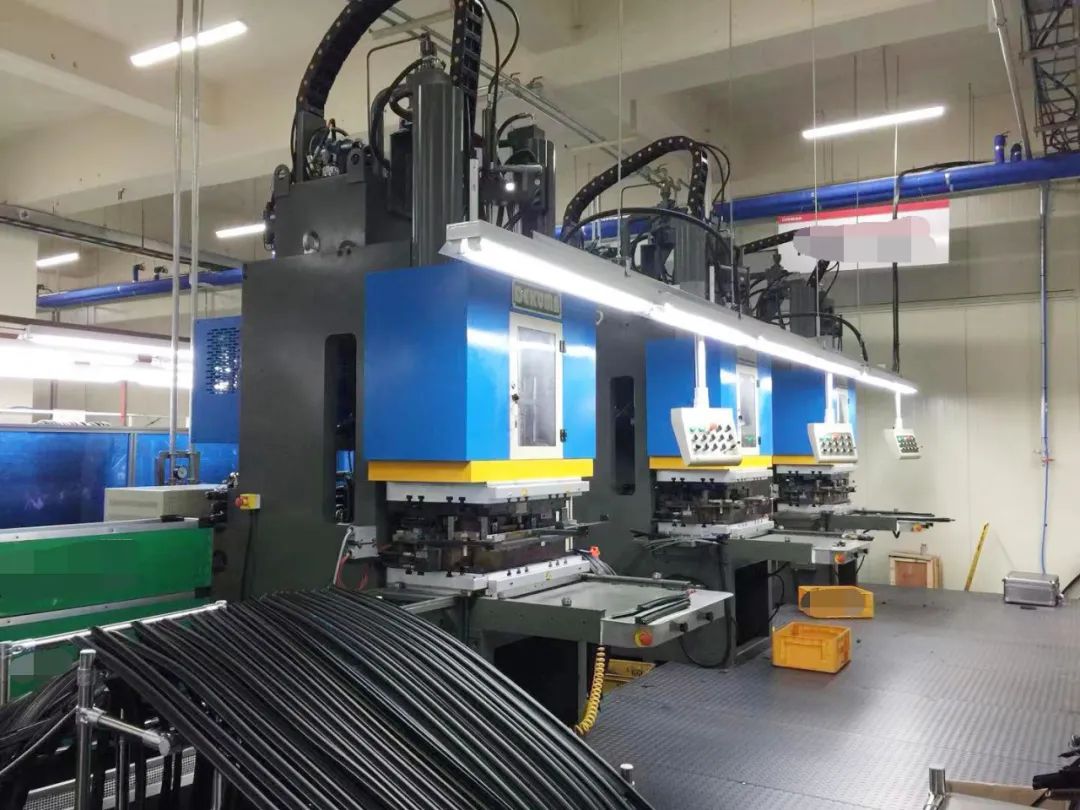
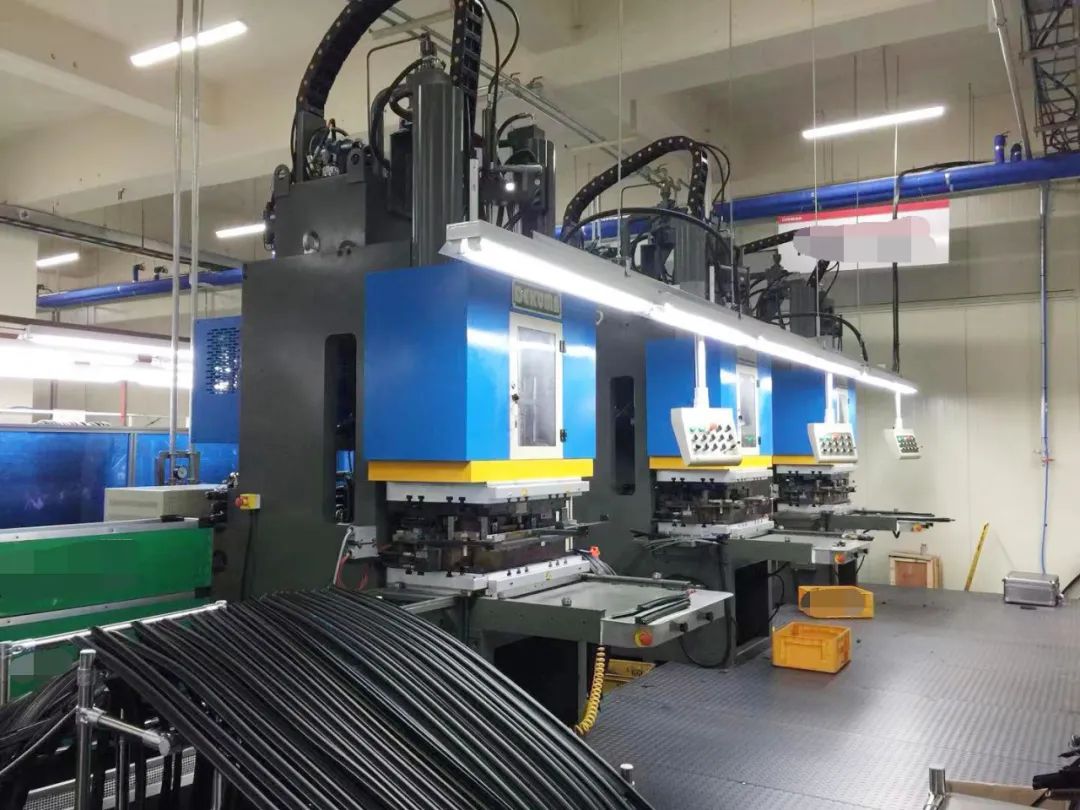
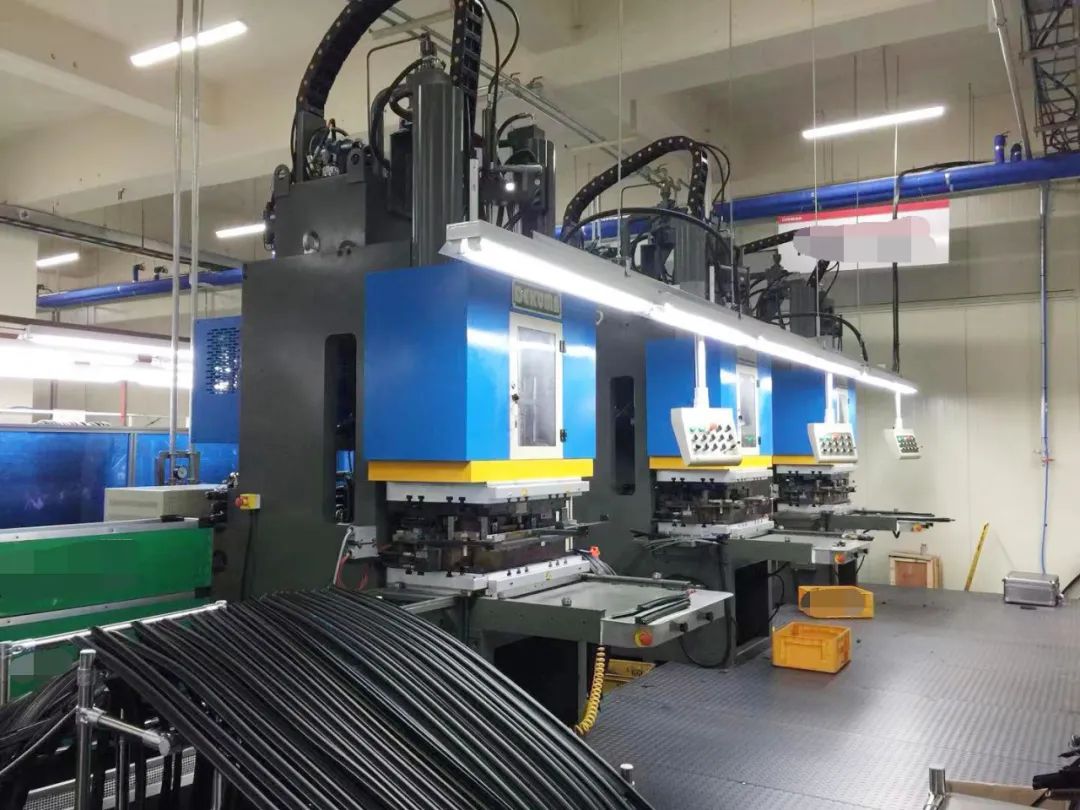
As a manufacturer of high-end rubber and plastic equipment,DEKUMA has always been paying attention to market development trends and committed to researching new technologies and materials to improve the efficiency and precision of seal processing equipment.
Dekuma Communication’s extrusion lines for microtubes and bundle tubes are pressing the “acceleration button” for the production of fiber optic networks.
Microduct is a small conduit with a diameter generally between 5-22mm that can be used as a channel for installing fiber optic cables.
Microduct bundles, are preassembled groups of microducts used for the installation of multiple fiber optic cables.
Since its launch in 2011, Dekuma’s Microduct & Microduct Bundle Extrusion Line
has been constantly iterated and upgraded, resulting in three major advantages for users:
01、Optimize the production process to increase productivity
The production speed of 14mm pipe up to 100m/min.
02、Automated configuration and efficient winding
Dual stations winder with automatic switching device can quickly change position and neatly arrange the pipe.
03、Provide a total production solution, saving time and effort
Dekuma provides customers with a turnkey solution, which can produce Microducts of all specifications and provide various production plans for Microduct Bundles.
The Microduct Bundle production line developed by Dekuma in cooperation with overseas customers provide users with a set of production solutions that are easy to operate, efficient and stable, and replace by automation instead of manual production.
We can always assist users in easily achieving a comprehensive upgrade in the production of Microduct & Microduct Bundle.
DEKUMA invites you to visit CHINAPLAS 2023
This exhibition will be held from April 17 to 20 at the Shenzhen World Exhibition & Convention Center for 4 days.
There is only one month left before the opening of the Chinaplas 2023. Dekuma, as a leader of high-end rubber and plastic machinery industry in China, always pays attention to the key points of customers and provides better solutions for customers with continuous improvement of technology and service.
In this issue, we will introduce RA650 composite insulator rubber machine, PE450 chipless cutting machine, RV50 automatic skeleton oil seal rubber machine in detail.
01、RA650 Composite Insulator Rubber Injection Machine
Dekuma will launch a new design of low table composite insulator rubber machine in 2023. This equipment solves the industry problem of difficult installation and operation of large-scale composite insulator rubber machine.
02、PE450 Pipe Cutting Machine
Dekuma will launch a new design of PE450 chipless cutting machine. This equipment adopts a unique knife feeding device and pipe adding device to solve the industry problem of uneven cutting surface and white edge of large-diameter pipes, reaching the industry-leading level.
03、RV50 Automobile Skeleton Oil Seal Rubber Injection Machine
Dekuma’s newly launched RV50 rubber injection machine production line combines Dekuma’s high-performance rubber machine and self-developed automation solution to reduce labor demand and solve the problem of difficult recruitment for end users.
