Abstract: This paper introduces an environmentally-friendly and efficient servo hydraulic press for production of backing plate of brake pads launched by Cosmos Presswhich widely used in the brake pad industry in past few years.
Keywords: automobile brake pad, production of steel backing, automatic production.
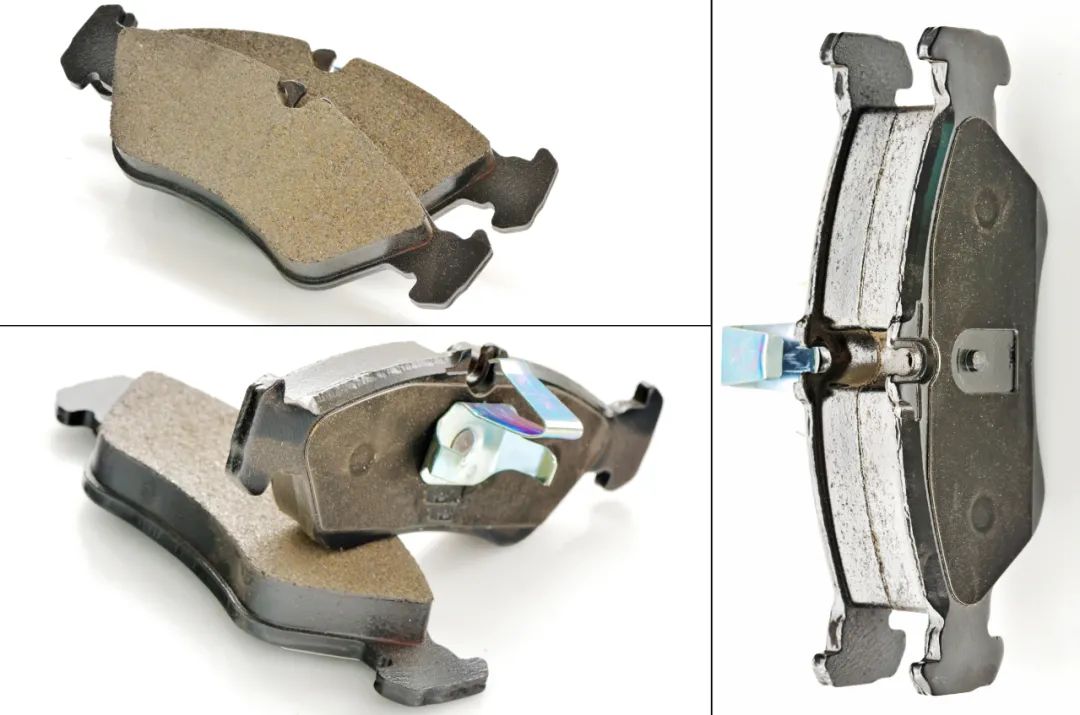
1. Difficulties in production process and special equipment for backing plate
Our investigations in Guangdong, Jiangsu, Zhejiang, Hebei and Shandong district reveal that the production of backing plate has the following features: the steel plate is relatively thick, generally 4-6mm, while the backing plate is generally designed with rivets and holes for installation on the caliper, therefore, the production processes are various and accuracy requirement is high.
At present, in the industry, the conventional punching process is the main production method. The main production equipment are mechanical presses. Some factories will use traditional hydraulic presses in some processes.
The control of quality is difficult in the production process with mechanical press and traditional hydraulic press. The production with mechanical press has a great impact on the service life of die. There is no domestic machine manufacturer to produce precision pressing equipment for backing plate. Some customers with high quality requirements will use imported fine blanking press which improves the quality of backing plate. However, the fine blanking press with price of several millions greatly increases the production costs. In addition, it is not conducive to flexible production with different specifications and in small batches, and affect the competitive advantage of enterprise.
Furthermore, the mechanical press generates great noise during punching process, so it is not environmentally friendly. Workers must wear ear protector for protection, the worse working environment cause difficulties in recruitment. With the improvement of urbanization, a factory which generates noise and is not environmental friendly is often complained, so the working time is greatly limited!
2. Introduction to functional characteristics of Cosmos servo driven hydraulic press
Automobile brake pads are vulnerable parts with large production volume. With the rapid growth of the automobile market and the increase of automobile owner, all automobile brake pad manufacturers are expanding their plants to increase productivity, and new manufacturers are also running into the market.
To meet the needs of customers, Cosmos Press, under the support of the group’s strong R&D strength, has launched a special environmentally-friendly, low noise level and efficient servo driven hydraulic press for production of backing plates. The machine matched with the molds can fully cover the typical production processes of backing plates including 1.chamfer forming; 2.stamping; 3.pin forming and 4.fine stamping;
At the beginning of the design, the characteristics of “large quantity and low price” of backing plate production were known. On the premise of meeting the function, the costs of the equipment should be minimized, and the redundant design should be well controlled, to ensure that each kilogram of steel of the equipment is useful, and each component is appropriate at this position.
