Talent is the key to enterprise innovation
Recently, Mr. Wang Guiqiu (“Mr. Wang”), Director of DEKUMA Rubber Machinery Business Division, was rated as a “senior engineer”.
Mr. Wang has been engaged in the rubber and plastic machinery industry for more than 20 years. Since he worked in Datong Group in 2000, he has been responsible for the overall development and design of the mechanical main body and hydraulic system of rubber injection machine. He has successively obtained more than 20 patented technologies and numerous R&D achievements, and has been silently contributing to the development of China’s rubber and plastic machinery industry.
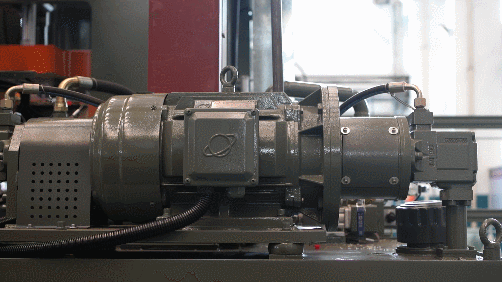
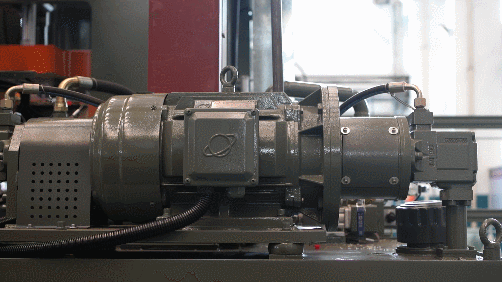
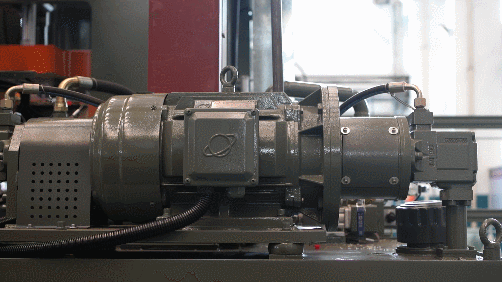
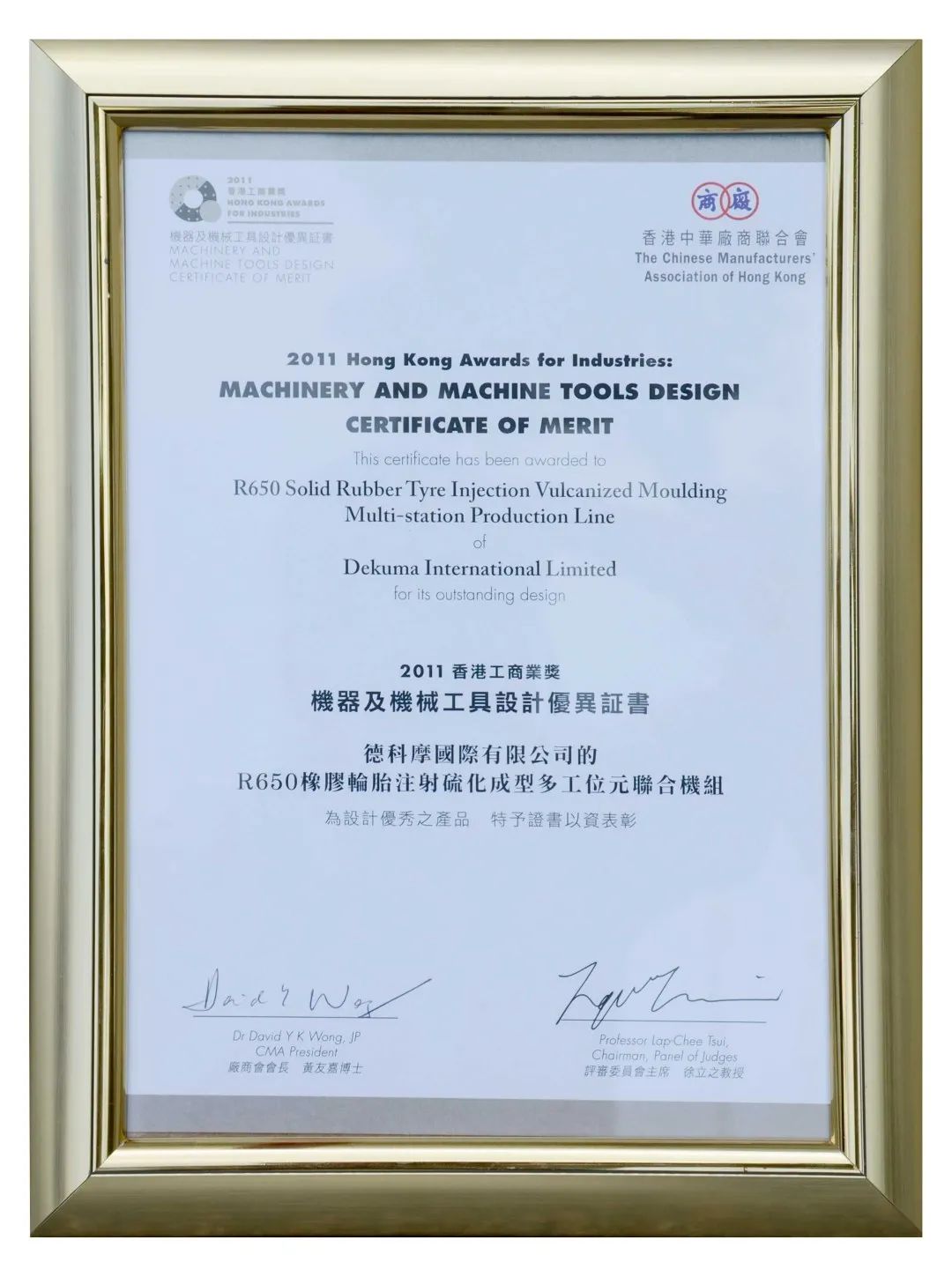
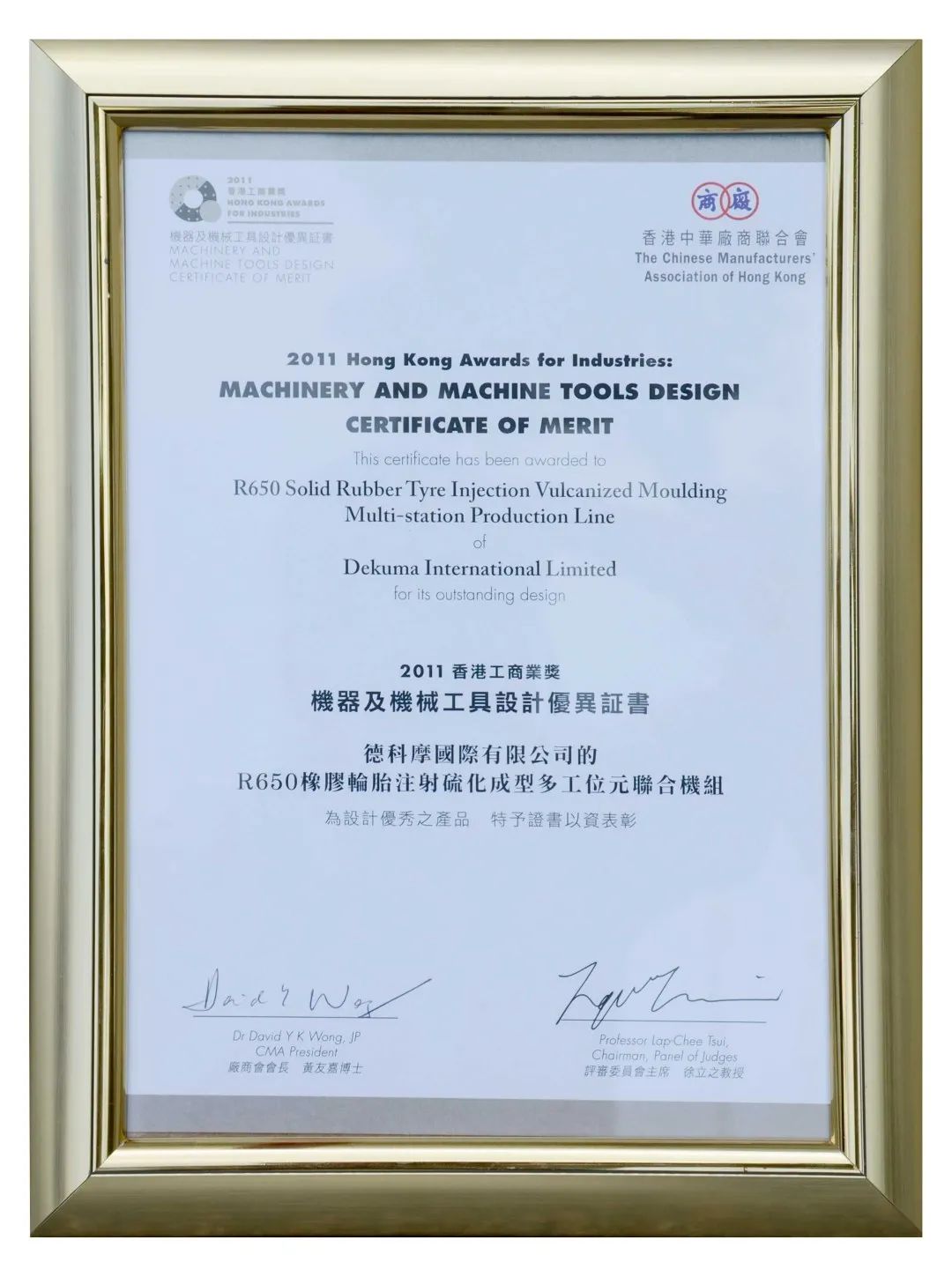
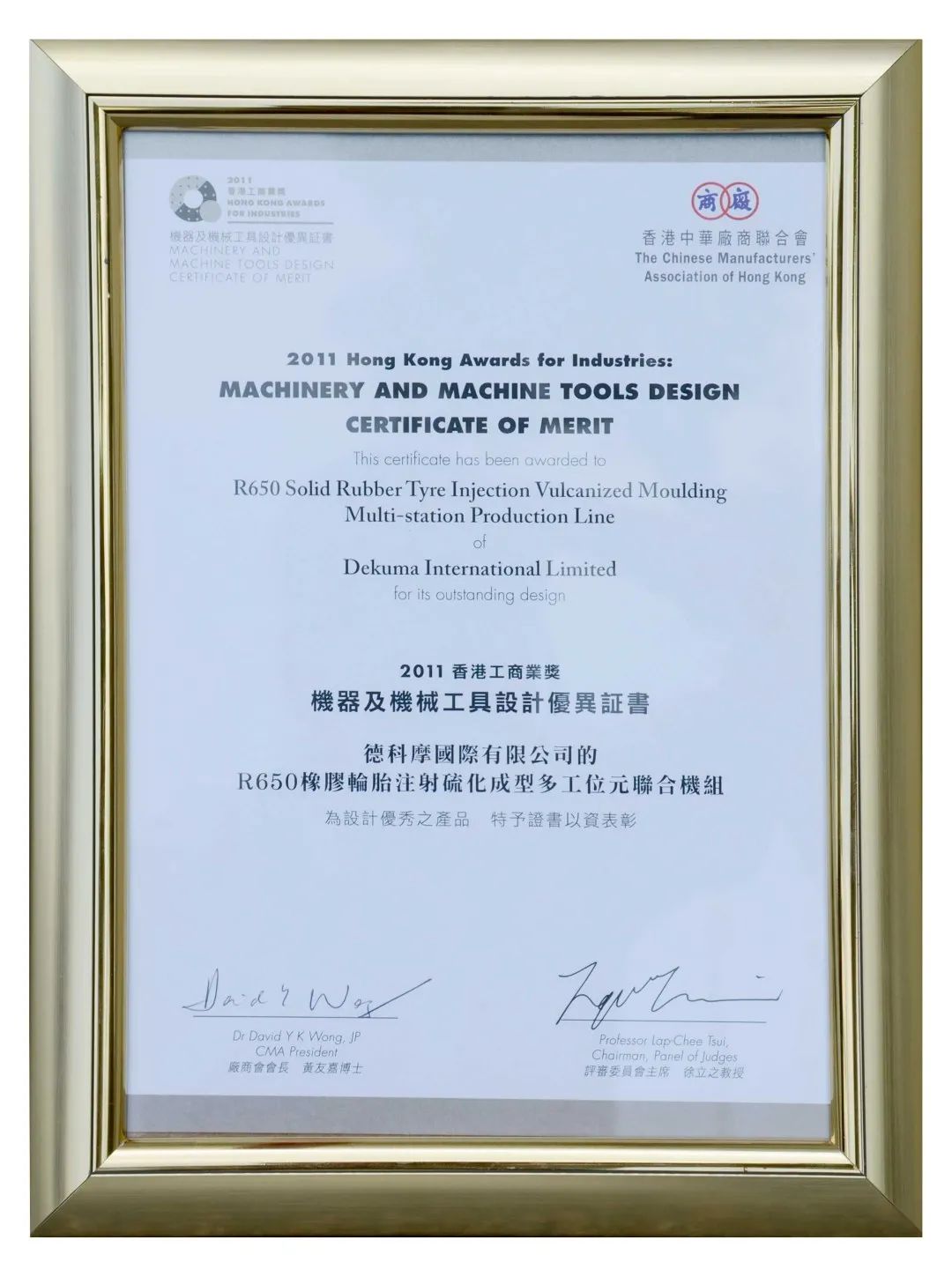
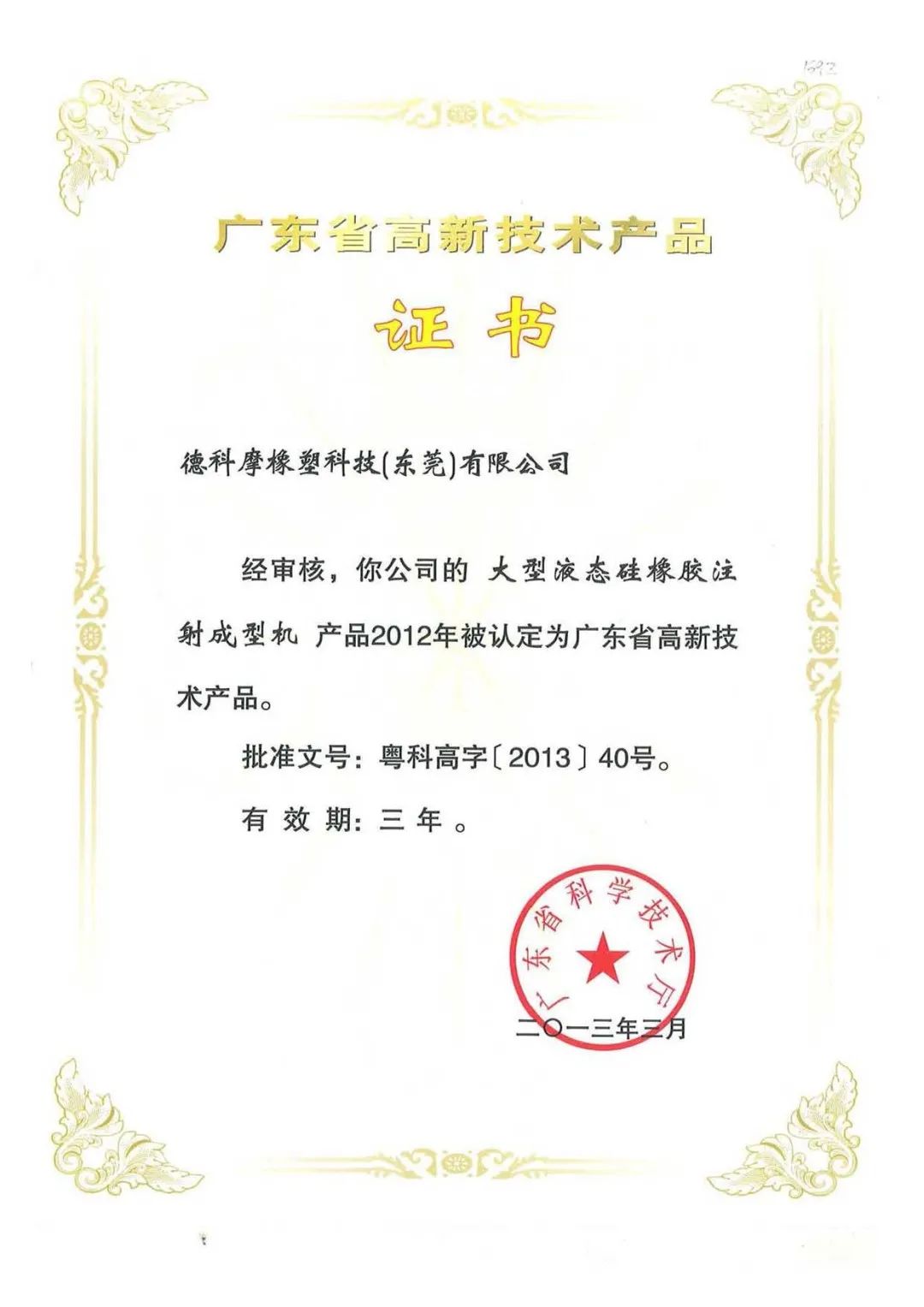
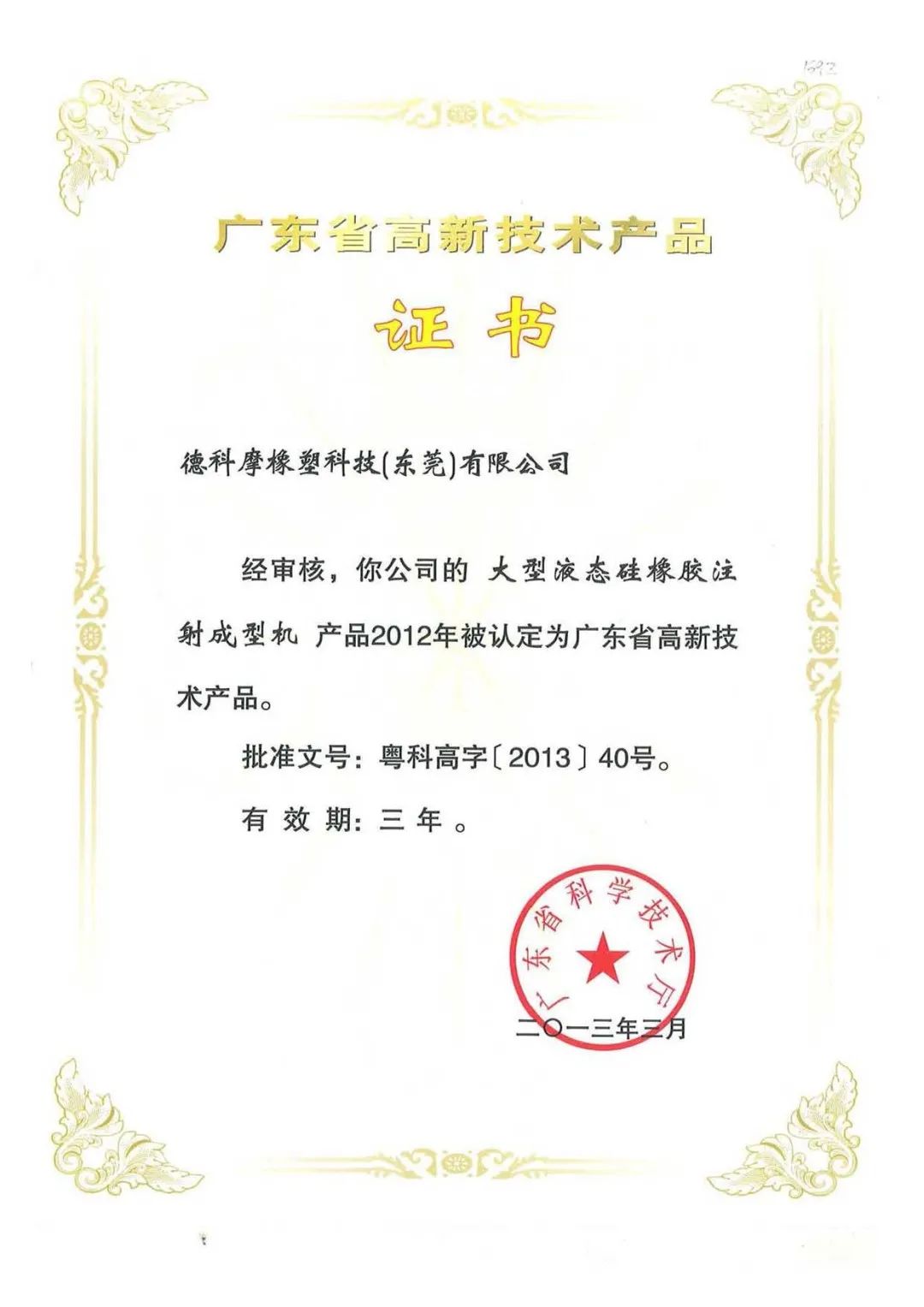
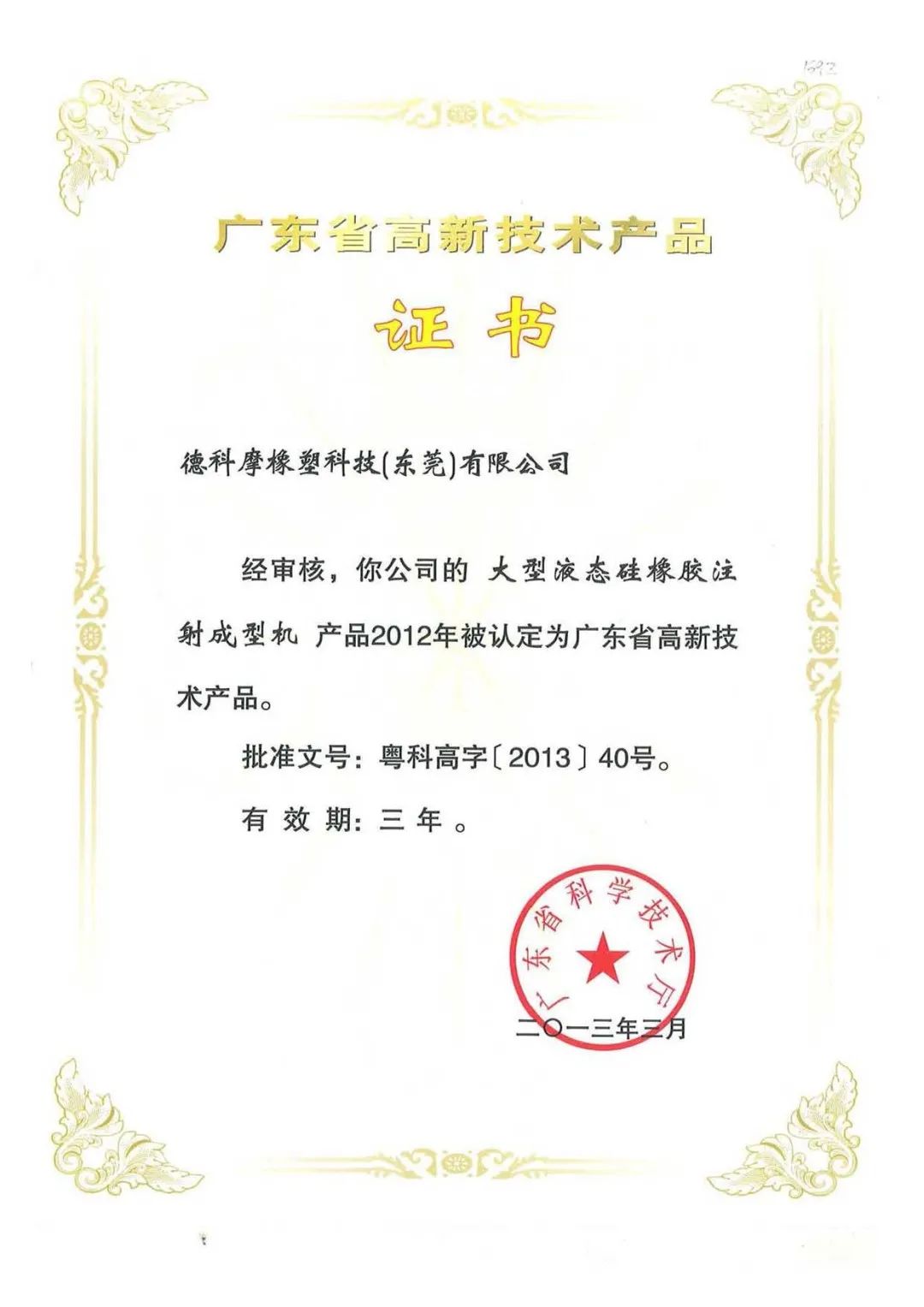
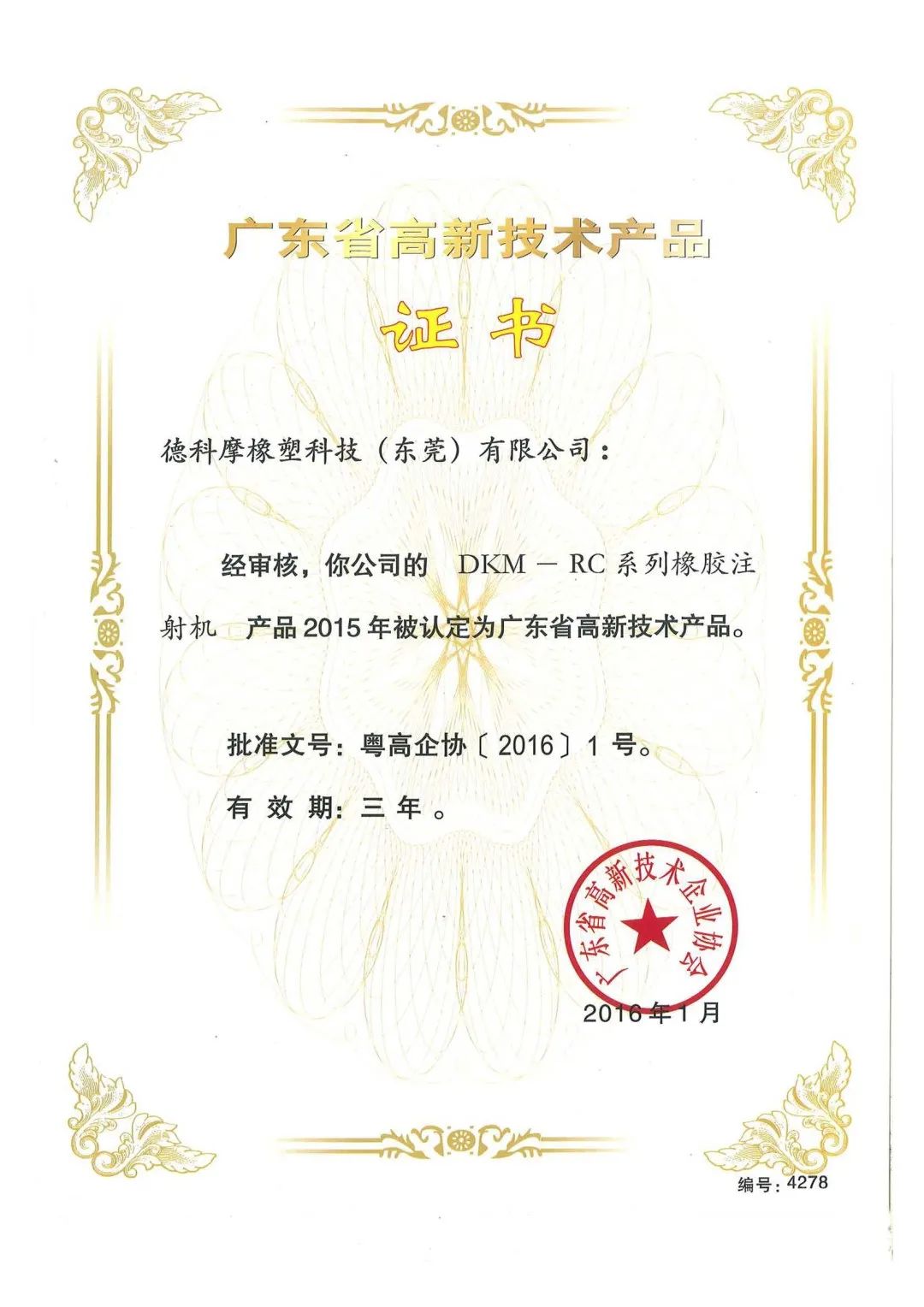
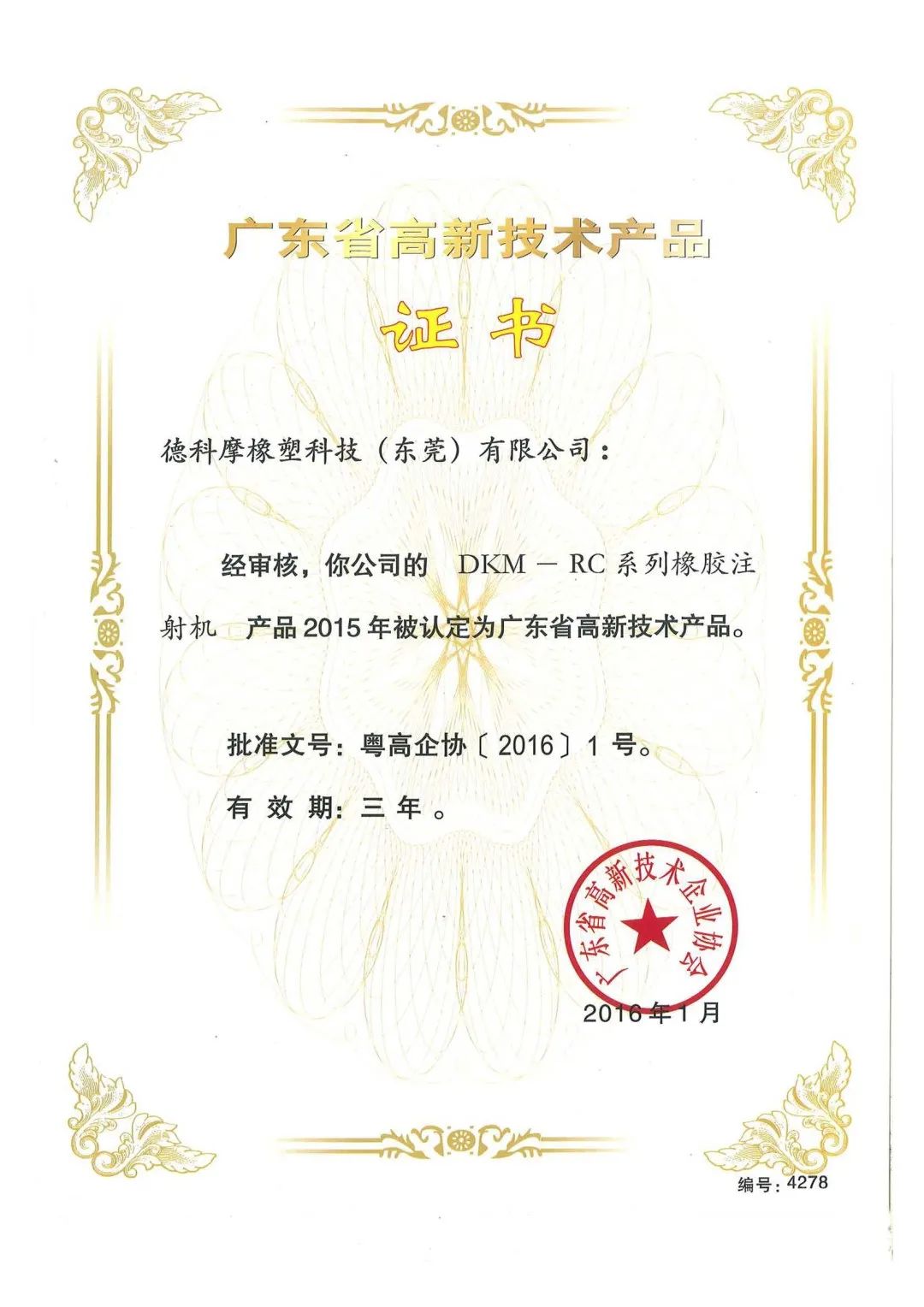
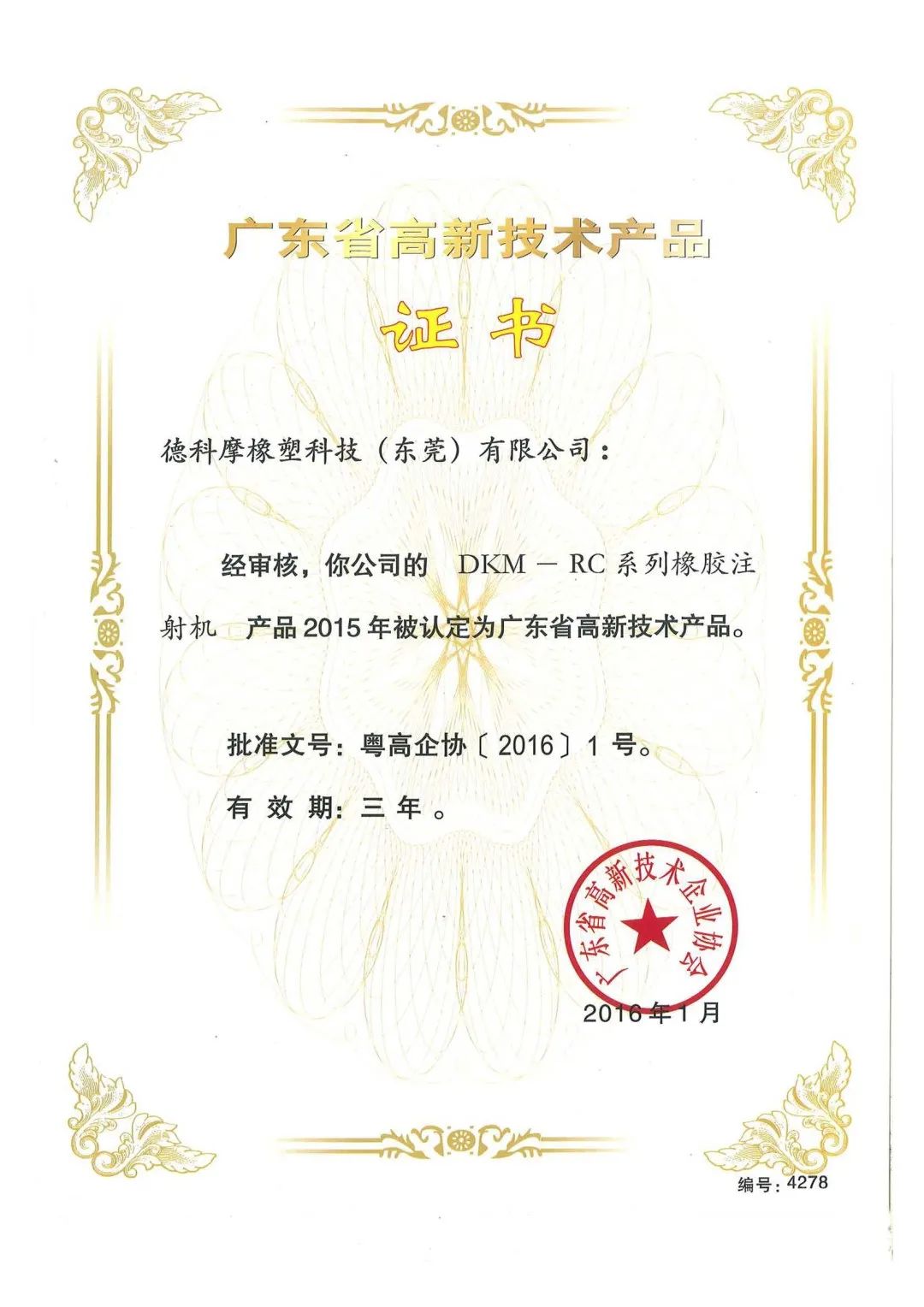
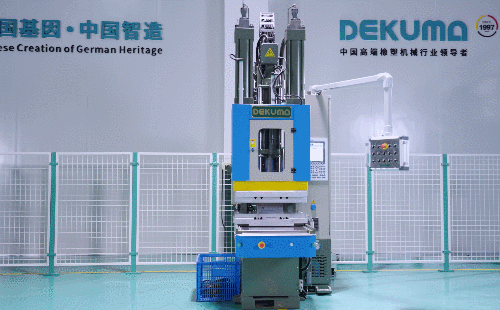
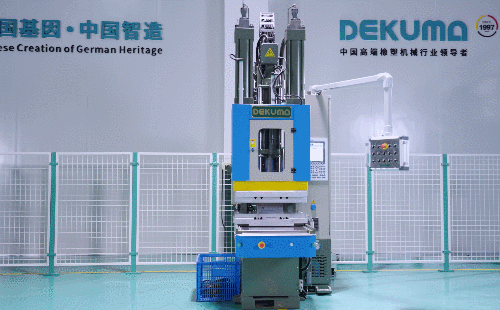
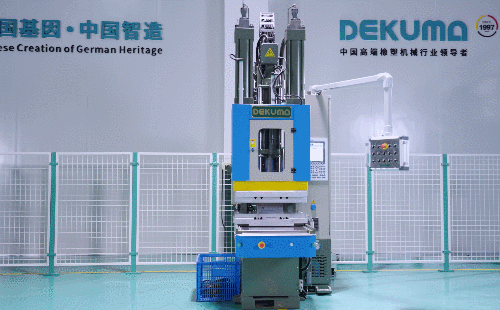
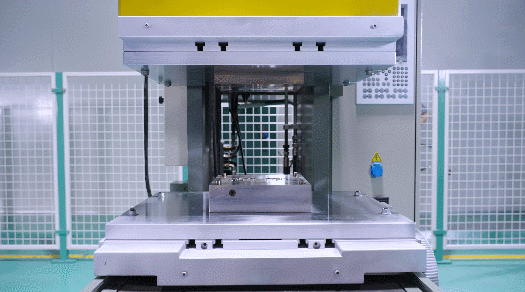
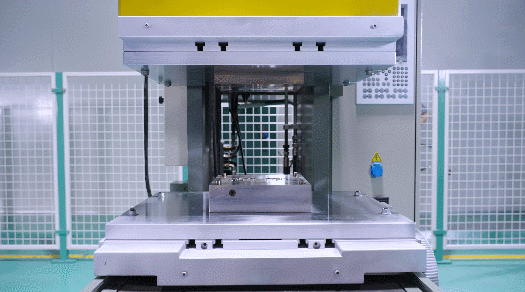
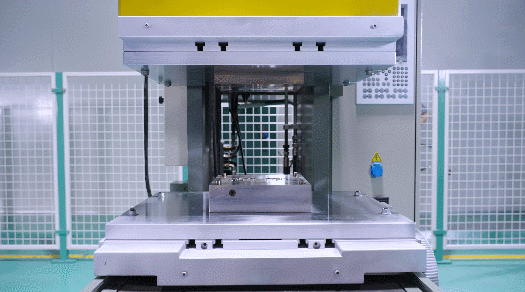
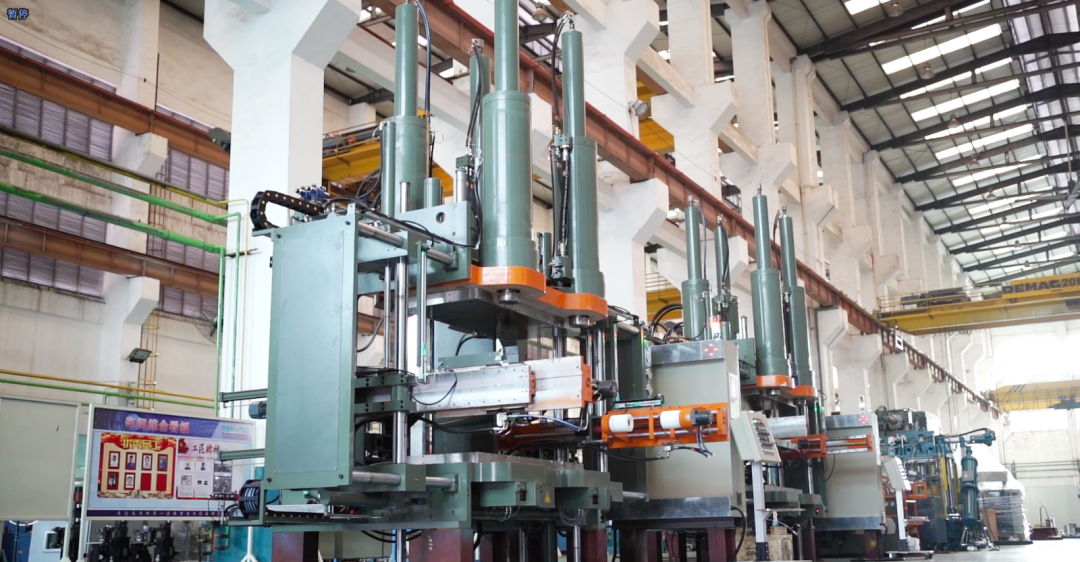
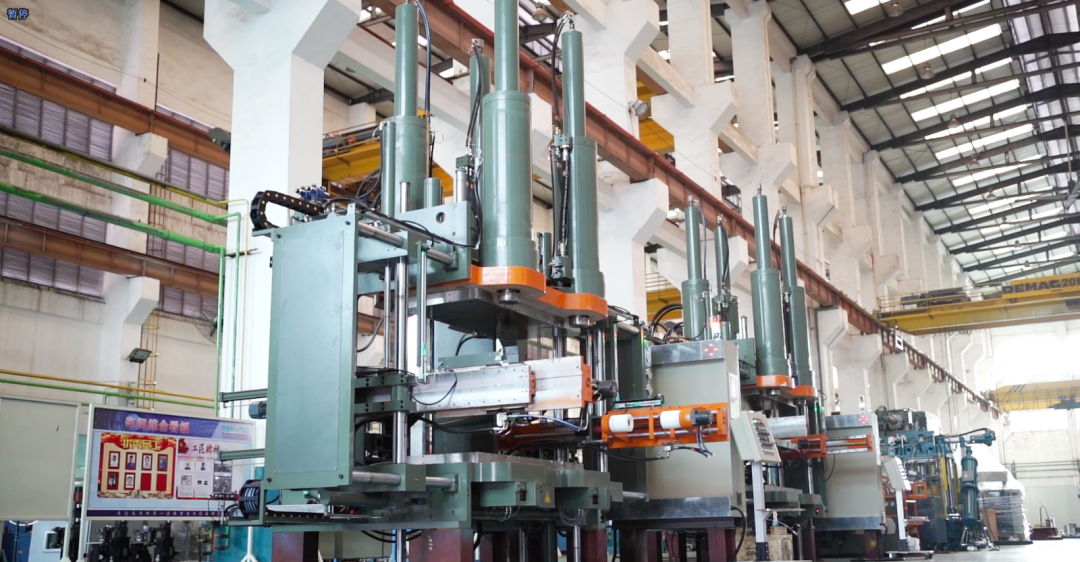
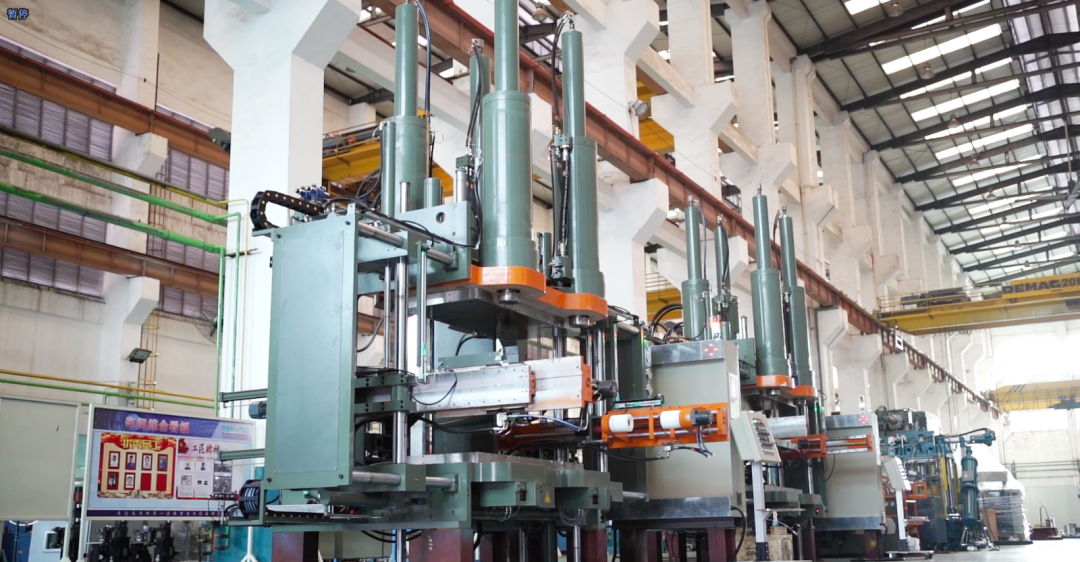
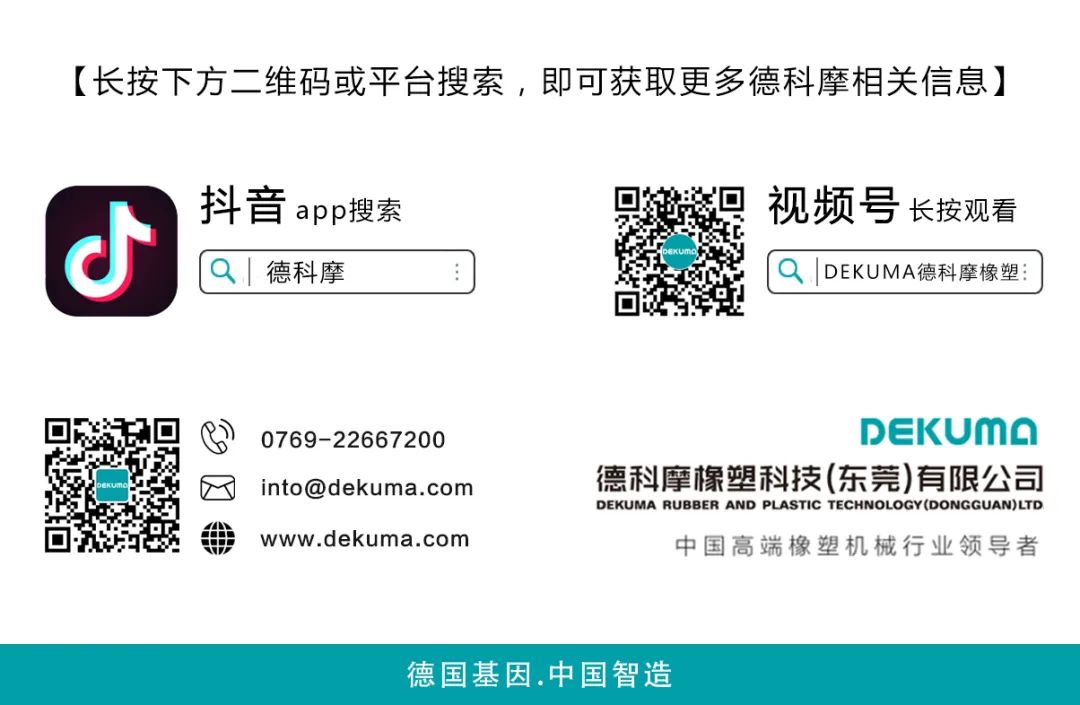
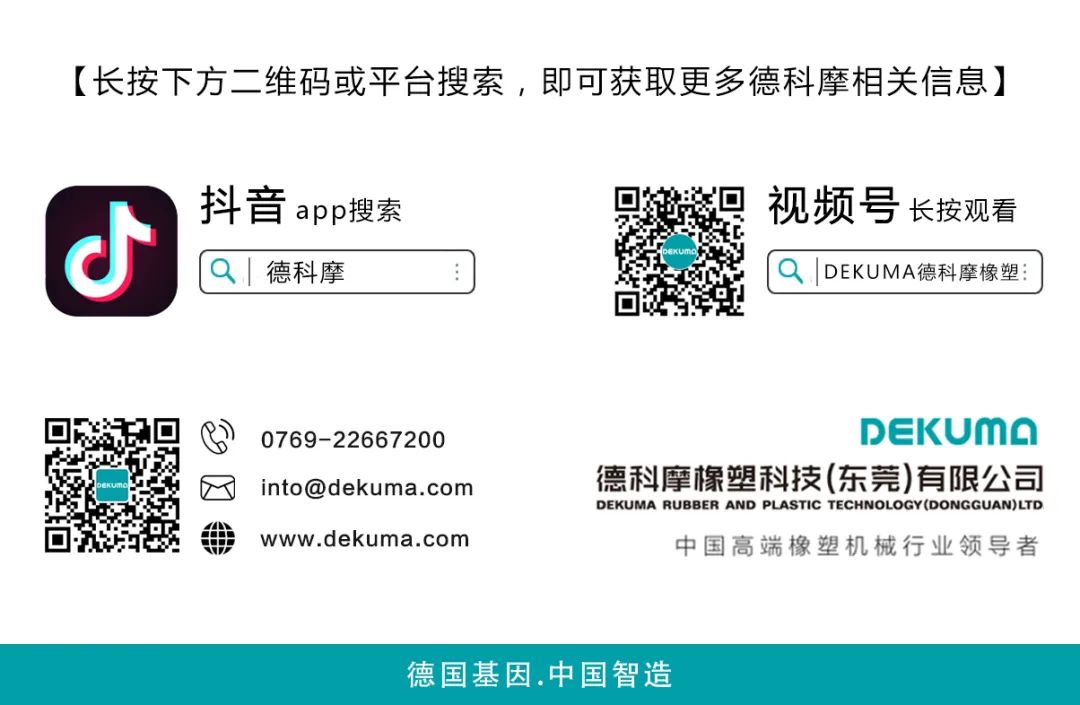