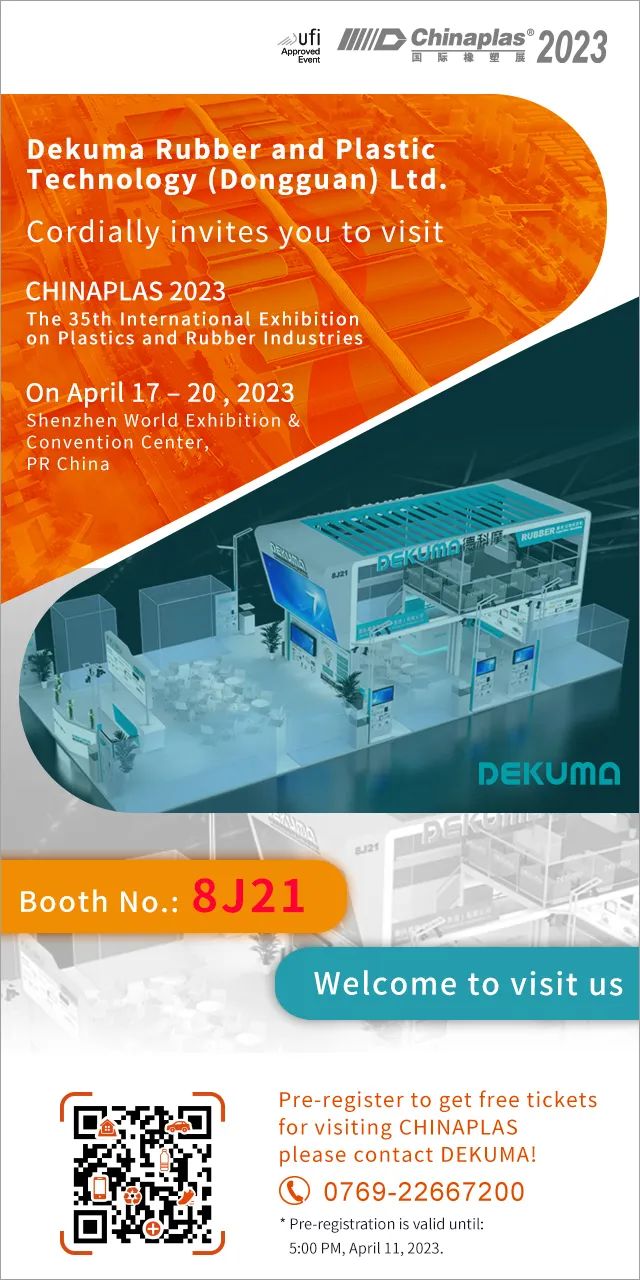
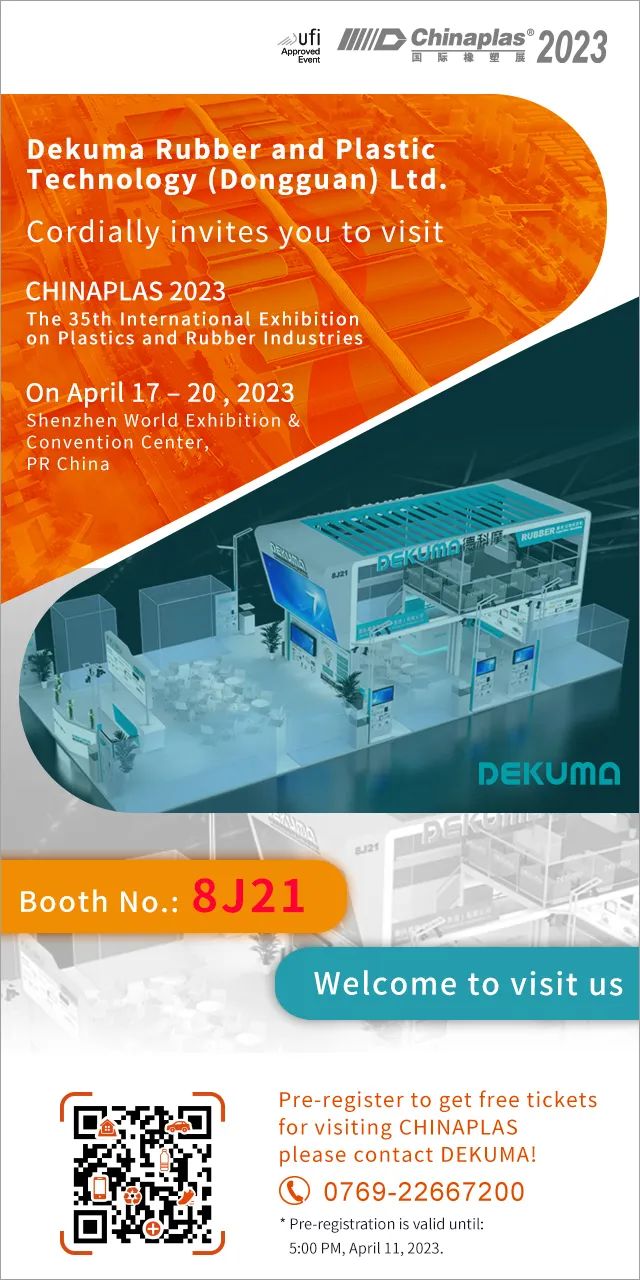
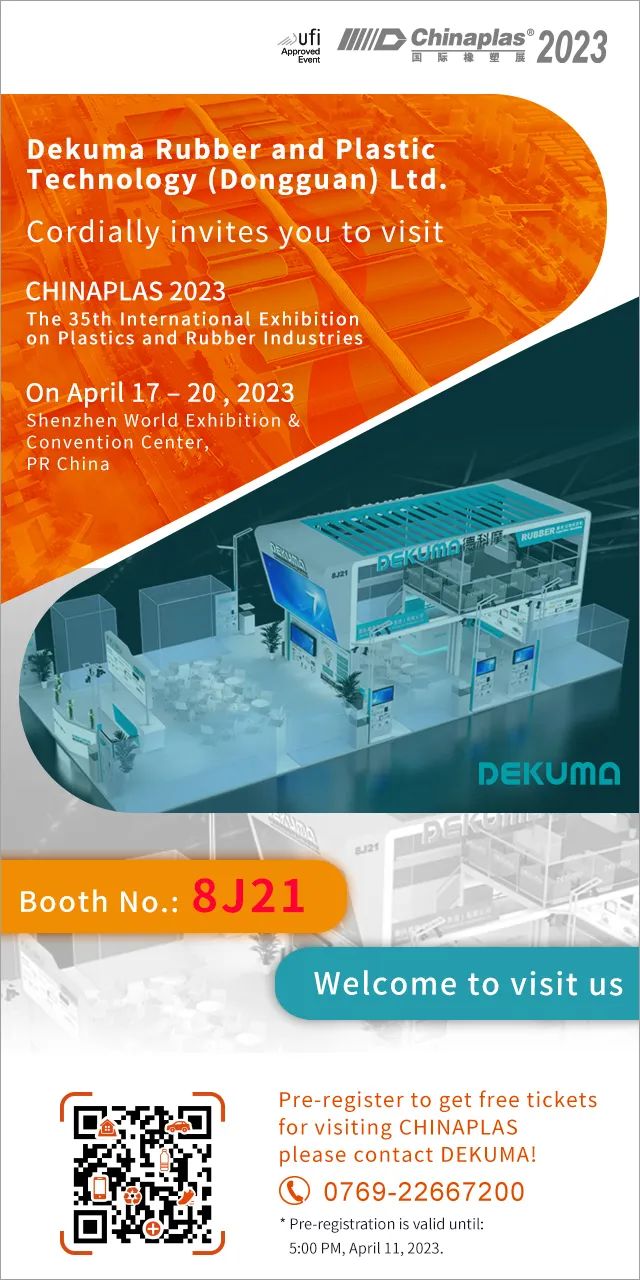
Highlights Review | Dekuma in Middle East Electricity (MEE) 2023


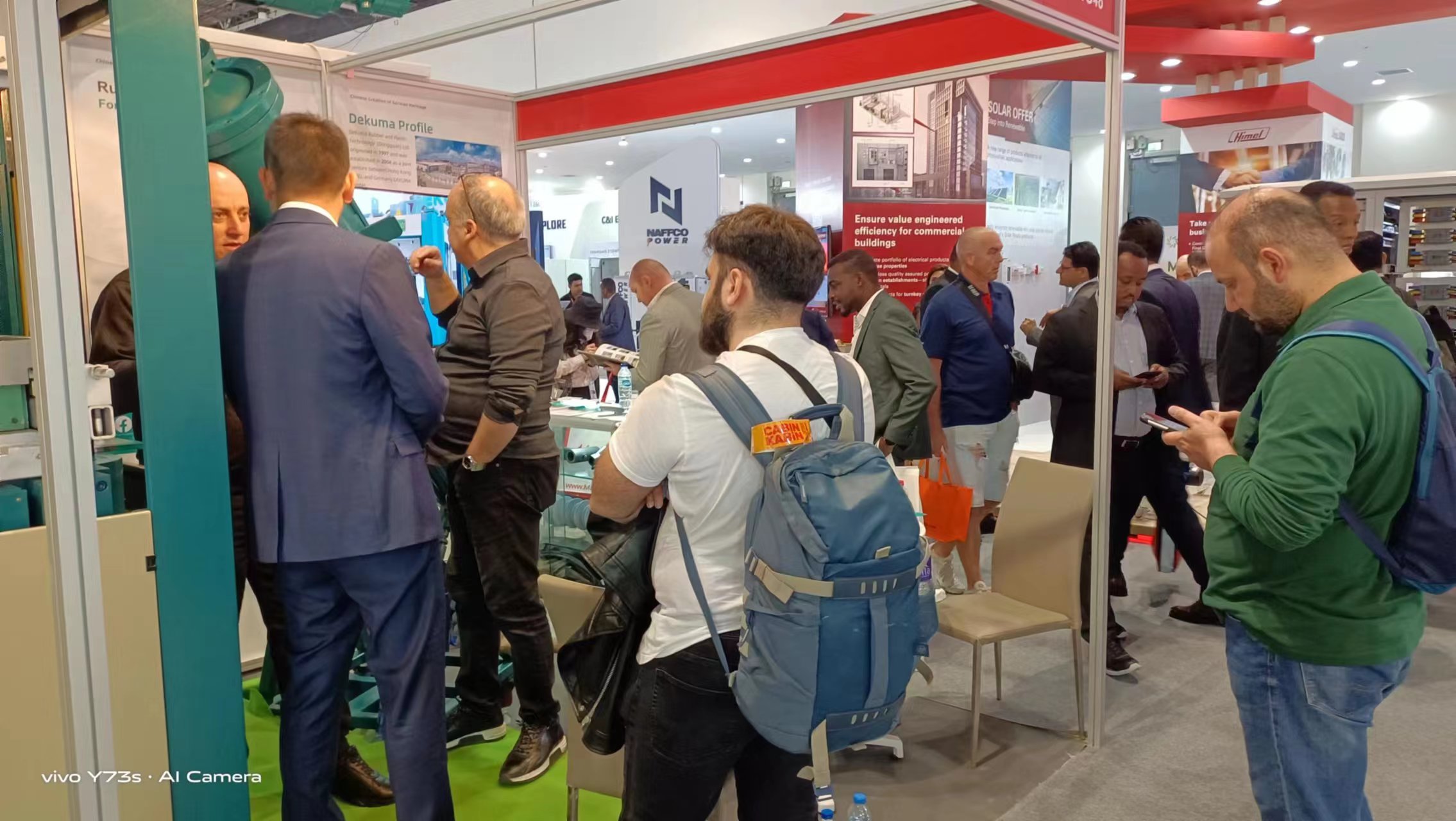
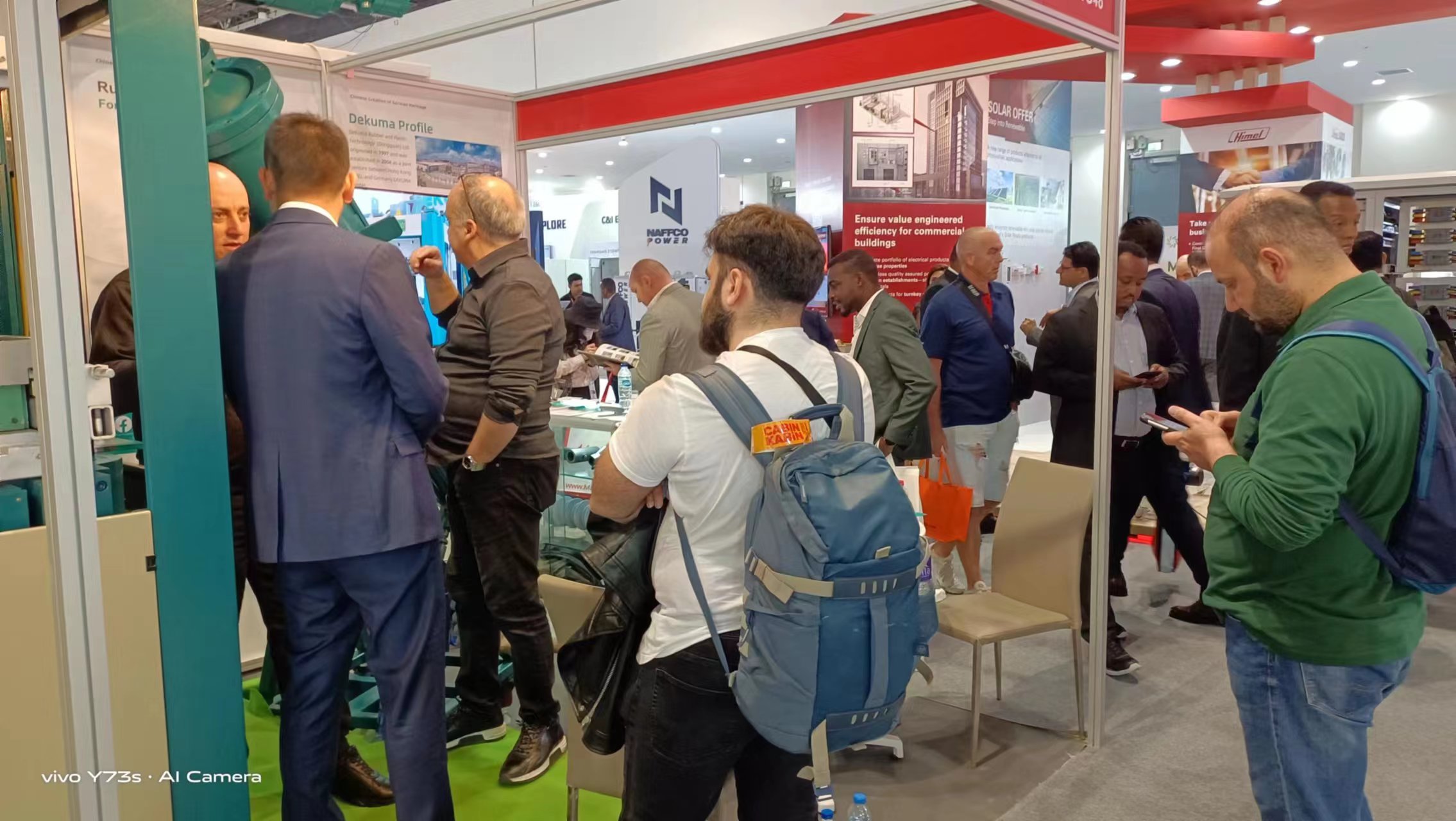
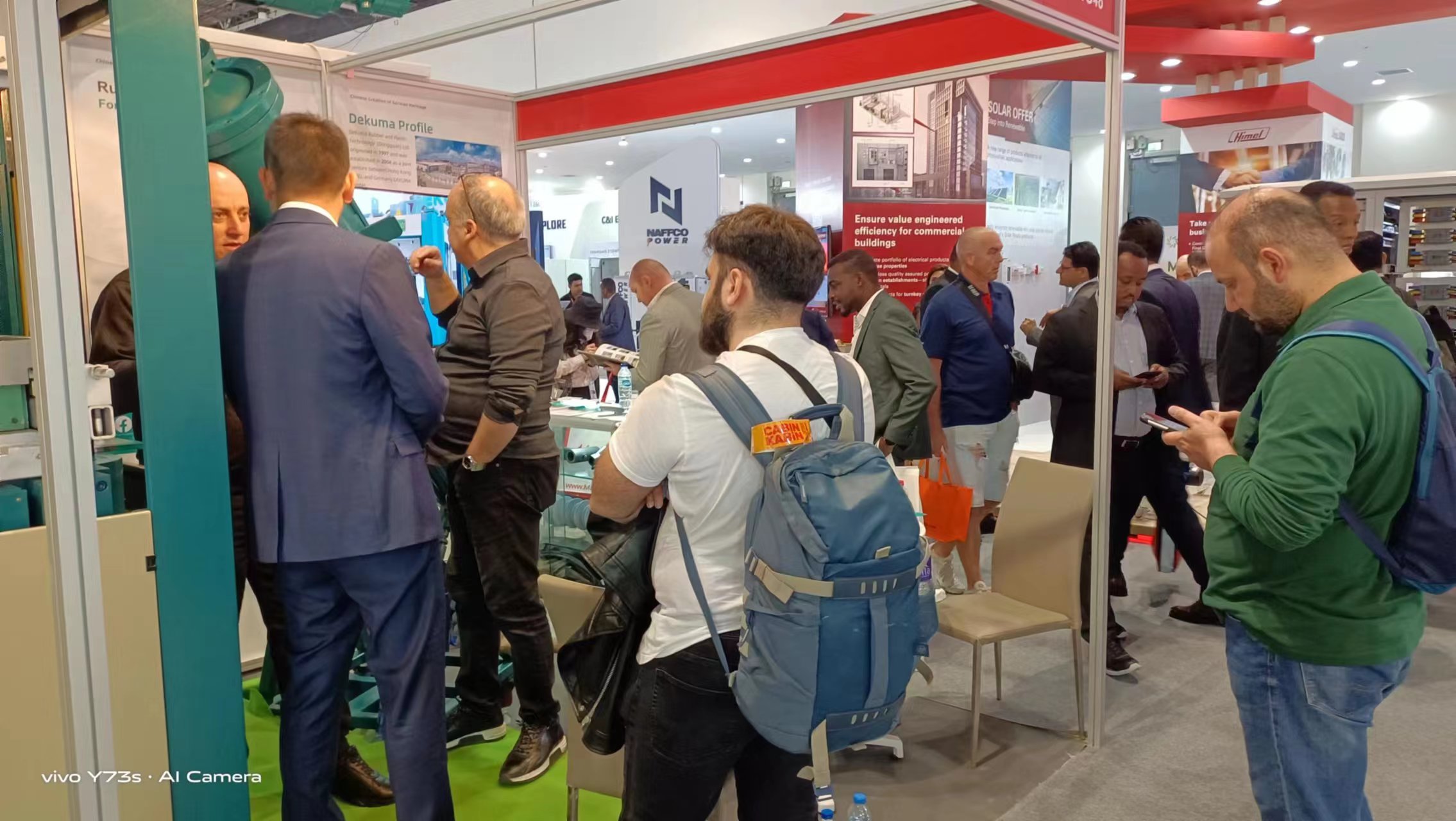