3. Advantages of Cosmos servo driven hydraulic press
3.1 Compact structure, easy operation, and automation
This machine is different from the traditional small table hydraulic press. Its hydraulic electrical system is reasonably designed and arranged on top. It is compact, has no obstacles around the machine, and is convenient for operation and installation of the mold. It does not affect the placement and handling of products. It is deeply favored by the workers on site. There is no obstacle around. Therefore, neither single machine automation nor multi-machine automation is affected. The production mode of multi-machine automation device reduces the manpower.
3.2 Rigid and lightweight machine body structure
The machine body structure avoids the “short, flat and fast” method of the small table machine, that is, three platens are made of heavy steel plates to achieve the purpose of rapid design and production. The three platens composed of top platen, moving bolster and fixed bolster are made of high-quality nodular cast iron. The reinforcement structure adjusted by finite element analyses is more reasonable, enhance good strength and small stress deformation, and has more optimized weight and safety factor ratio. Therefore, it avoids the phenomenon of “the wool coming from the sheep”, i.e. customers spending more money on machine weight.
3.3 Low noise level, environmentally-friendly, high-speed and stable hydraulic system
3.3.1 Low noise level and environmentally-friendly
The optimized servo motor hydraulic pump system only generates approximately 70dB to 80dB noise level during operation, and almost doesn’t generate noise in idle time, which greatly reduces the noise problems in the working environment. The operator enjoys moving from mechanical press workshop to servo driven hydraulic press workshop. To a certain extent, it also reduces the pressure of labor recruitment.
3.3.2 Pressure and position accuracy
The moving position and the pressing pressure are controlled and detected by precision linear transducer and pressure sensor. The pressure sensor matched with servo driver control can realize stepless regulation of working pressure. The working pressure for production of large and small backing plates can be set according to demand, which improves the quality and stability of products, and improves the “uncontrollable pressure and vulnerable mold” during punching operation; the pressing pressure can provide data support for new product development according to the size and accuracy requirement of product.
3.3.3 High-speed response
The highlight of the hydraulic system is used of imported Rexroth directional valve matched with the domestic mature two-way large-flow cartridge valve technology which not only realizes high-speed response to meet the production efficiency, but also reduces the manufacturing costs of the high-speed hydraulic system. The specially designed cartridge valve system reduces the resistance of the hydraulic oil flowing at a high speed, reduces the calorific value and the energy consumption, ensures the long-term high-speed response without stuck phenomenon, and ensures 24 hours stable and automatic production of press hydraulic system installed with oil cooler.
3.3.4 Control system
The “PLC+ touch screen + servo driver” control can realize the intuitive and efficient setting of the process flow and parameters. The flexible pressing process is adopted. Based on current backing plate production process and years of experience, Cosmos Press’ machine contains most of the pressing technologies of production process in the market. It can do the pressing process that cannot be completed by the mechanical press, realize the flexible and multi-purpose use of one machine, reduce the expenses and floor areas of production line, and lower the production costs.
Instant and effective action prompts
3.3.5 Unique finishing process structure
Based on the requirements of production process of backing plate, the machine is designed with a special cushion cylinder structure for finishing process. The sheared edge zone and dimensions of backing plate produced by the customer’s mold with the cushion cylinder structure, can reach the precision requirement from main engine factory. A special proportional pressure valve is equipped on the two-way cartridge valve to realize the floating blank holding force during finishing. By adjusting the floating blank holding force, the sheared edge zone of finished backing plate can meet the requirements. Besides, under the support of the floating force, the geometric dimensions of the previous processes of the backing plate will not be affected. A certain leveling effect will also be achieved.
Equipped with a special mold frame, it can be used in the reverse finishing process, that is, the ram cylinder is used for pressing and leveling, and the cushion cylinder is used for finishing. This process action is applicable to products requiring high leveling force.
The finishing process meets the quality requirements of backing plates. Three or four machines are combined to form an automatic line for production of backing plates. Customers do not have to spend millions on purchasing imported machines. It reduces the production costs of products, realizes the flexible production with different specifications and in small batch, and improves the product competitiveness.
4. Other advantages
4.1 Energy saving
The servo motor as the power source of machine. In working, it outputs the torque according to the real-time loads. Its power loss is small, 50% less than the traditional induction motor fixed with displacement pump, and at least 30% less than the traditional induction motor with variable pump.
4.2 High productivity
Its productivity is equal to that of mechanical press. It can complete punching action within 1.3s-1.6s and complete finishing action within 1.7s-2.3s.
5. Conclusions
Its successful development has solved three problems in traditional brake pad production process with mechanical press, i.e. “difficult recruitment & low per-capita productivity, noisy and high energy consumption”, relieves the pressure of environmental protection of an enterprise in production, greatly improves the product competitiveness, creates profits for users, and makes contributions to the development of automobile industry in China.