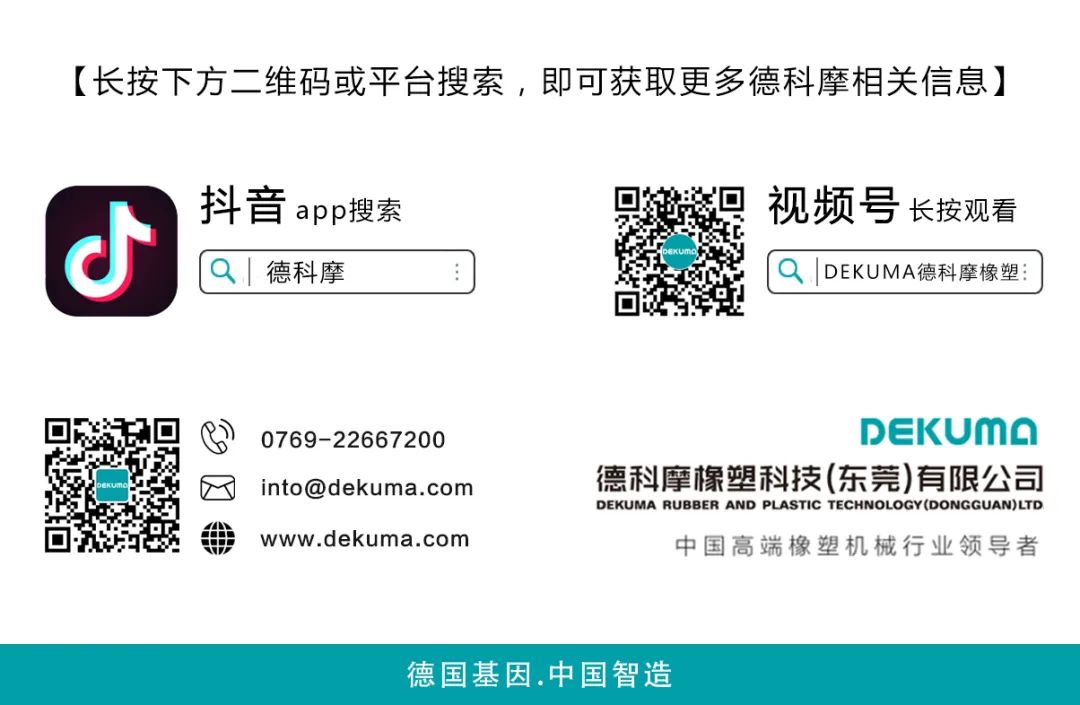
DEKUMA listed into Dongguan Top 100 Innovative Enterprises 2021
At present, although the scale of China’s manufacturing industry ranks among the top in the world, with the gradual disappearance of the demographic dividend and the development of industrial upgrading and transformation, potential problems in the industry are gradually exposed.
Most of the traditional rubber and plastic machinery equipment is mainly low-end, and the automation level and performance of these equipment are still far behind foreign high-end equipment.
For example, traditional production equipment may cause environmental pollution and cause factories to be moved to remote areas. Machines with a low level of automation make workers too labor-intensive, resulting in the dilemma of finding and retaining people. Production equipment in some certain fields has long relied on imports. These are the “unspeakable pain” of the rapidly developing Chinese manufacturing industry!
Dekuma believes that relying on “two substitutions” and “technological innovation” can alleviate these pains. From the transformation and upgrading of equipment to promote the industrial upgrading of the rubber and plastics industry. Complete the transformation from “big” to “strong” and enhance the competitiveness of China’s manufacturing industry.
“Two substitutions” refers to the substitution of imported equipment and the substitution of labor. Only when China can independently develop and produce high-end equipment can we gradually reduce our dependence on imported equipment, and enable more domestic manufacturing companies to realize their original aspirations and help the rubber and plastics industry produce intelligent manufacturing.