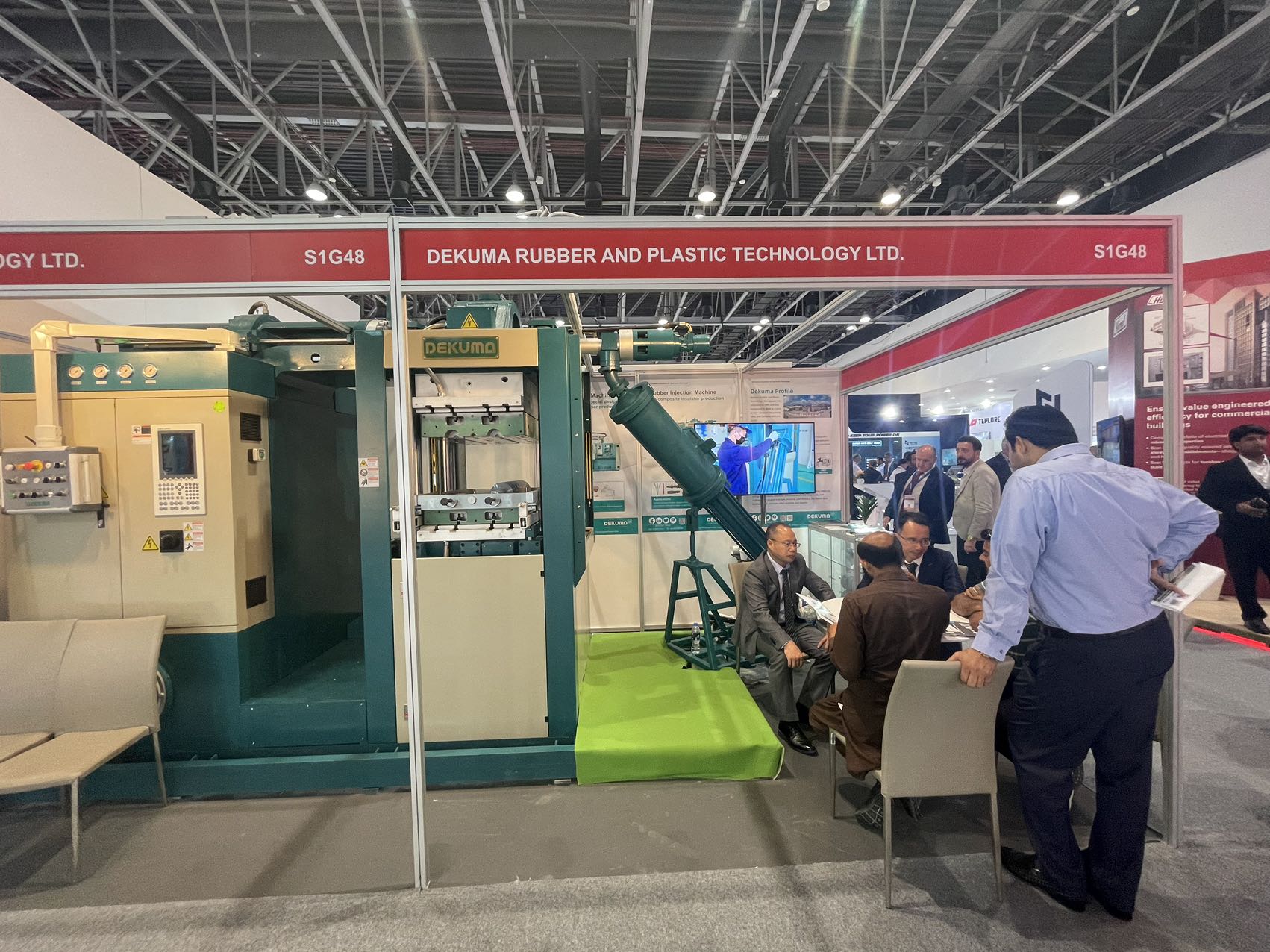
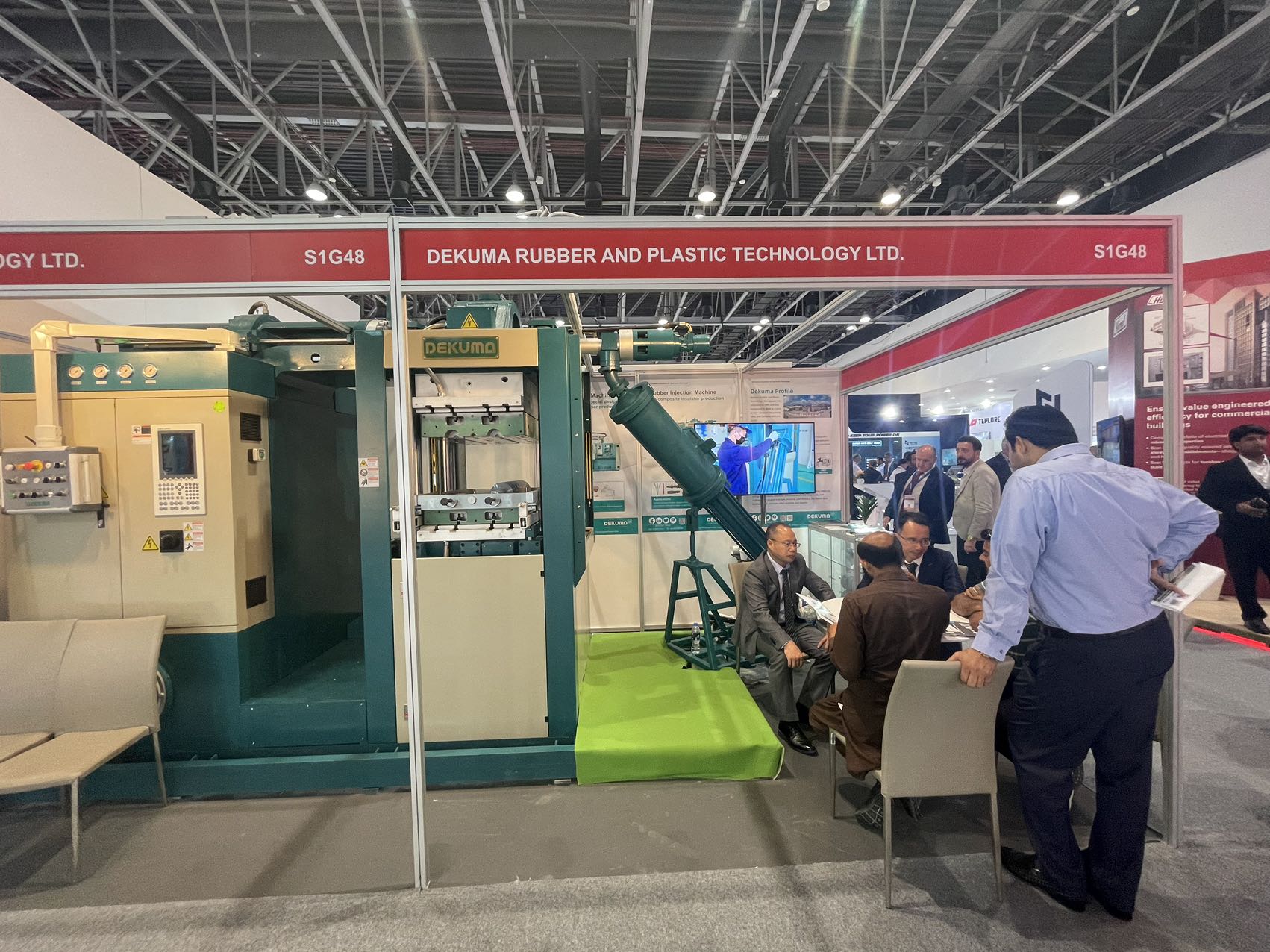
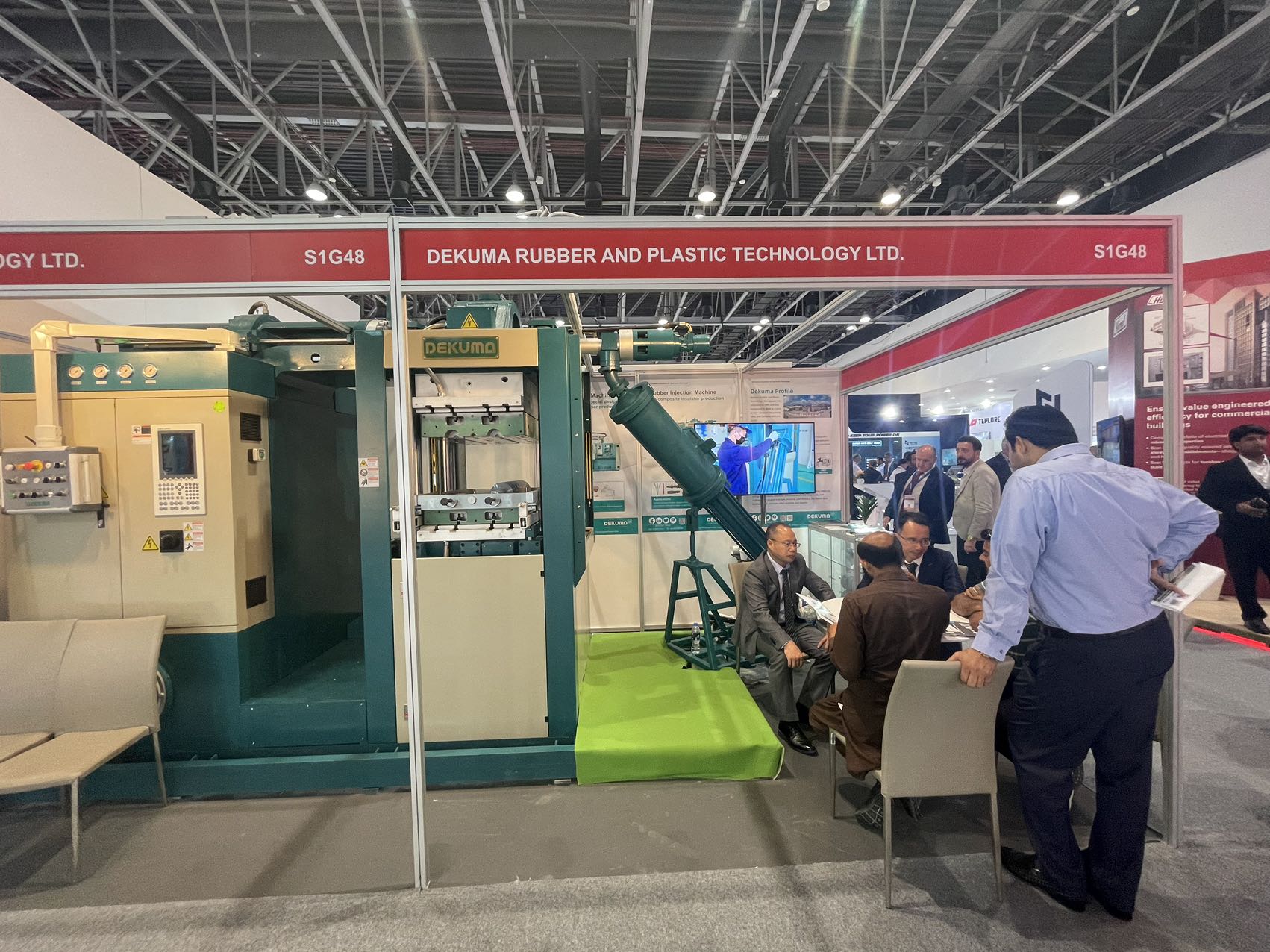



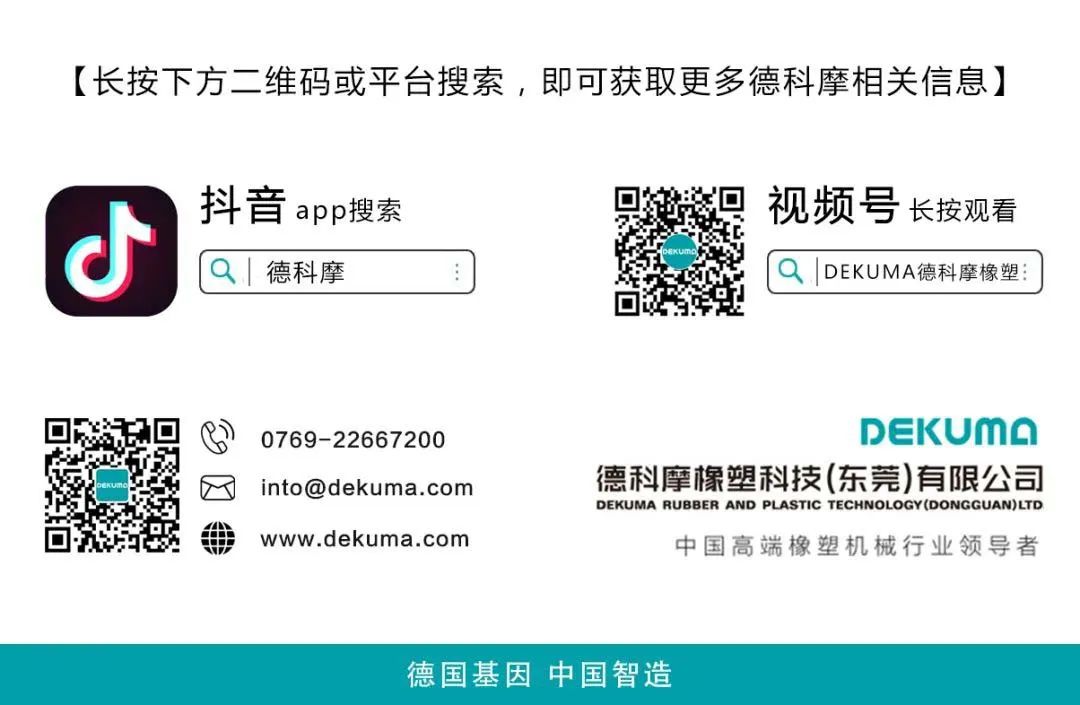
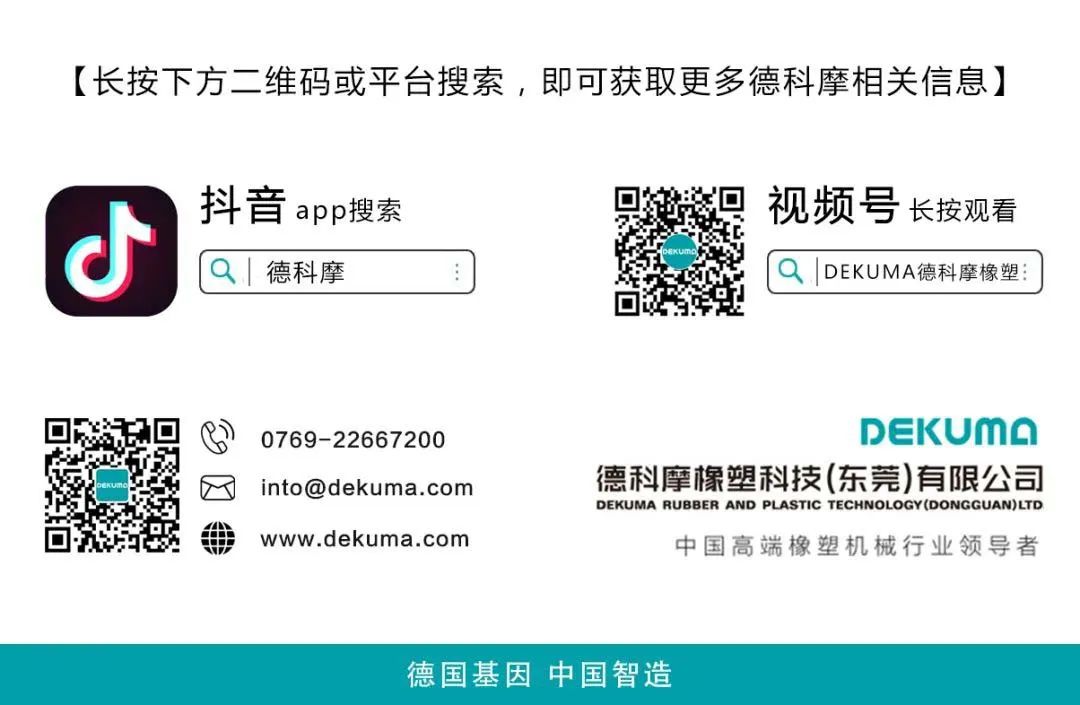
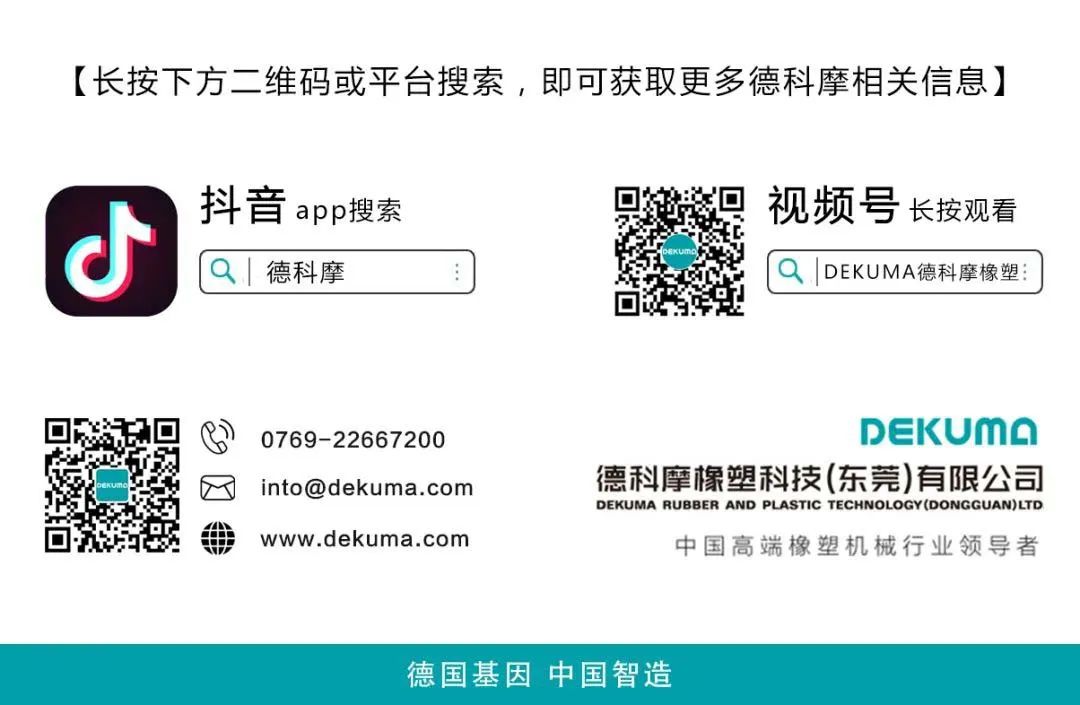
Exhibition News | Dekuma will debut at CHINAPLAS 2023



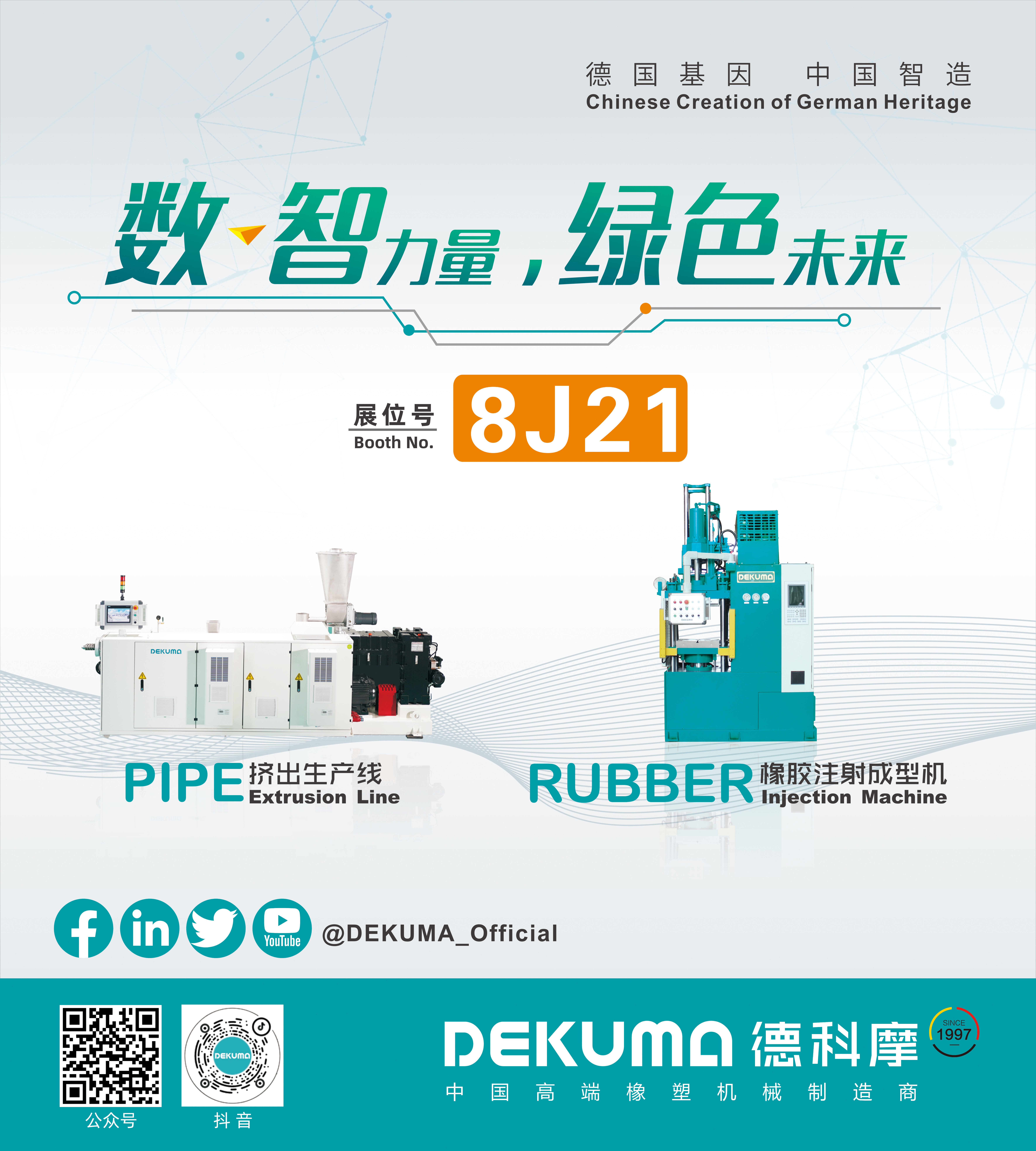
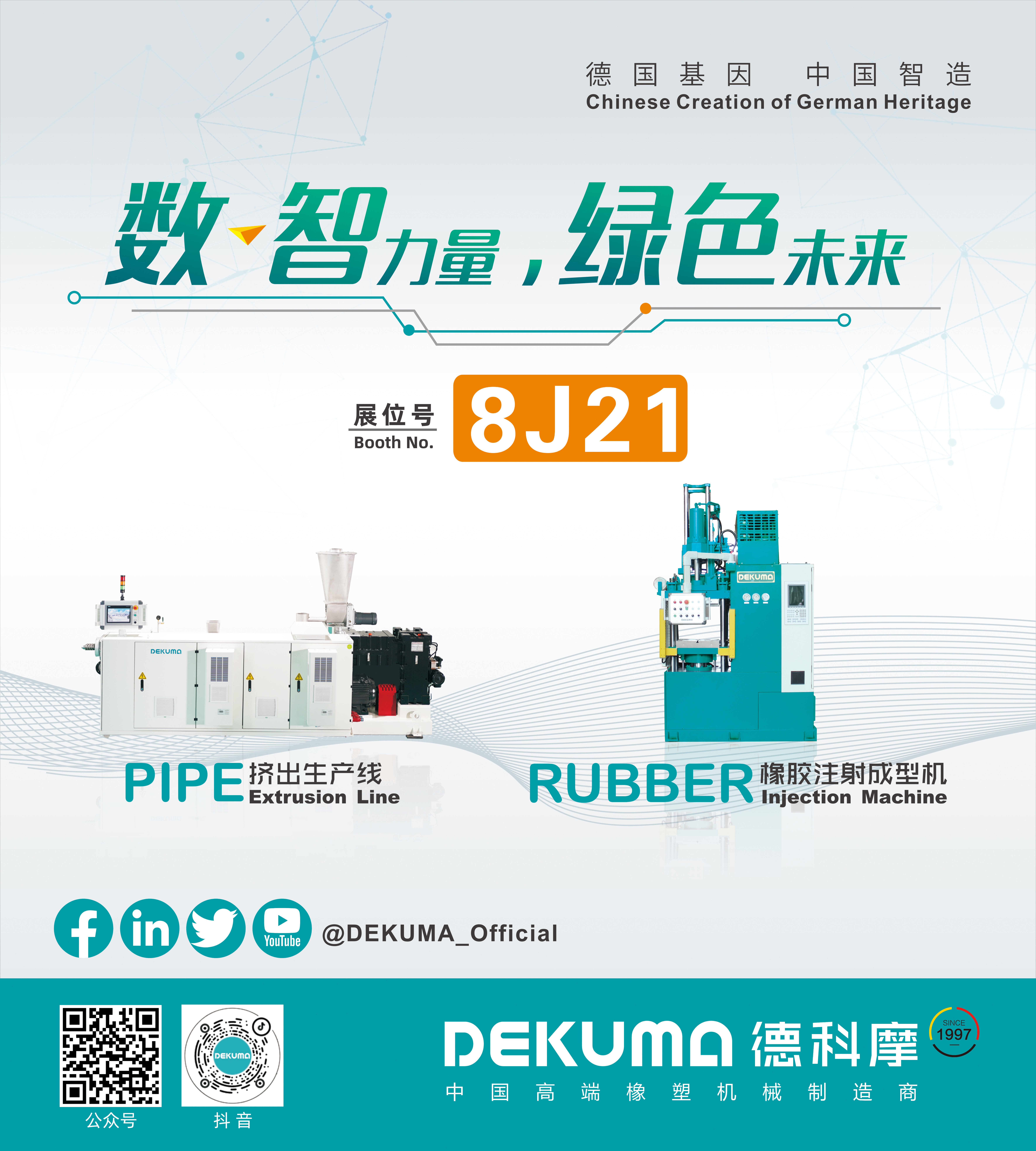
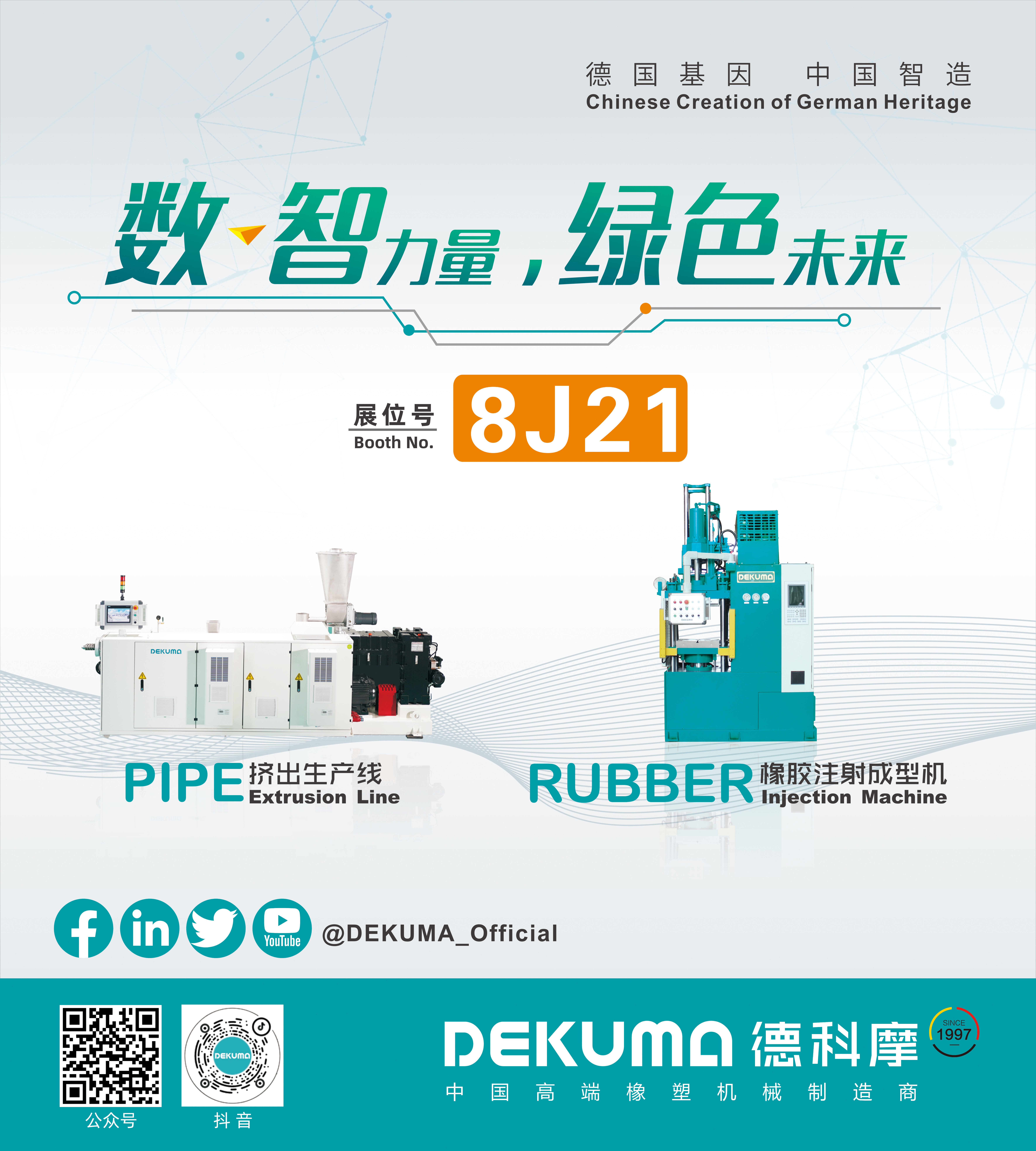
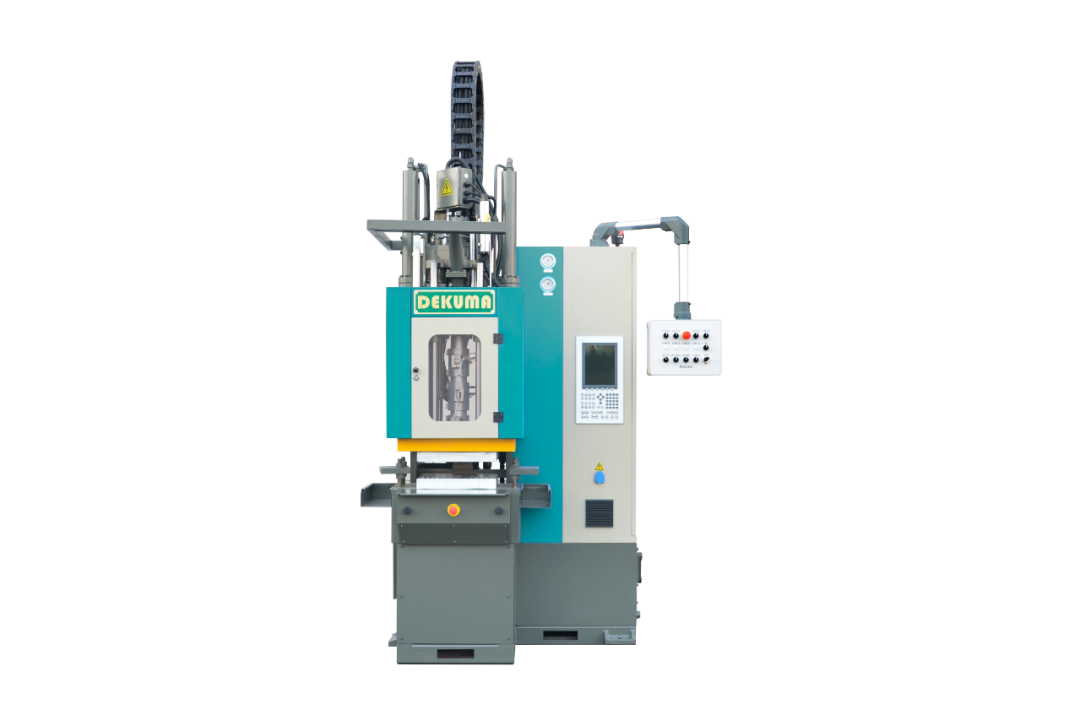
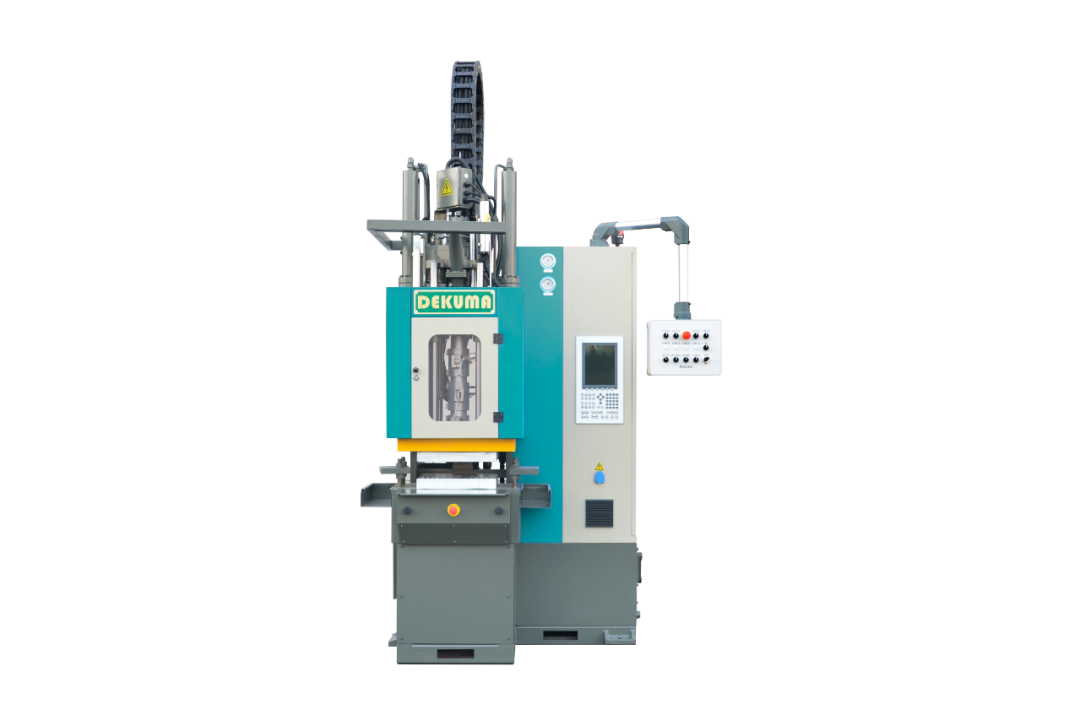
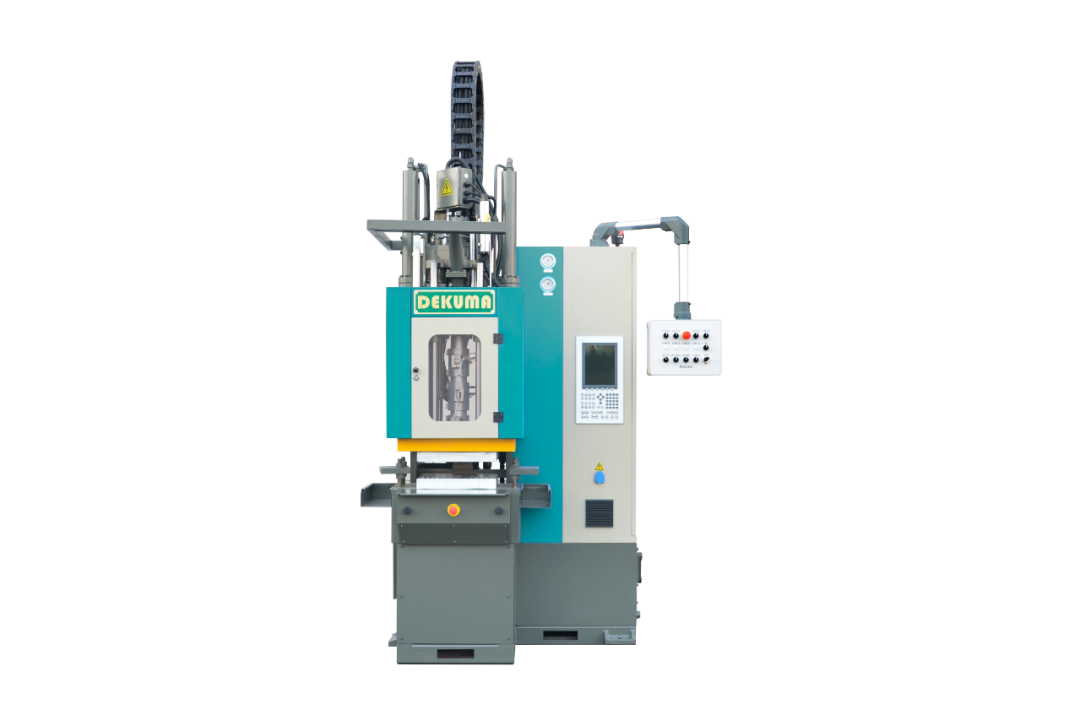
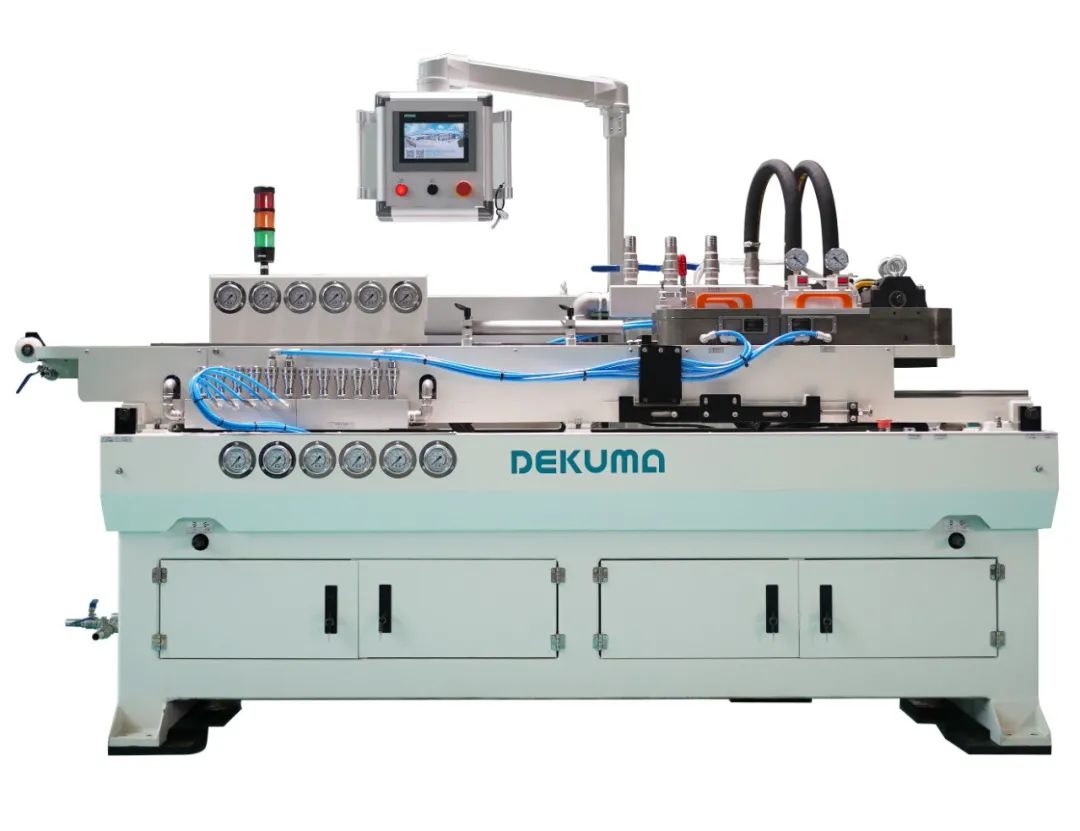
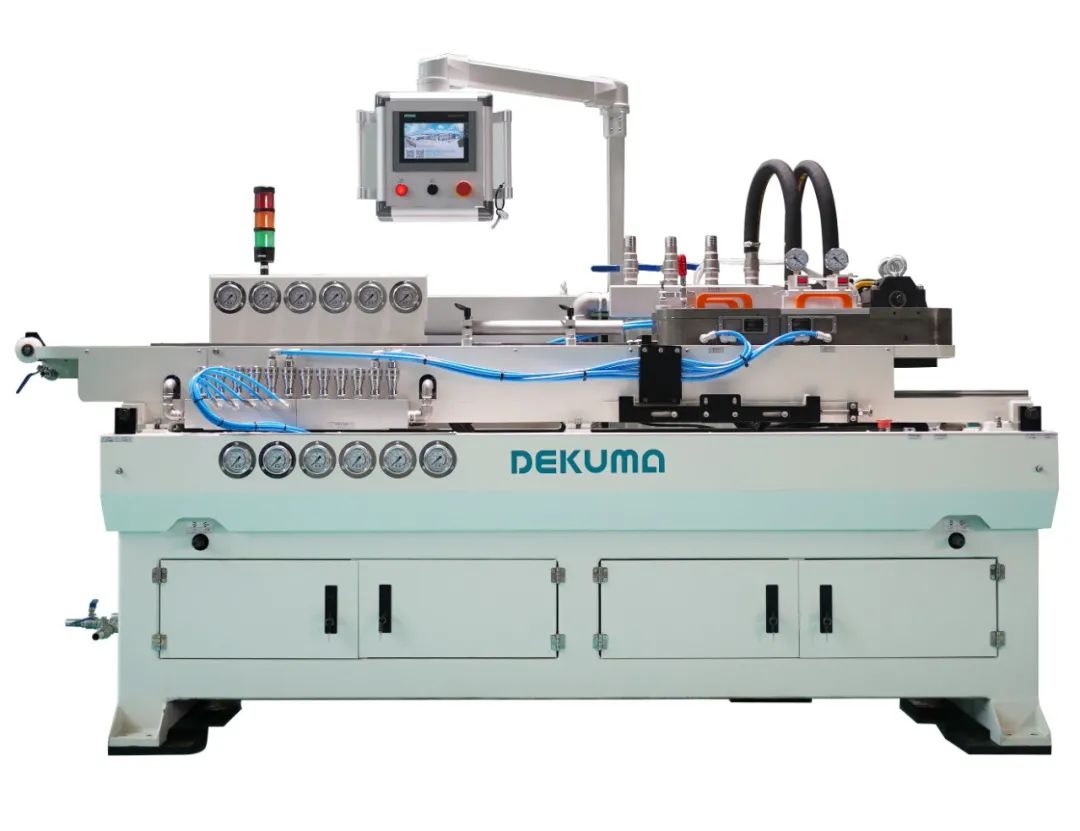