“Innovation” is the difficulty of Chinese manufacturing and the pain of Chinese manufacturing, but it is also the light of hope and breakthrough of Chinese manufacturing. Since the reform and opening up, from Chinese manufacturing to Chinese “intelligent” manufacturing, only when manufacturing enterprises take innovation as the first driver can we drive China into an era of innovation in an all-round way.
Recently, Dongguan Science and Technology Bureau released the Announcement on the List of Dongguan Innovative Enterprises to Be Recognized in 2021.
According to the implementation of Dongguan Innovative Enterprise Cultivation Plan, based on the national high-tech enterprises, no more than 100 high-tech enterprises with strong innovation ability, fast growth and good development potential will be selected as the top 100 innovative enterprises; the focus will be on promoting enterprises to break through the national and provincial R&D planning technologies in key areas, cultivated them as listed companies on the Science and Technology Innovation Board and the Second Board, and built into Hidden Champions of the industry.
Since 2012, DEKUMA has beenContinuously meet the new needs of customers in the selected market segments, actively pay attention to the pain points of customers, and continue to meet customers through technological innovation, gradually replace imported equipment in more and more industries, and gradually ease the difficulty of recruiting for customers, and the common problem of keeping people difficult.
The highly representative and special machines for segmented markets such as automobile rubber seal strip angle splicer, rubber track machine, automobile nylon multi-layer oil tube production line, microduct extrusion line and automobile steel back special machine are constantly researched and developed in an innovative way.In these industries, Dekuma’s equipment has been highly recognized by global industry benchmarking companies and has reached long-term strategic cooperation.
In the List of Dongguan TOP 100 Innovative Enterprises to Be Recognized in 2021, DEKUMA was successfully shortlisted into Dongguan Top 100 Innovative Enterprises.
Over the years, DEKUMA has always focused on the R&D, production and sales of rubber injection molding machine, pipe extrusion production line and hydraulic press, as well as providing customers with after-sales services of related products. DEKUMA is committed to providing global customers with turnkey solutions for complete sets of equipment.
Its products are widely used in many fields such as auto parts, building materials, energy transmission and electronic communications. Customers are located in dozens of countries in Europe, America, Latin America, the Middle East and Southeast Asia, etc.
In the future, DEKUMA will continue to dig deep into the industry-specific markets, devote itself to providing customers with industry-specific equipment, and tailor-made one-stop solutions for customers to meet diverse production needs.