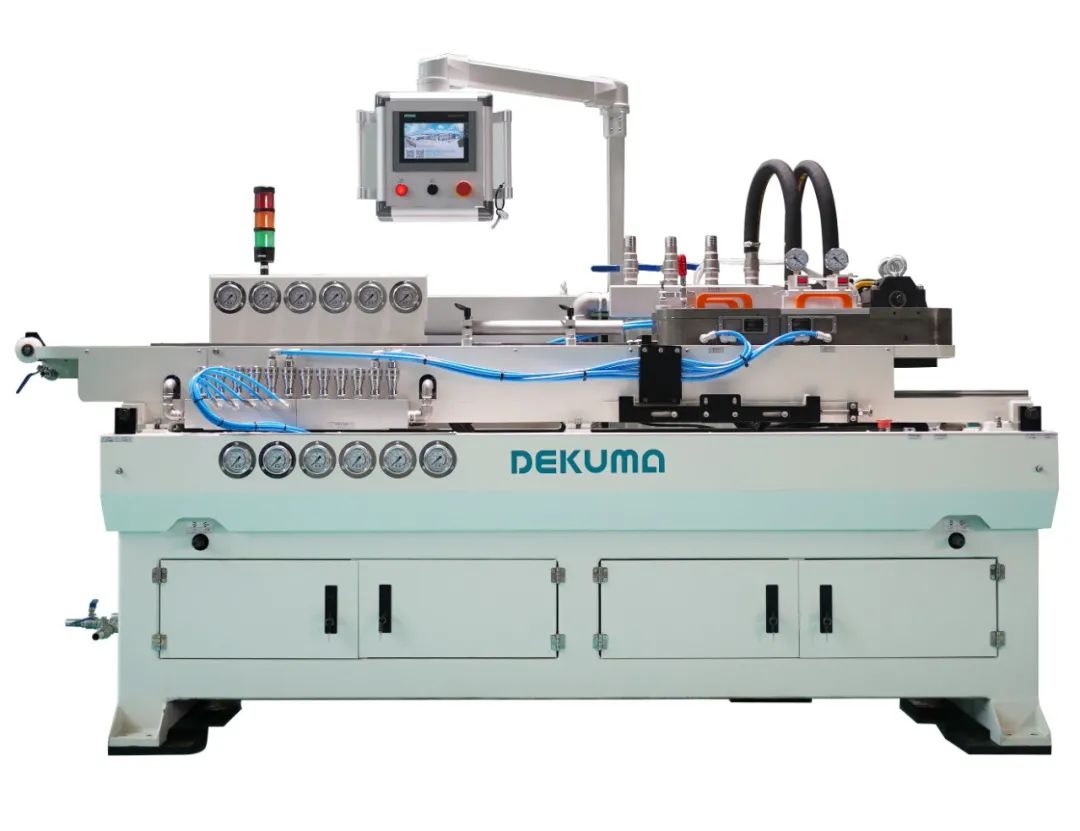
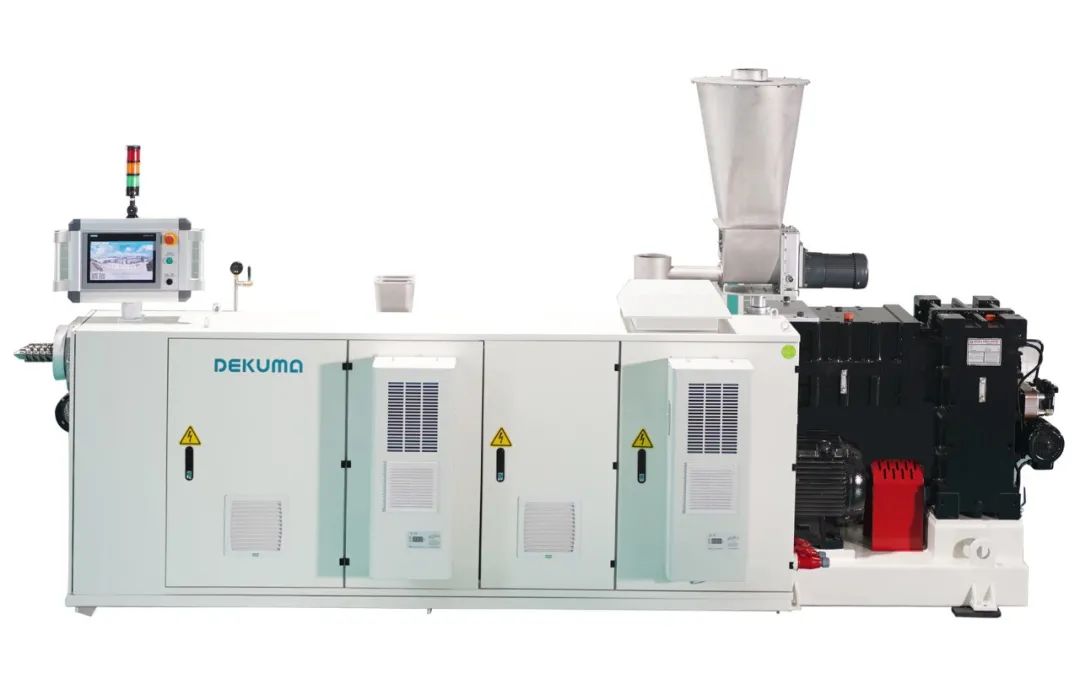
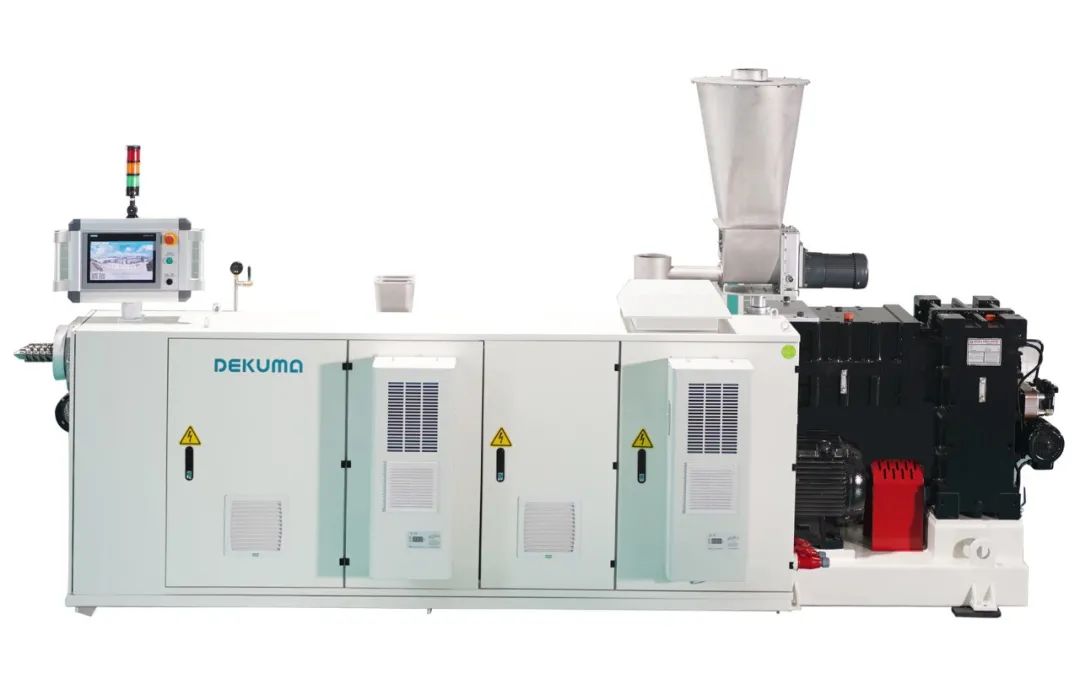
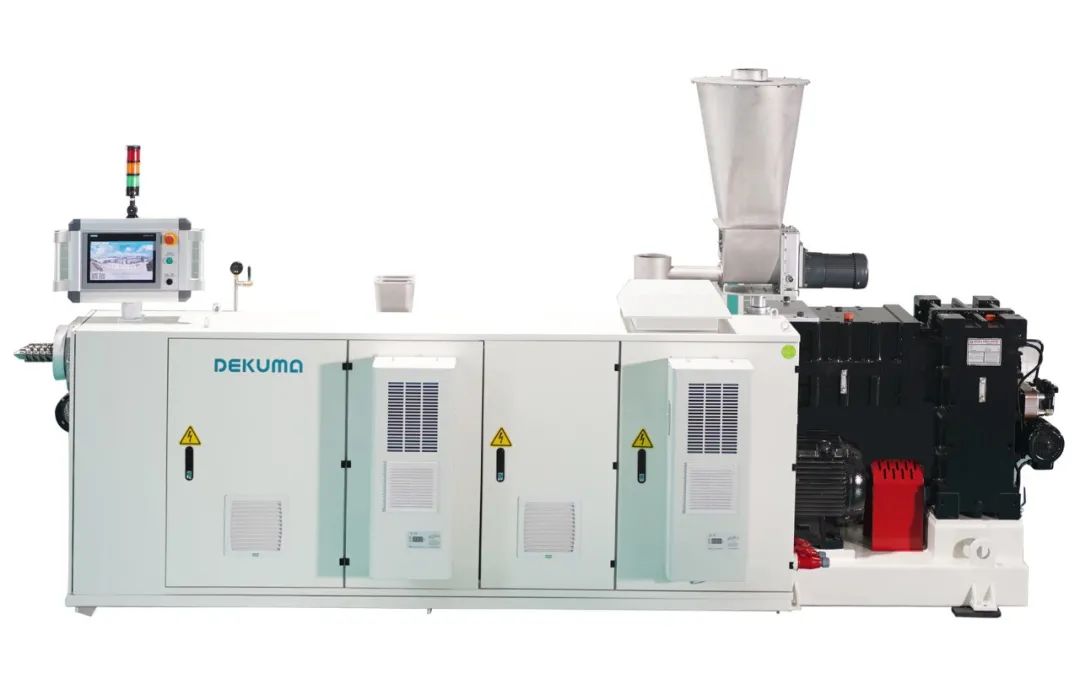
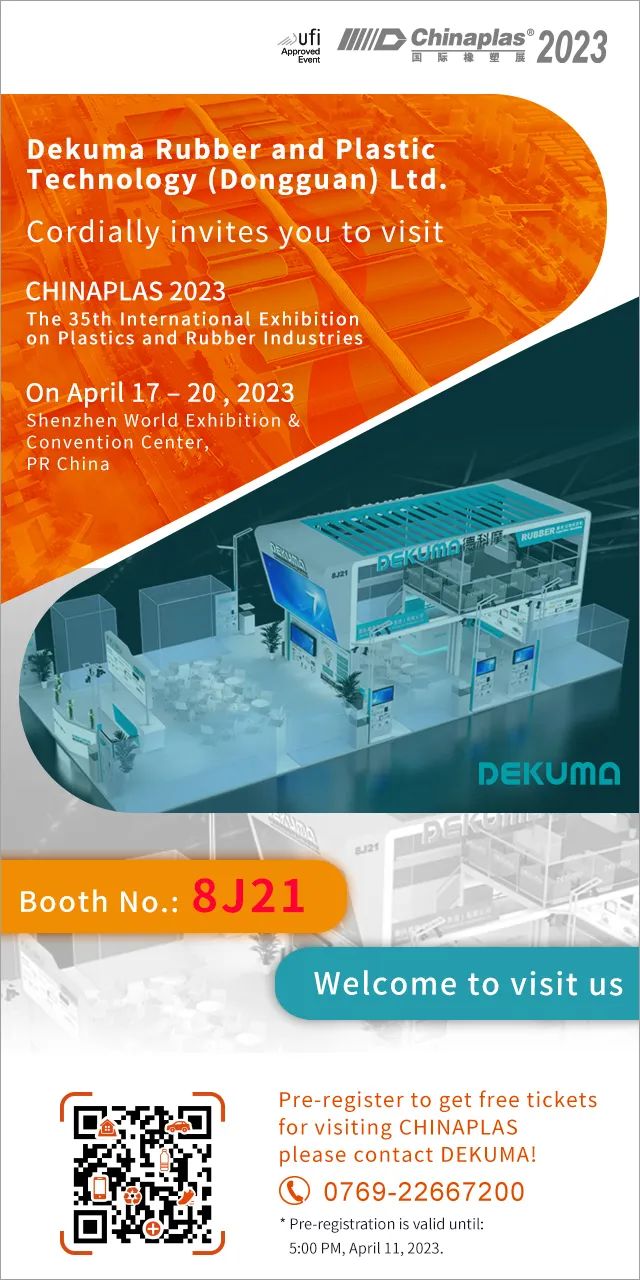
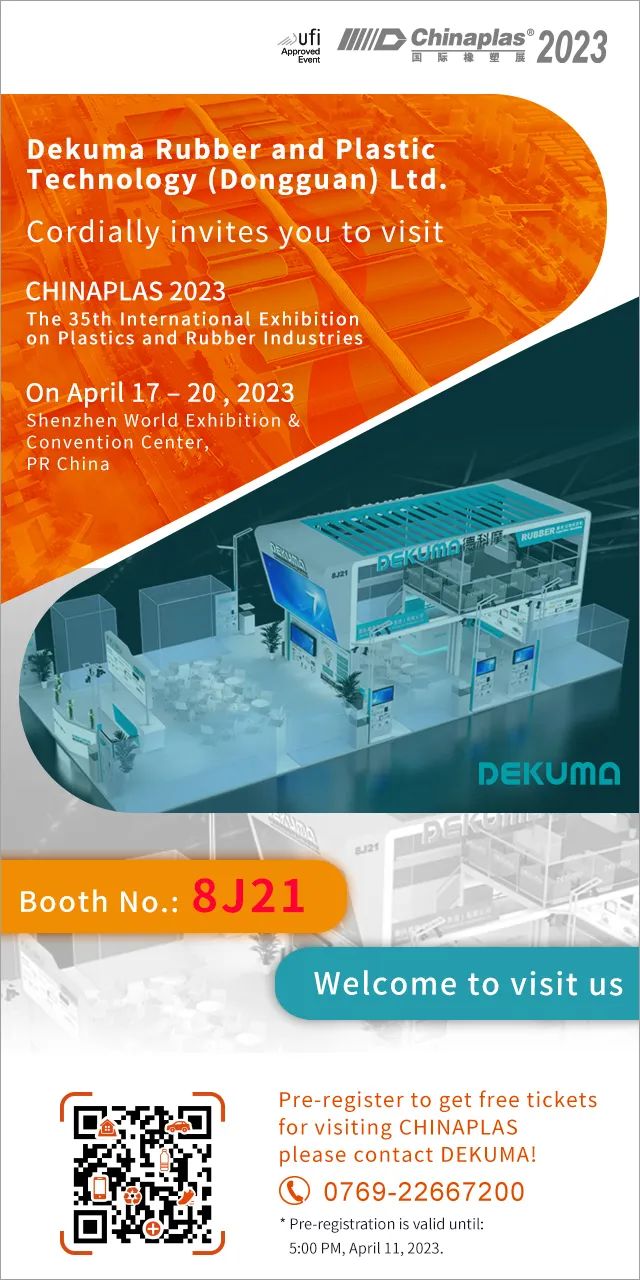
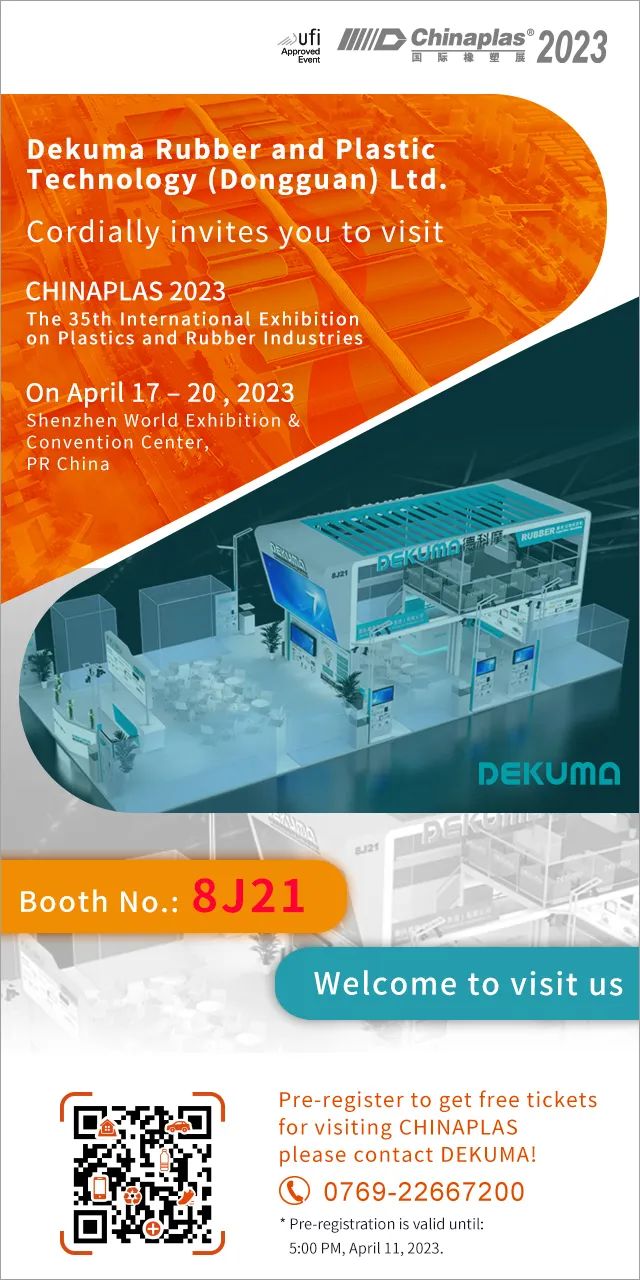
DKM-RV200F Rubber Injection Machine: A powerful tool for cable accessory production
DKM-RV200F Rubber Machine is widely used in the electric power industry, especially in the production of various types of EPDM and silicone rubber cable accessories, such as elbow joints, T-joints, insulating caps, and cable terminal joints.
This equipment has the following features:
1、Flexible structure for easy mold installation
Adopts a direct pressure locking mold structure to facilitate the installation of molds with different thicknesses. In addition, the stepless pull rod structure also ensures sufficient space for mold locking.
2、Safe device to improve production efficiency
The locking mold cylinder comes with a safety pressure protection device to prevent overloading of the locking mold pressure.
3、Anti-loosening structure to extend service life
The pull rod anti-loosening structure ensures that the threads on both ends of the pull rod are secure, evenly stressed, and not easily damaged.
4、Intelligent system for easy operation
Adopts the most advanced control system in Europe to meet the requirements of various molds and product processes.
DKM has always been committed to meeting the needs of users, constantly innovating, and improving product and service quality to provide users with comprehensive solutions.
We believe that the DKM-RV200F Rubber Machine will help users achieve a dual reduction in production costs and management costs, and create more business opportunities and competitive advantages for users.
2000T High-Precision Frame Type Servo Driven Hydraulic Press
This product is mainly used for metallic materials such as shallow drawing, press forming and stamping process.
It is suitable for the forming of high-precision parts such as automotive cover parts, interior parts, sealing pads, new energy vehicle battery pack water-cooled plates, computer and server casings, household appliance casings, TV back panels, and plate-type radiators.
1: Newly upgraded with a large table design
3 x 2 meter large bolster, optimized for the pressing of new energy vehicle battery pack water-cooled plates.
2:High precision pressing for improved pressed products pass rate
Ram cylinder slow pressing position repeatability ≤±0.02mm, ram cylinder slow pressing pressure accuracy ≤±1.5bar.