Press and hold the QR code below to enter the website of Dongguan Science and Technology Bureau.
Show Preview丨DEKUMA Will Participate in K 2022
NO.1 About the K Show in Germany
K as the world’s leading trade fair, started in 1952 and is the world’s largest event of rubber and plastics industry. It is held every three years, and 21 sessions have been successfully held so far, and it will usher in the 22nd event in 2022.
NO.2 About DEKUMA
DEKUMA has always been focusing on the R & D, production and sales of pipe extruder production line, rubber injection moulding machine and hydraulic press. Our products are widely used in auto parts, building materials, energy transmission, telecommunications and other fields.
Adhering to the concept of “high precision, intelligence, automation and customization”, DEKUMA will bring our latest R & D results to K Show:
1. DKM-EII75x36 parallel twin-screw extruder commonly used in the production of PVC pipes;
2. DKM-RC40Se rubber injection moulding machine commonly used in the corner connection of automobile rubber seal strip.
(1)、DKM-EII75x36 parallel twin-screw extruder
Equipped with the screw and barrel with high L/D ratio optimized by the DEKUMA engineering team, it is often used to produce high-quality UPVC and CPVC pipes, ensuring good plasticizing effect and increasing output.
The DKM-EII75x36 twin-screw extruder to be exhibited at K Show is a new model launched by DEKUMA, suitable for the production of small and medium size PVC pipes. It’s energy-saving, efficient, stable and reliable!