3:Super-strong frame structure designed for reliability and durability
Box type frame structure designed through annealing process, confirm the elastic deformation in maximum pressure through finite element analysis, guiding of moving bolster by eight-face linear guide way, enhance the stability of moving bolster movement and high eccentric pressing force.
4:Fast and flexible to improve production speed
Servo motor drive + two-way cartridge valve control, fast response speed hydraulic system, sensitive action, and reliable operation.
5:Advanced operating system for easy operation
Equipped with a Siemens PLC control system with HMI interface, large touch screen for ease operation.
6:Energy-saving to reduce production costs
Uses a servo motor drive, energy consumption reduced by 30%~50% compare with induction motor.
Drawing on 40 years of hydraulic ingenuity and craftsmanship, Cosmos Press has developed a high-precision frame servo hydraulic press that is a powerful tool for manufacturing precision parts.
Precision Extrusion | Dekuma Auto 5-layer Pipe Production Line
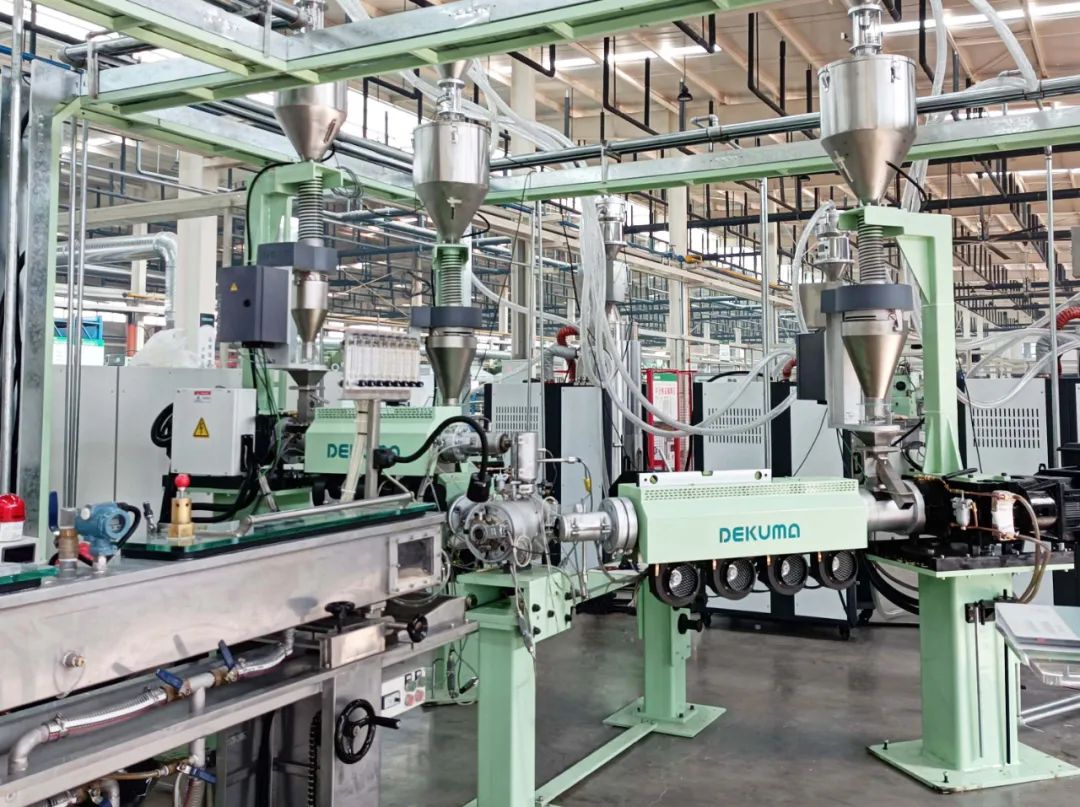
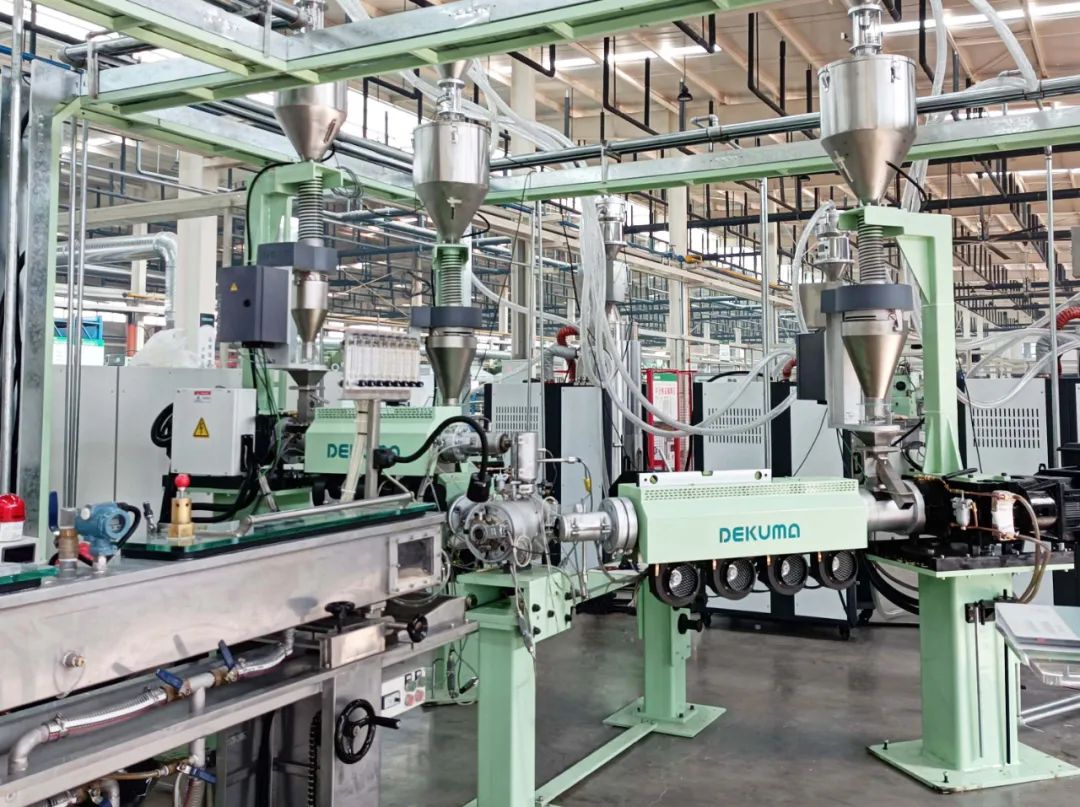
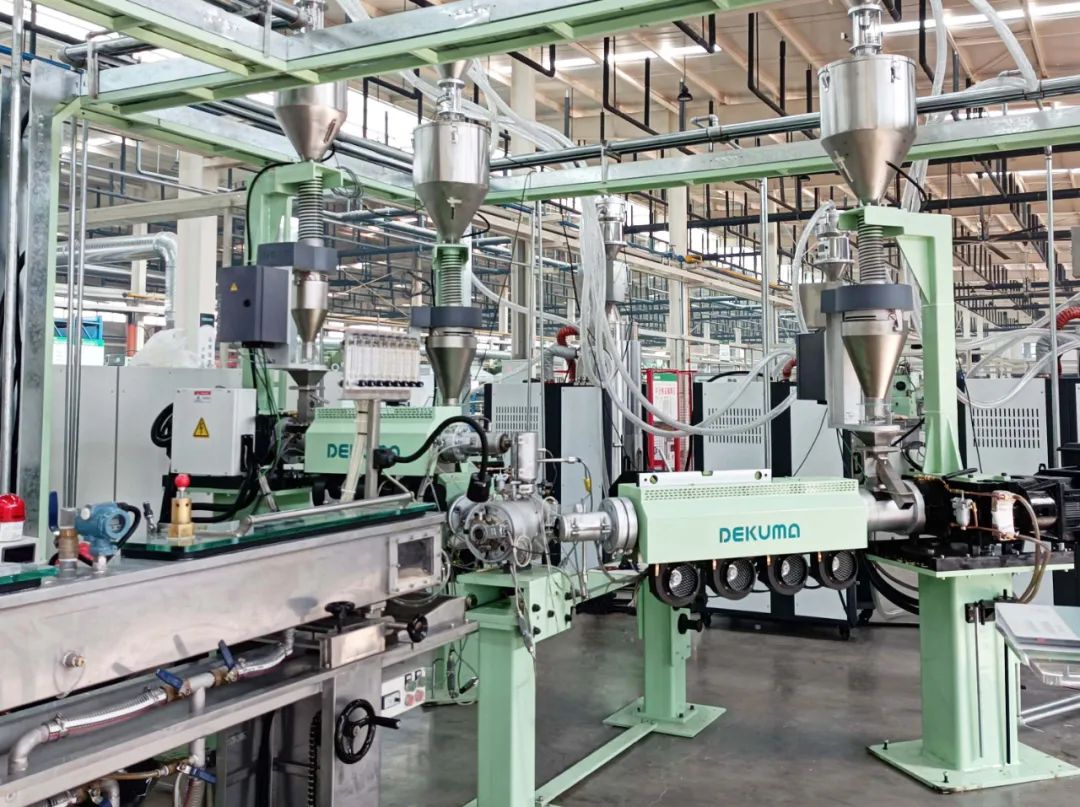
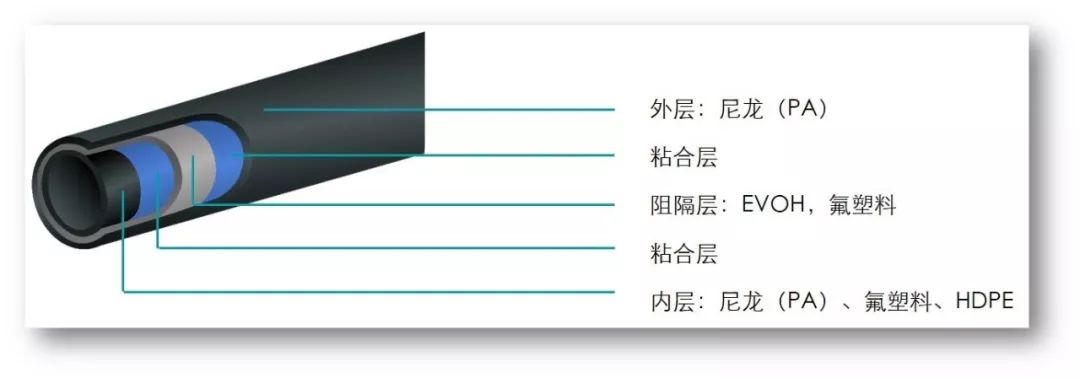
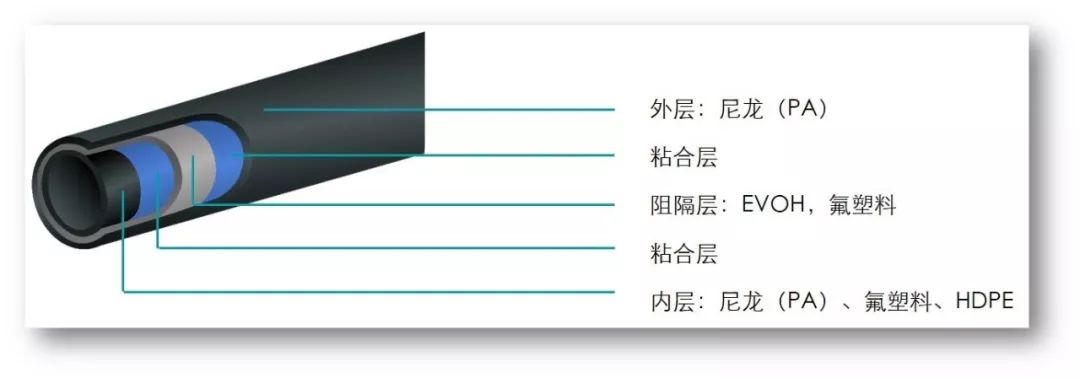
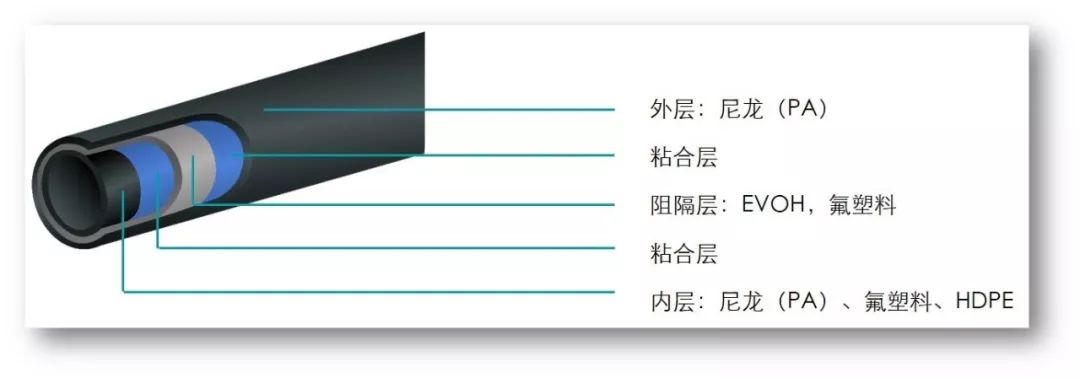
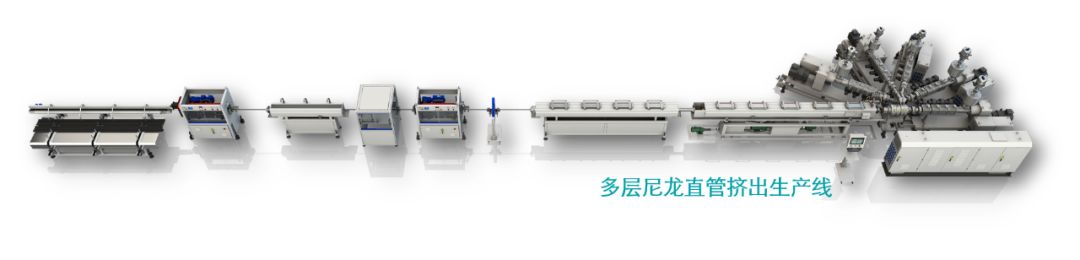
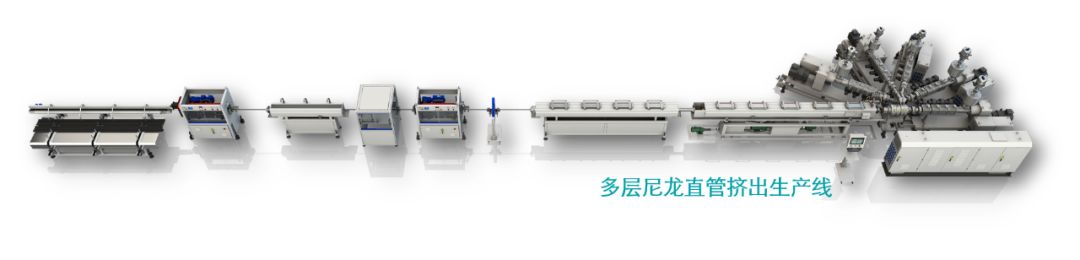
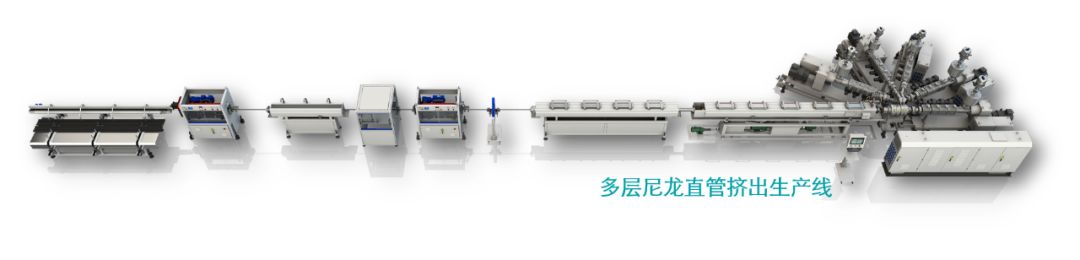
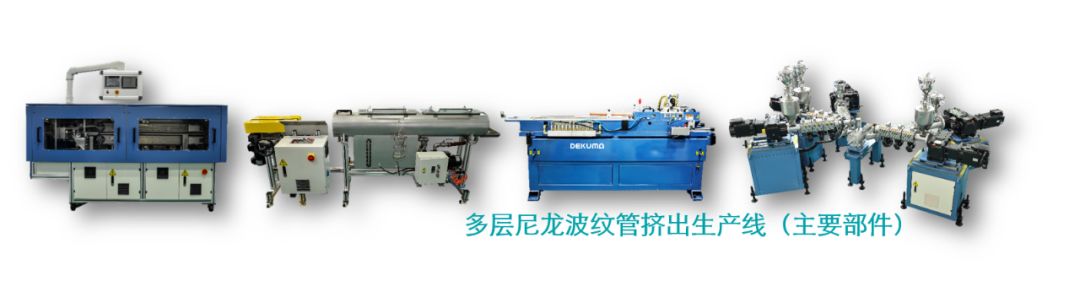
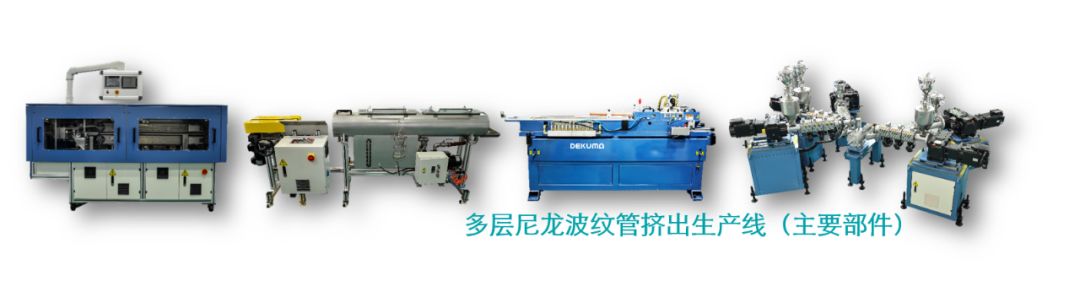
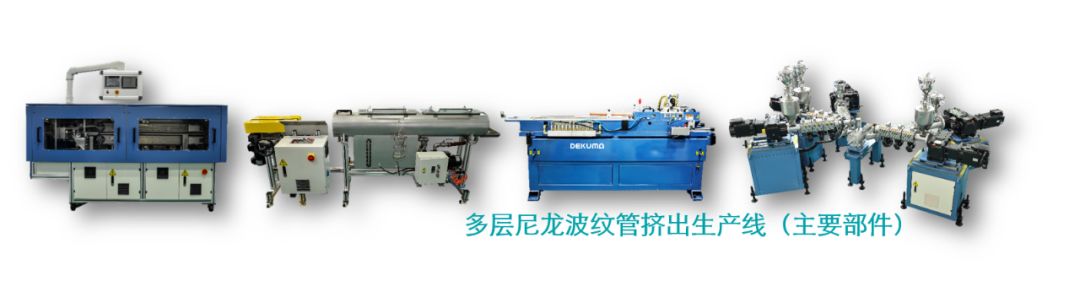
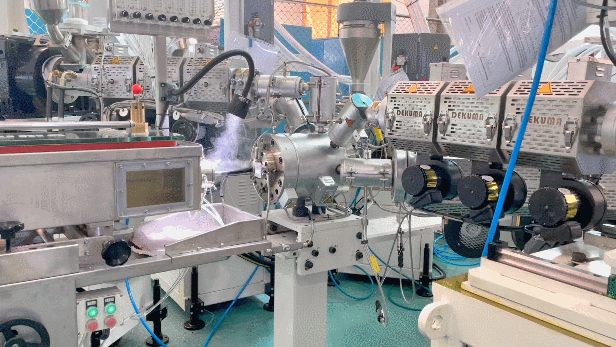
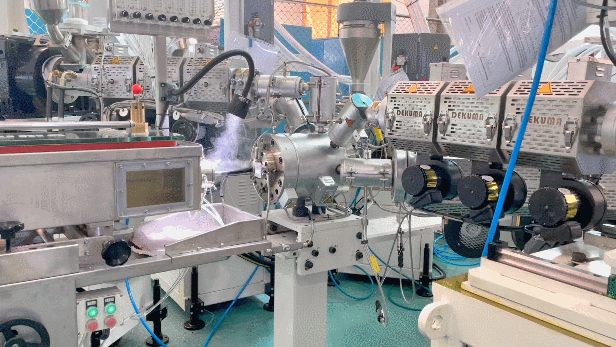
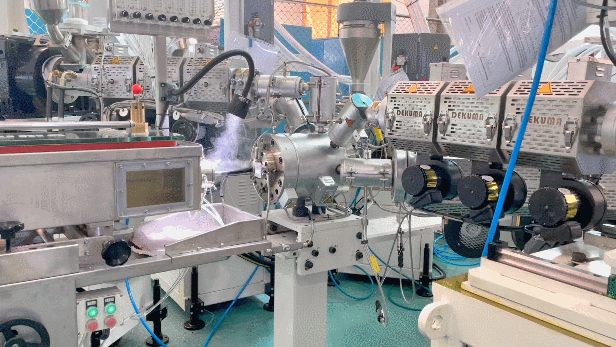
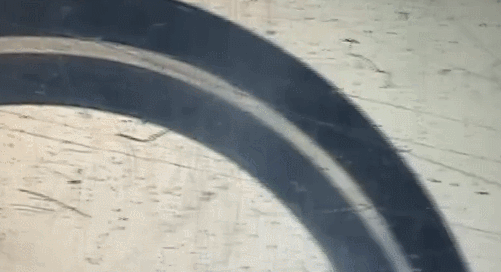
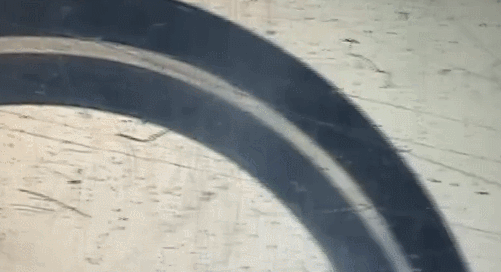
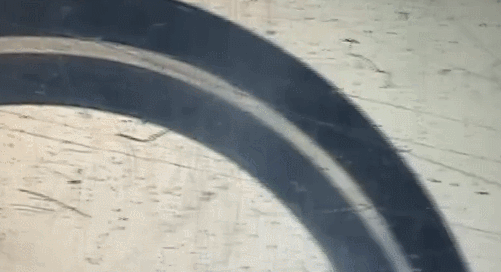
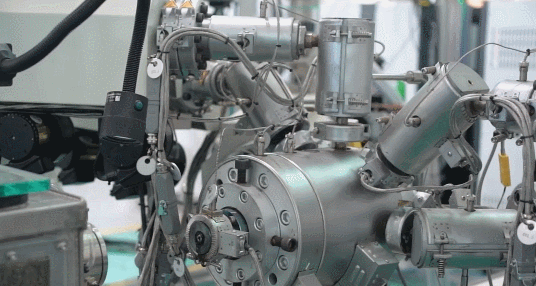
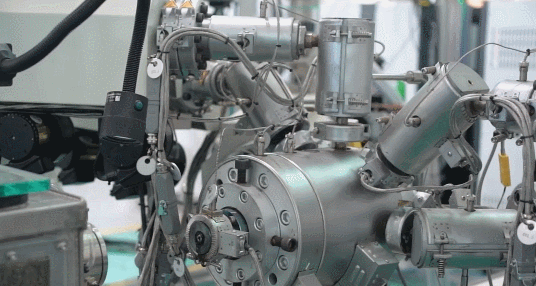
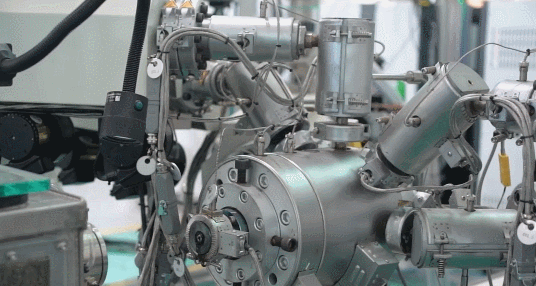