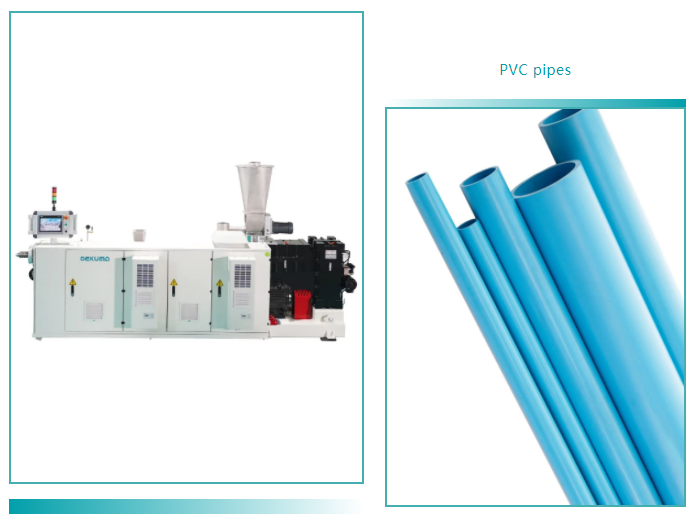
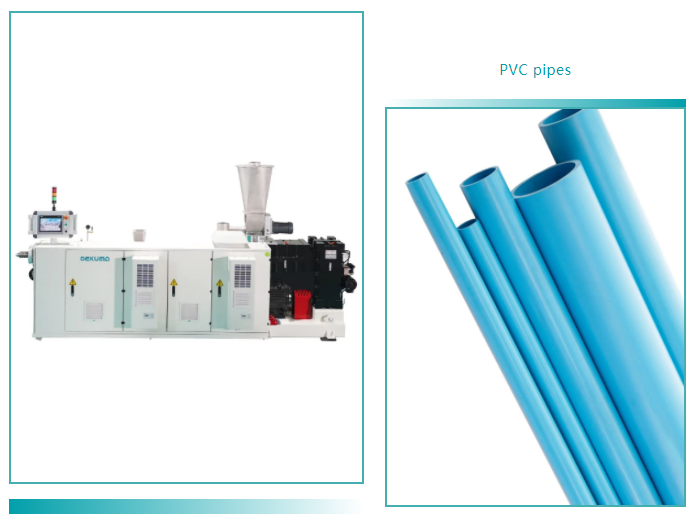
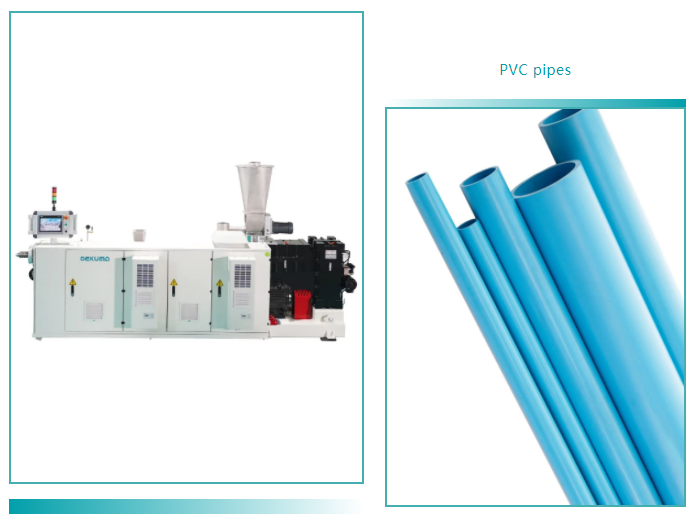
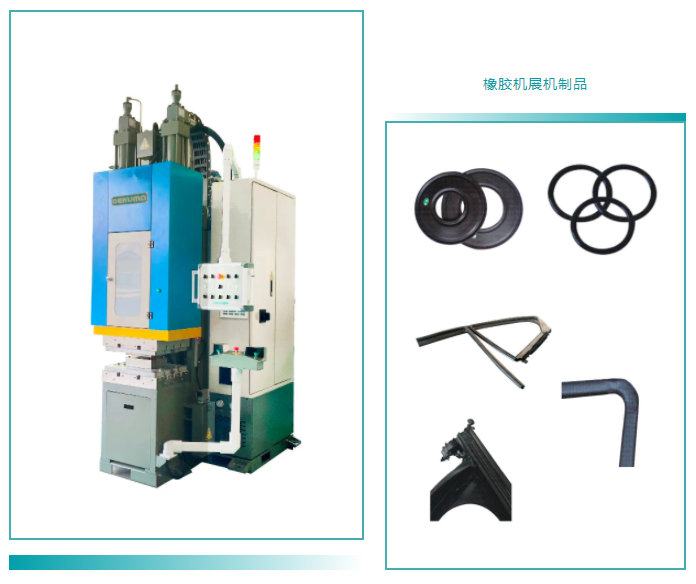
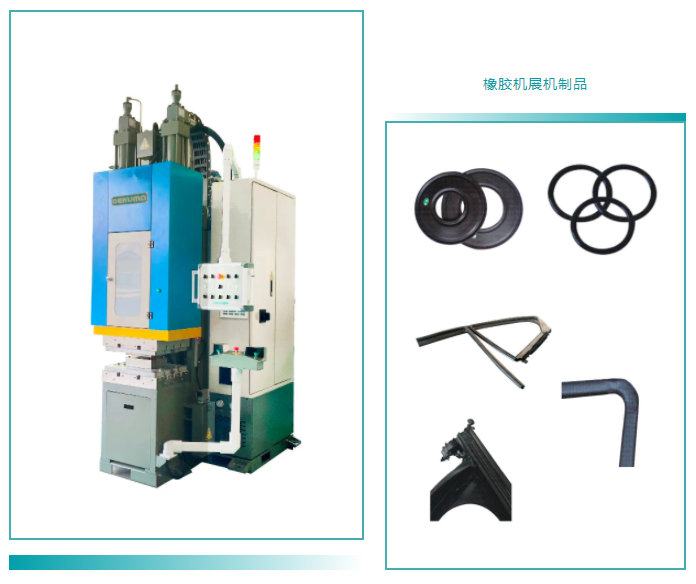
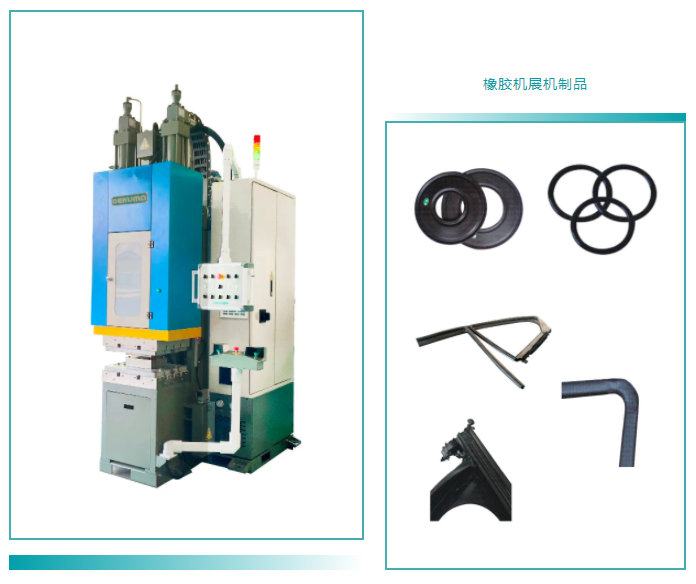
Welcome to DEKUMA booth!
• Booth No.: Hall 15 / A37
• Exhibition time: October 19-26, 2022
• Venue: Messe Düsseldorf, Germany
Please scan the QR code to access the official website of K Show 2022 for buying the tickets.
Advantages of Dekuma’s brake pad backing plate press (Part Ⅱ)
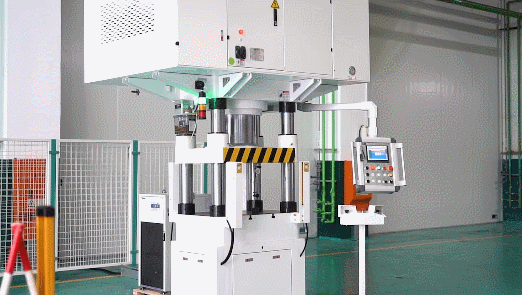
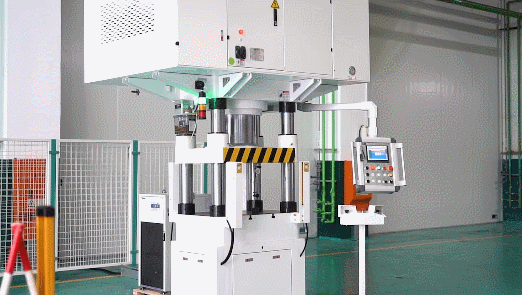
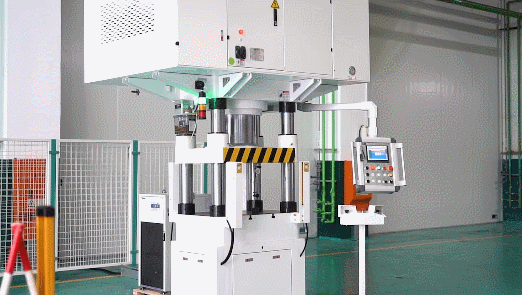
#02
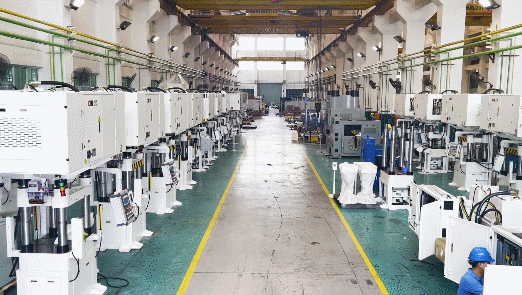
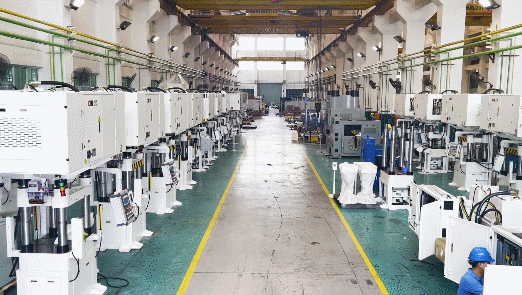
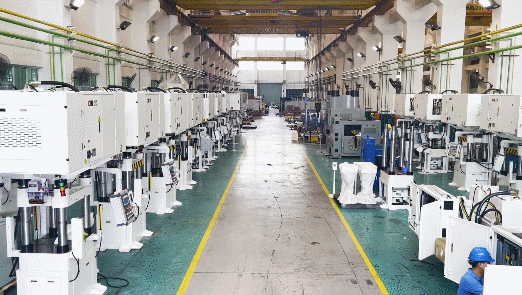
#03
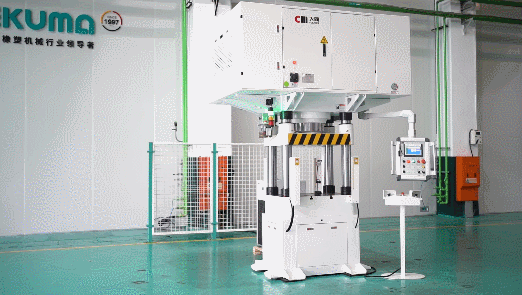
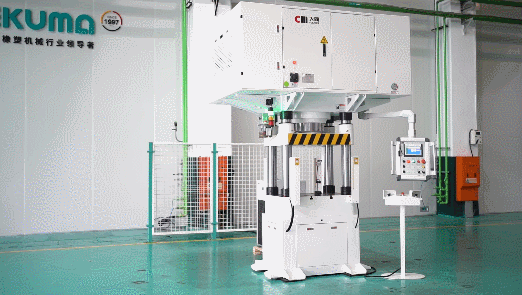
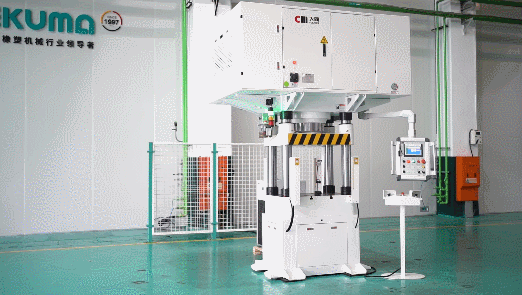
Advantages of Dekuma’s brake pad backing plate press (Part I)
Traditional brake pad backing plate hydraulic press is particularly noisy during production process,seriously affecting the working conditions of workers.
Not to mention wearing earplugs when starting work, the factory will often be complained by nearby residents.The working hours are very limited.
According to the process characteristics,DEKUMA adopts hydraulic press with a servo motor driving oil pump to replace the traditional punching machine to produce brake pad backing plate.
Traditional punching machine has no acceleration and deceleration functions.Instead, it produces by the collision and extrusion of the upper and lower dies. It will make noise when colliding.
But the servo press can slow it down before the collision.Then try to reduce the noise of the collision as much as possible.
Our steel backing hydraulic press can be almost silent when in standby.The impact force during operation can also be much lower than that of traditional punching machine.Reducing the working noise from a maximum of 120dB to 75-78dB,workers don’t need to wear earplugs when using DEKUMA steel backing hydraulic press.
If you feel better, your work will definitely be easier.The product qualification ratio will also increase.And the problems such as difficulty in recruiting workers or limited working hours due to loud noise will be easily solved.
DKM new rubber track production machine exported to South Korea
Recently, DEKUMA’s upgraded and optimized new RC480 automated rubber track production machine has been commissioned, and successfully exported to South Korea and arrived at the customer’s factory.
This customer is one of the largest auto parts manufacturers in South Korea, with production bases in many countries and regions, such as China, Europe, Southeast Asia and South Korea headquarters where DEKUMA’s rubber track machines are widely used.
DEKUMA has been cooperating with this customer for more than 10 years, and continuously improves equipment during the cooperation, and creating greater value to the customer.
Today, let’s see how DEKUMA’s rubber track production machines meet customer needs and keep improving.
Excellent performance of DEKUMA’s rubber track production machine
High degree of automation, reducing labor intensity and manpower requirements
In the past, the traditional production of rubber track required manual feeding, demolding and product retrieval. Generally, the production of a rubber track of several hundred kilograms required 3~4 people to work together.
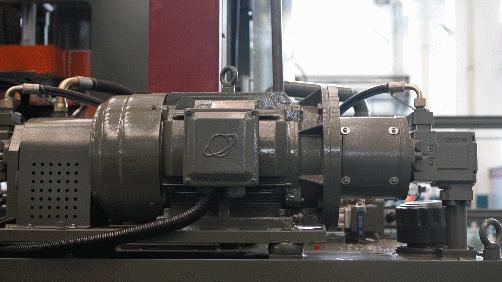
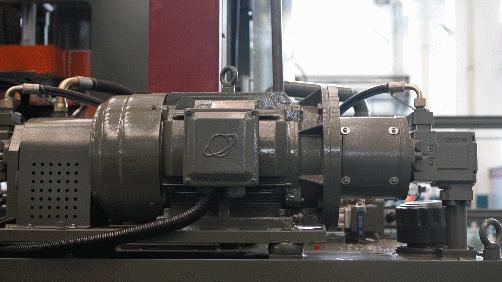
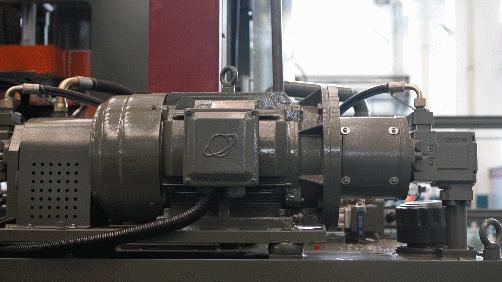
#02
Overcome steel wires week links, and improve the service life of track
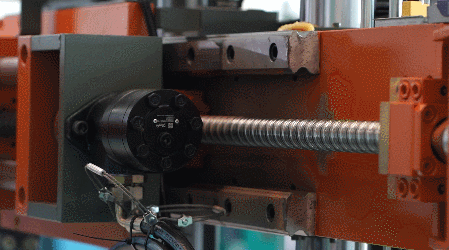
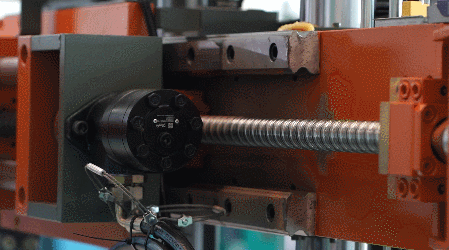
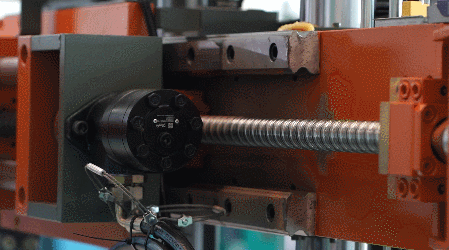
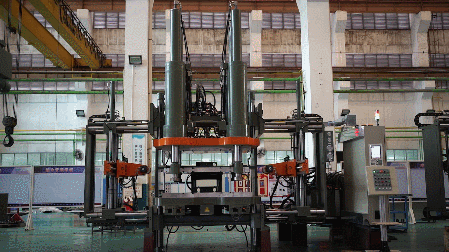
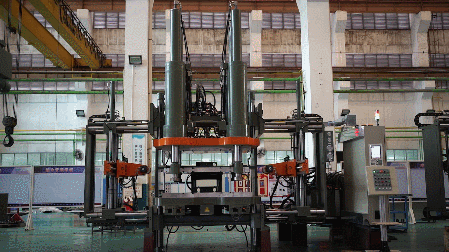
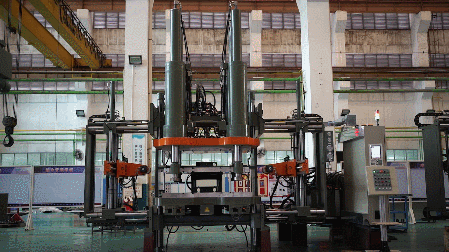
Advanced non-dynamic clamping and vulcanization structure reduces energy consumption in production process
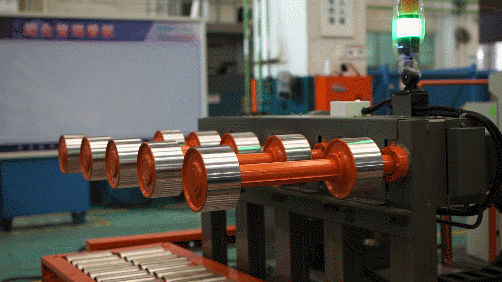
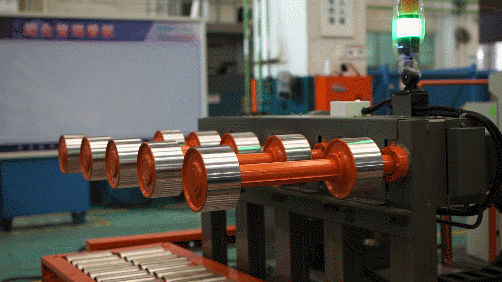
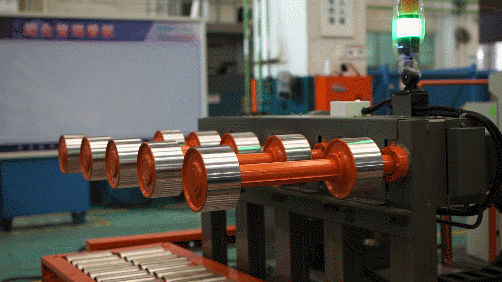
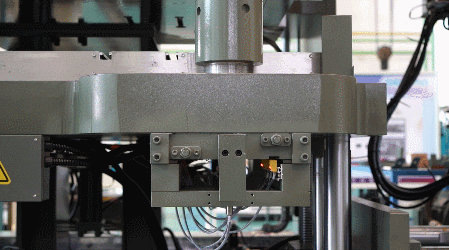
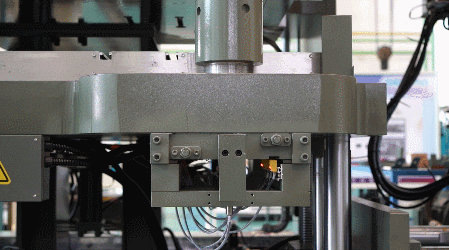
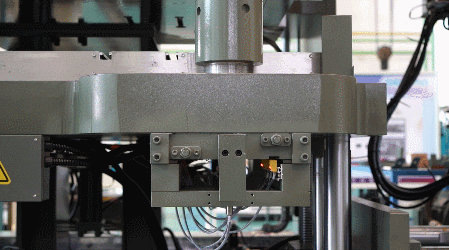
#04
Highly intelligent operating system realizes simple operation
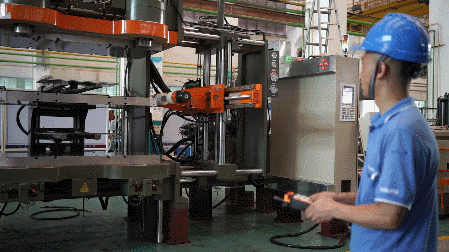
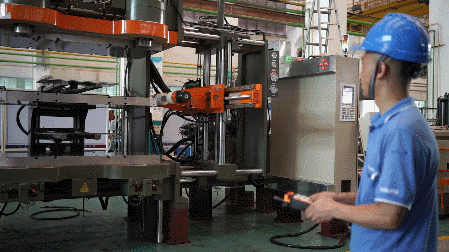
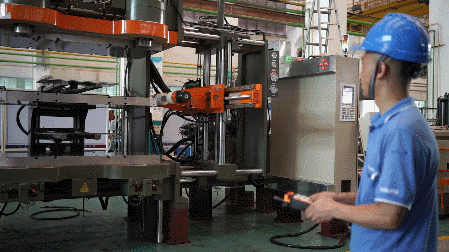
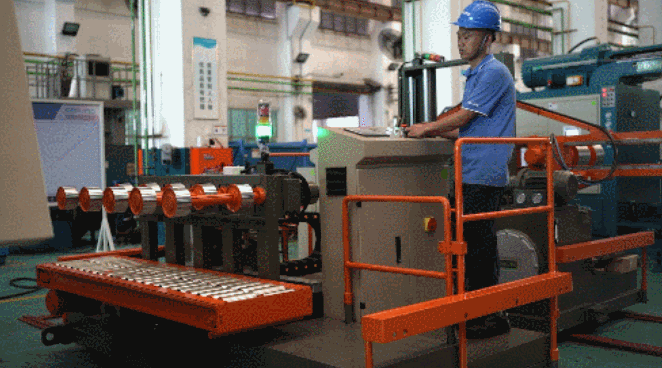
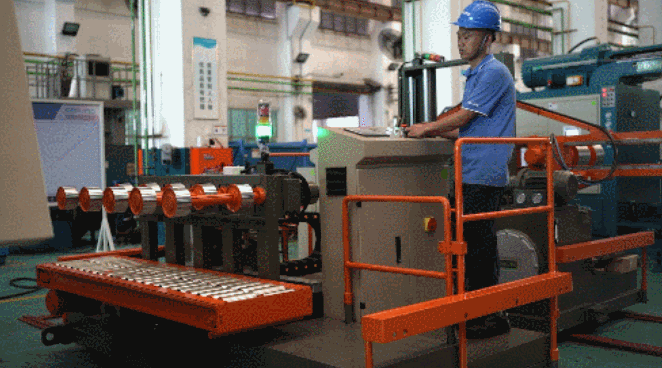
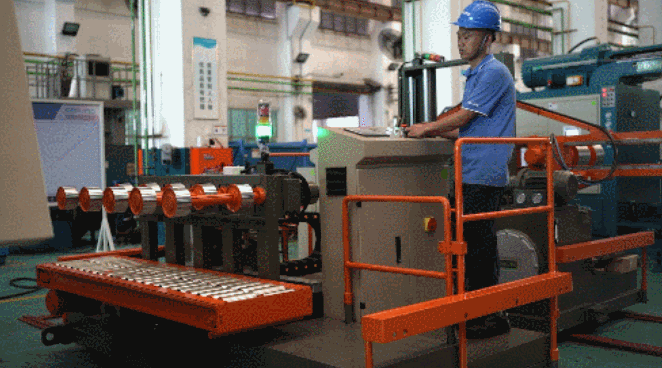
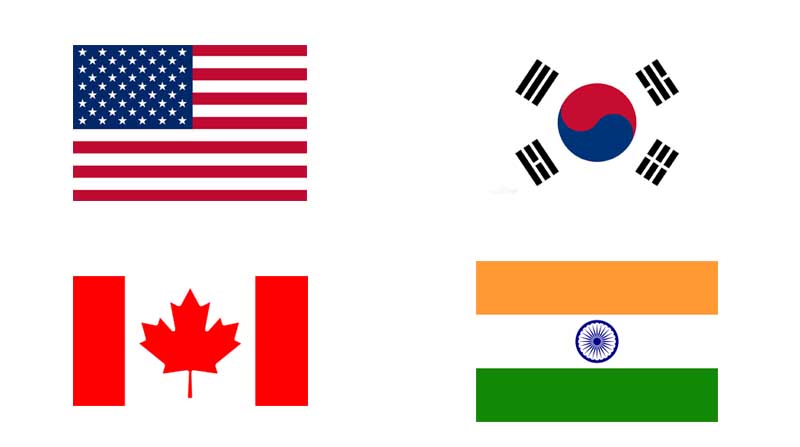
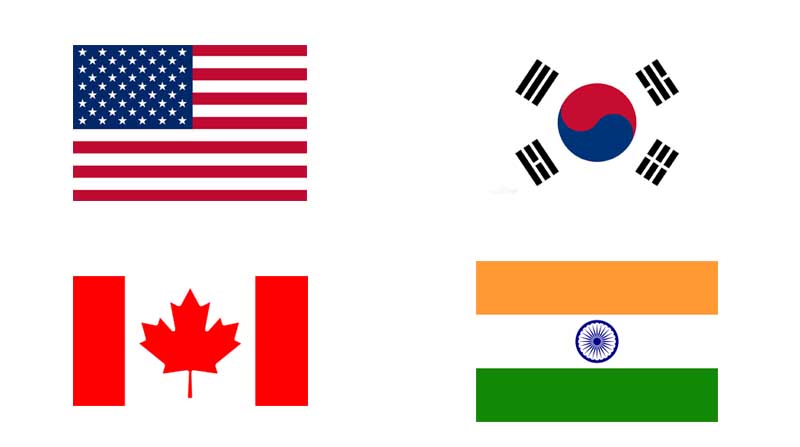
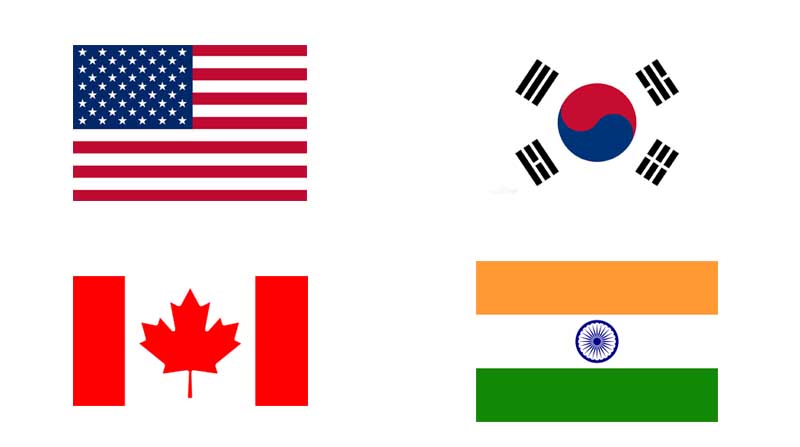
PTFE Moulding Hydraulic Press Key Technology and Application
Abstract: This paper analyzes the production process of PTFE compression molding, and summarizes the causes why conventional pressing pressure and pressing process are easy to cause product defects and scraps.
To solve the problems of surface patterns, cracks, discoloration, hidden cracks, etc., the hydraulic press team of Dekuma has developed a precision servo hydraulic press for blank pressing of PTFE powder product, and solves the problem for customers from the root.
01 Introduction to PTFE Properties
PTFE, known as the “king of plastics”, features many excellent properties including colorless, non-toxic, wide temperature resistance, chemical inertness and low coefficient of friction.
It serves as one of the important materials that are indispensable to all industrial sectors, e.g. automobile, national defense, machinery, chemical industry, electronics and other industries. It can also be made into PTFE pipes, rods, belts, plates, etc.
02 Commonly Used Methods of PTFE
The most common method is compression molding when processing products with PTEE.
The process of compression molding goes roughly as follows: raw material inspection → mashing and sieving → measuring → molding → semi-finished product inspection → sintering → cooling → finished product inspection → packaging.
After investigation on the common problems encountered during production of PTFE compression molding, it can be found that the improper operation of pressing pressure and pressing process may easily cause product defects and scraps, and the unstable pressure output serves as the main reason for cracks.
On the basis of understanding the customer’s process, the hydraulic press team of Dekuma has developed a precision servo hydraulic press for blank pressing of PTFE powder product, and solves the problem for customers from the root.
03 Advantages of PTFE Powder Blank Precision Molding Machine
(1) Slow Pressure Rising and Controllable Time
For powder compression, the time will significantly affect the effect of product molding. In case that the speed is too fast, exhaust will be insufficient, which may easily cause problems such as surface patterns, cracks, and large differences in density between both ends and the middle.
For the time control of pressurization, the hydraulic press adopts servo motor oil pump hydraulic system to solve the problem. Under the cooperation of hydraulic pressure and electricity, it has developed a controllable function of slow pressurization based on the set pressurization time, and the pressurization time is controllable from several seconds to dozens of minutes.
(2)Almost no pressure impact and fluctuation in pressurization stage
At the critical point of signaling pressure, most common hydraulic presses will experience the process of overshoot – fallback – stabilization due to inconsistent pressure repeatability each time.
Under the cooperation of server and plc program, the hydraulic press can control the critical point of signaling pressure well under the high sampling frequency and high-speed scanning cycle.
Thanks to the research results of hydraulic team of Dekuma for years, the set target value can be achieved under cooperated control of the server and the plc program. In the pressure holding stage, the pressure fluctuation is controlled within 1 bar, which can also maintain long-time operating of oil pump without damage.
Due to the specific characteristics of PTFE powder, after the initial pressurization to the set pressure and entering the holding pressure stage, the volume can still be compressed continuously. Once the volume is compressed, the pressure shall be reduced and the press will supplement pressure. Therefore, the pressure holding stage of PTFE product serves as a process of hydraulic system continuous pressure dropping and supplementing.
The stability of hydraulic press is realized based on years of application experience. Under the perfect coordination of high response of servo hydraulic PID and discharge flow of hydraulic oil circuit, the pressure fluctuation reaches almost zero.
For accurate pressure output, the hydraulic press engineers continuously optimize the hydraulic system and program. In application of servo system, sometimes a single PDI parameter is often not sufficient for the pressure range of the whole area. With the PID parameters set with low pressure, it will be still not applicable when reaching medium and high pressures.
After finding this situation in practical application, the hydraulic press combines with years of application experience, adopts multiple sets of PID parameters, corresponding to the multi-stage signaling pressure of the hydraulic press, and avoids the inapplicability of a single PID parameter to different pressure stages.
(3)After completion of pressing, the pressure relief time is controllable
For pressing of PTFE powder blank products, sometimes the pressure holding time takes dozens of minutes, with the purpose of obtaining a blank product with uniform density after reaching a certain compression ratio. However, after reaching the pressure holding time, in case of pressure relief instantaneously for some products, it is easy to cause the quality problem of hidden cracks inside the product.
To solve the problem of pressure relief, the hydraulic engineers have developed the function of slow pressure relief process and controllable time, and the pressure relief time can be controlled from several seconds to dozens of minutes.
For this, the pressure relief process can be considered as an inverse process of pressurization. During pressure relief, the pressure is output according to the time ratio for the purpose of reducing pressure until the final pressure relief in place. Conventional hydraulic presses have no such function.
(4)Convenient setting of process parameters
Adopt PLC + touch screen + servo drive control, for intuitive and efficient setting of technological process and parameters.
Most PTFE blank molding methods require two-sided pressurization + product demolding, and one product forming requires pressing twice + demolding once. However, the pressing parameters of the three times are not the same, and common hydraulic presses require repeated manual filling of different parameters three times.
Based on the special process of PTFE, the hydraulic press has compiled the parameter setting method for this process, allowing the customers to input parameters that conform to the product for one time, and the pressing can be completed with only operation controller. The operation is simple and fast, which reduce the probability of errors, improves reliability, and significantly reduces the technical threshold of operators.
For products that require to maintain pressure and exhaust for a certain period of time under different pressures to ensure transmission of pressure to all parts of the resin, it provides a free parameter setting function. (As shown in figure below)
For commonly used product parameters, after completion of debugging and passing inspection, it can be saved as a recipe, which supports one-key save and recall. (As shown in figure below)
(5)Energy saving and environmental protection
Common hydraulic presses produce large noises when working, which can easily pollute the production environment and affect the health of operators. The Datong hydraulic press adopts a servo motor as the power source, whose noise level is only about 70 decibels when working, and is almost silent under standby state. When operating, the torque is output according to the size of immediate load. The power loss is small, which can save 30%-50% of electric energy compared with common hydraulic presses, with significant energy saving effect.
Note that the pressing and holding time of PTFE powder blank products is long. For high precision, the user shall basically maintain the pump on and holding pressure. In this process, the servo motor system of the press only needs a dozen or so percent of output to conform to the pressure holding requirements. The hydraulic system produces less heat, reduces the cooling cost, and extends the service life of oil pump.
Common hydraulic presses require full speed output when the pump is on and pressure is holding. The actual utilization rate is only about 10%, and the machine is doing useless heating work for the rest time. The power loss is large, the energy utilization rate is low, and the oil pump service life of each hydraulic component is reduced.
04 Conclusion
For PTFE powder molding, accurate and stable pressure serve as the key factor to molding; for investment income, machines with energy-saving, energy conservation and environmental protection and high-utilization features are the key to cost recovery and realization of benefits; for operators, simple and efficient operation mode is the key point; the hydraulic press meets all the above key points, which can meet customer needs, and help customers solve problems from the root.